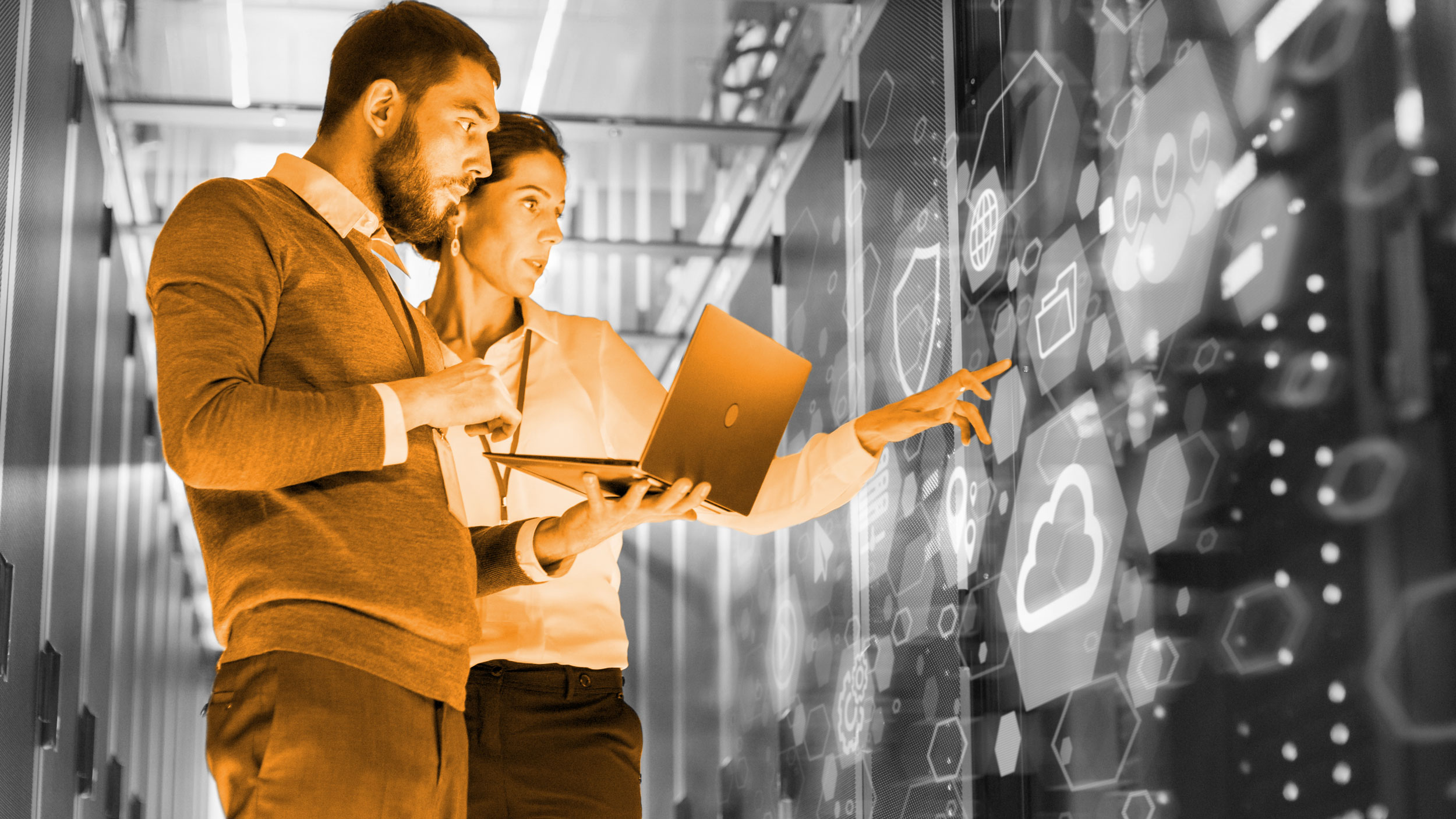
Engineering Management Office Transformation
Transport for London is a local government body responsible for the transport systems in Greater London. They provide pan-organisational engineering support for all modes of transport on the network, both over and underground.
The engineering directorate employs around 1,500 staff across 43 engineering functional capabilities who support the delivery of activities as varied as Skylines to Track, Ferries to Signalling and Underground Vehicles to Cycle Superhighways.
Key stakeholders in the programme included the Director of Engineering, Chief Operating Officer in Engineering, and the Chief Technical Officer in Engineering, as well as the Engineering Leadership Team.
The project objective was to create and embed a robust governance process across Business Delivery Areas, Functional Capability Pools, Technical Innovation and Executive Integration, and to establish an Engineering Management Office [EMO] to support the organisation in the development of the Engineering Operating System [EOS].
Following a recent organisational transformation, TfL had struggled to create a governance process that could consistently measure and highlight both positive and negative performance levels within the main business areas [Engineering Delivery, Functional Capability and Capacity, Technical Innovation and Executive Integration], and facilitate a strategic or ‘tomorrow’ view from these business areas.
This hindered their understanding and identification of, and accountability for, the problem solving activities required to provide effective Engineering outcomes for the wider Pan-TfL Business. There was also a need to provide robust and consistent engineering solutions for the London Transport system. An Engineering Management Office [EMO] needed to be established in order to co-ordinate and confirm the deployment and development of the TfL Engineering Operating System [EOS].
To meet the challenge, Project7 adapted, embedded and sustained the governance rhythm and heartbeat of the Engineering Directorate through the creation of a robust structure. This structure enabled the delivery of customer and stakeholder requirements, and developed the capability and understanding of the engineering staff at all levels to enable them to produce consistent engineering professional services.
Project7 also developed, mapped, designed, drafted & defined the implementation for the new Resource Management System [RMS]: TfLE’s ‘Keystone’ process. This involved completing a draft set of step definitions, KPI metrics, process confirmation and support systems documentation.
The Governance methodology furnished the Directorate with:
- Consistent and robust performance reviews of the ‘Matrix’ management organisation with actionable outcomes.
- A robust data architecture that enabled the Directorate to trend performance and become more able to respond quickly and appropriately.
- Over 90% of the functional capability pools demonstrated consistent and repeatable understanding and control of their organisational structure, current and future demand, and capability requirements.
- All four areas established consistent understanding and control of their delivery performance, budget vs actual head count and costs, future demand, and customer change impact.
- Better understanding and control of the Technical Innovation team’s discipline, including current challenges and risks, and activities to support future
- Executive integration showed good understanding of current and future challenges within the directorate and co-ordinated the timely decision-making processes required to alleviate these challenges.
- Highlighted middle management talent, which will underpin the Directorate’s future growth.
- An improved change control process was introduced, delivering more accurate forecasting and resource delivery.
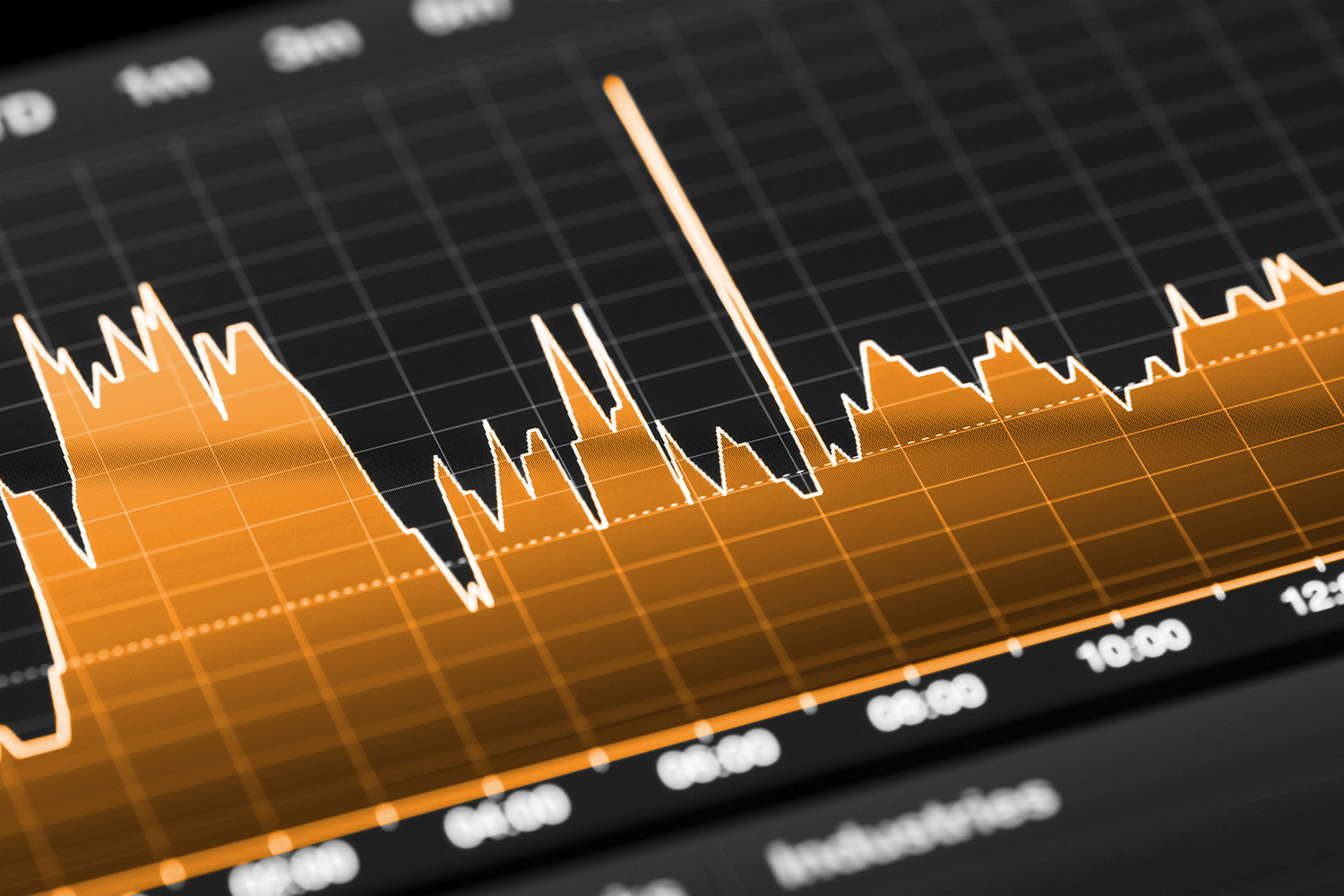
Portfolio Level Resource Optimisation
The London Underground [LU] is a public rapid transit system, serving London, in the United Kingdom. The network comprises of 11 lines, and carries approximately 1.34 billion passengers a year [4.8million per day], making it the world’s 11th busiest metro system, employing circa 24,000 people.
The performance and reliability of LU is key to enabling it to deliver the customer promise of ‘Every Journey Matters,’ and is ultimately vital to the safe and effective operation and growth of London more widely.
LU reliability performance had been worsening since 2016, following a sustained period of improvement since 2011. Recognising this, the Managing Director of LU, and the wider LU Executive, commissioned a reliability improvement project to ensure it as meeting the level of performance committed to in the Transport for London [TfL] Business Plan.
Five work-streams were identified that were having a significant contribution to worsening network performance; Staff Availability [absenteeism] in Line Operations was one of the five workstreams.
Poor absenteeism manifests itself in cancellations, lost customer hours, as well as increased cost equating to £48M per annum.
Following an initial assessment by Project7, it was identified that there were 3 main causes for the issue of Staff Availability;
- The Attendance at Work Policy, which was not sufficiently robust to sanction those employees who are unable to sustain attendance.
- Use of the Policy by key stakeholders, such as Operations and HR, was such that standards of dealing with employees at various stages in the process was not timely enough or consistent.
- The capability level of managers to deal with these issues was not at the required standard.
To establish the current state, Project7 began by conducting a deep dive into absence cases, reviewing touch points throughout the absence process, including adherence to process in parallel with the mindsets, capability and behaviours of the people using and managing the process.
A pilot Visual Performance Management process was designed, developed and implemented in the worst performing area. Lead and lag metrics were identified, defined and used as part of the Visual Performance Management process. Area Leaders were coached in how to conduct regular performance dialogues with their teams, and structured problem-solving techniques were used to address gaps in performance. As a result, absenteeism fell by approximately 7% from 16% to 9% over an initial 12-week period.
A Project Management Office [PMO] was then established for Line Operations to coordinate and provide overall governance for the improvement programme, with a weekly cross-functional team meeting. A standardised Tiered Visual Performance Management system was designed, developed and deployed across all of Line Operations to create transparency and a forum for teams to review, drive and improve performance of staff availability.
Whilst the project was initially aimed at train operators in Line Operations, it became extended into Customer Service and Asset Operations to provide a standardised approach across the business.
Project7’s ability to work vertically [from executive to front line] and horizontally [operations and professional services] within the business, to initially establish the current state and then to maximise sustainable change through people and process, resulted in significant performance improvement.
Overall staff availability results for train operators in Line Operations, where the number of employees on restricted duties, was 85 [2.4%] against a target of 52 [1.5%]. The programme resulted in the number of restricted employees reducing to 35 [1%], a 58% improvement with a cost avoidance salary wise of £2.4M per annum, after the first 9 months. The success of the project has resulted in a £15.4m cost avoidance total; equating to a 64:1 Return on Investment.
- The overall number of employees off sick across the network reduced by 14.2%. Equating to a £2.4m cost avoidance in salaries.
- The reduction in lost customer hours has provided a cost avoidance to date of £5m, with a projected annual customer benefit of £13m.
- The £15.4m cost avoidance equates to a 64:1 Return On Investment.
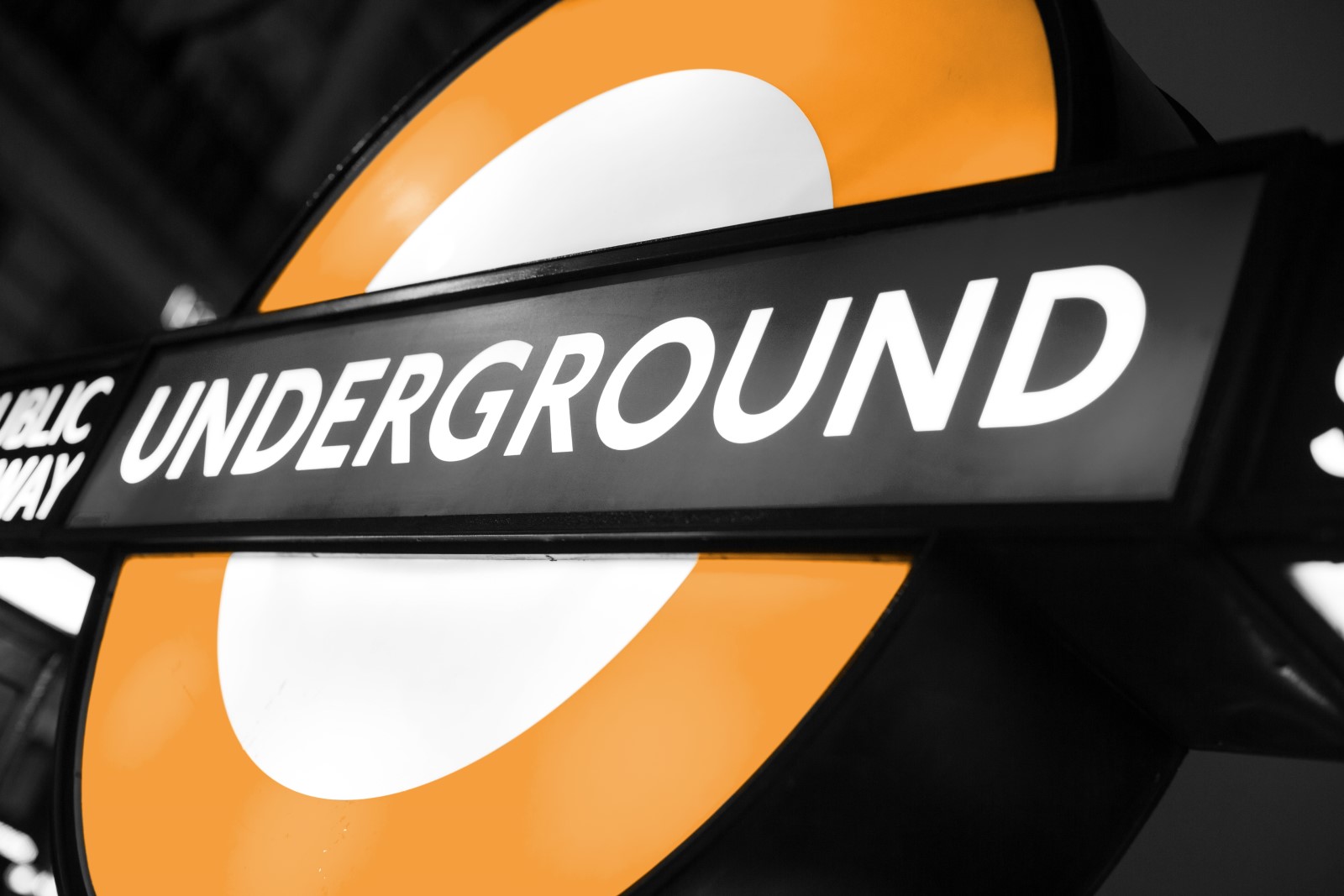
Central Line Depot Visual Performance Management
The London Underground (LU) is a public rapid transit system serving London and parts of its adjacent counties. The network comprises of 11 lines, and employs around 24,000 people. The performance and reliability of LU is key in enabling it to deliver its customer promise of Every Journey Matters, and is ultimately vital to the safe and effective operation and growth of London more widely.
Following the launch of the LU Visualisation Process, as part of the LU Reliability Improvement Programme, it became clear that there were significant opportunities for improvement of asset reliability on the Central Tube Line.
Project7 Consultancy were engaged to assist the Central Line Fleet Maintenance Depots with the development and establishment of an effective visual management system.
A scoping review was completed across Central and Victoria Line Maintenance Depots, focussing on their Visualisation processes.
The review determined a list of observations and recommendations for the enhancement of Visualisation, to drive availability and reliability of fleet assets in service.
Within the entire LU network, it is the Central Line fleet that suffers the most in terms of reliability. This is true for both the number of ‘Lost Customer Hours’ (LCH) and the ‘Mean Distance Between Failures’ (MDBF). The actual number of faults reported per week on the Central Line is around 5 to 10 times that of other lines.
The review of the existing Visualisation activities at the Central Line Depots had identified:
- White Boards were not in use
- Electronic Vis Data integrity was not trusted
- No clear link between Asset Functional Vis and local priorities
- No discussion of gap between performance and target
- No visual representation of ‘Reliability’ issues on fleet
- Action recording poor and tracking non existent
- No evidence of escalation
This was creating a number of problems:
- Difficulty in understanding daily priorities
- Firefighting of repeat issues
- Lack of resolution had become the norm
- The same people discussing the same problems every day
- Missing performance targets had become the norm
However, a number of opportunities to accelerate the establishment of the visualisation process were now available.
In order to overcome the challenges identified during review, and due to the limited time available for the new Visualisation system to become established, it was determined that an emphasis on skills transfer, relating to the principles of Visual Management should form part of the wider programme.
The programme for the re-introduction of the Visualisation process and structured meetings at the Hainault and Ruislip Maintenance Depots included the following activities;
- Alignment of the depot Visualisation to Fleet Functional and Asset Operations Visualisation. Specific care was taken to ensure that the focus of the visual management activities within the Depots were aligned effectively to the wider KPI cascade; covering all 6 of the KPIs and each of the agreed Hot Metrics. A top level Depot Performance board was established at each site to ensure that this was the start point for all Visualisation activity.
- The overall scope and content of the Visualisation materials at each site were designed to underpin the top level KPIs & metrics being managed. Each of the KPIs would be underpinned by Visual Management Boards, able to support decision-making, and capable of influencing performance in an appropriate way.
- The actual design of each Visualisation Board aspired to enable effective decisions to be made ahead of a potential problem being realised. The general objective was to provide a ‘2 week’ forward view of operational requirements and a visual representation of capabilities and capacities, so that risks could be identified and addressed ahead of their causing damage to performance.
- Daily Visualisation meetings were introduced, reviewing planned operational demands and progress during the previous day, and readiness for Night Shift working.
- Full review of meeting governance was undertaken at both depots, including external meeting and/conference call requirements. An optimised process of operation for the meetings was defined and displayed within the Visualisation meeting rooms. Daily coaching of the meetings was undertaken, supported by formal use of the Visualisation Process Confirmation system to continuously improve meeting effectiveness and sustainability.
- A good level of skills transfer in the principles and establishment of Visual Management systems was achieved with the key management team figures at each Depot and the nominated LU Improvement Team representative.
The dramatic improvement in the ability to identify and respond to upcoming concern is expected to deliver real and meaningful operational performance results, within the next few months. Decisions are already being made that are affecting performance, and preventing problems that
would inevitably have impacted on performance.
As a result of P7’s implementations, the level of teamwork and interaction across Depots has improved significantly. This is particularly evident where departments had previously withdrawn completely from the morning meeting activities, and are now playing an active part in promoting
the contribution they make to the effective operation of the Depot, getting involved in helping other areas solve site level performance problems.
Following the Visualisation project, significant deliverables for the Client have included:
- 50% increase in the level of alignment of local Depot performance measures
- Regular review process; of all 6 KPIs
- 80:20 alignment objective comfortably achieved
- 100% compliance with the delivery of the daily operational Vis meeting (no cancellations)
- Excellent meeting attendance; 90%+ compliance
- 26% improvement in scores achieved against Visualisation Process Confirmation score sheet
- Level of compliance with the targeted skills matrices’ requirement standards, increased by 33%
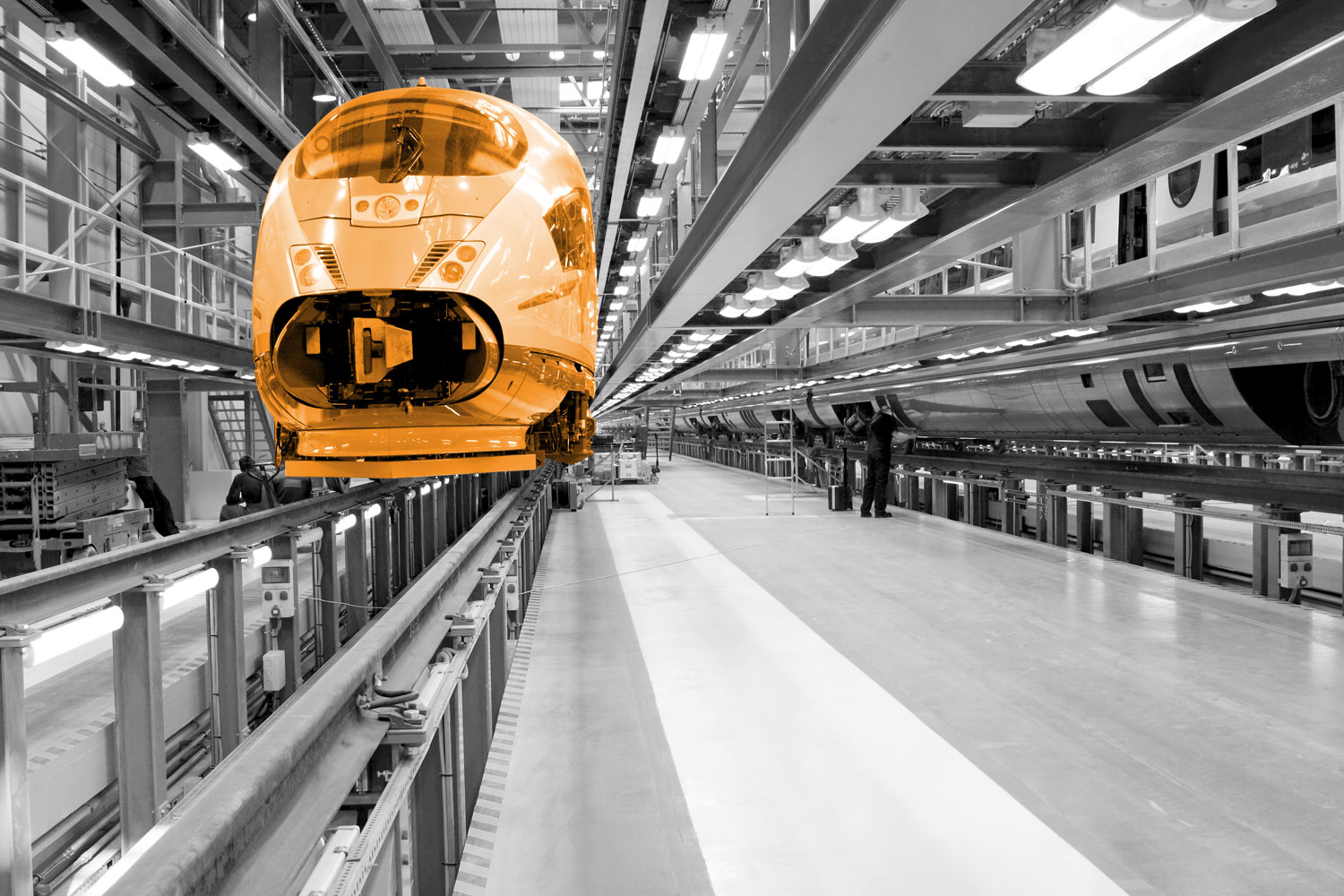
Depot Improvement Project
Newton Heath Train Maintenance Depot maintains 40% of Northern Trains Ltd [NTL] fleet, this makes it the largest maintainer across all 4 Depots within Northern Rail Limited, with a maintenance establishment of up to 300 staff inclusive of contractors.
Key stakeholders from within the organisation included, Depot Manager, Depot Production Manager, Production Depot Managers, Plant and Maintenance Managers and Stores Manager.
Northern was in the process of establishing a new Maintenance Facility planned to come online Mid 2020. The client identified areas within the Depot that required support to improve performance, introducing new ways of working including the incorporation of the Engineering Operating Model that Project7 had been introduced at other Depot locations across NTL.
Project7 was selected as the Partner of choice to support the client through the Project Management of the Depots readiness for transferring into the new facility.
The key motive for this project stemmed from the lack of in-house improvement experience and capability within the company – a significant challenge that was preventing the client from delivering a full Lean programme, necessary to achieve the desired savings and cultural improvements targeted, across a large scale workforce.
For many years, client had trialled numerous options in an attempt the establishment a high performing Continuous Improvement [CI] culture – with limited success. One of the main causes was the lack of dedicated teams to support and drive CI improvement.
The organisation was left with a high number and variation of projects and improvement ideas but had little to no structure in place for the required changes to be successfully integrated into the business.
Partner of choice:
- Project7’s demonstrable experience, success and trusted methodology for creating an internal capability coupled with our direct hands-on coaching approach were the main contributing factors for selection and being chosen as Northern Trains partner of choice for this programme of work.
In order to overcome the challenges within Northern Rail, Project7 designed and supported the implemented an Operating Model.
Project7’s coaching and implementation of the Operating Model supported the development of leaders in Lean Leadership behaviours, whilst leading, coaching and guiding the client through the introduction of the new ways of working to create a high performance culture that would create the foundation for excellence on moving to the new facility.
- Delivered 5S Workplace Organisation training, to Northern staff, including train the trainer for ongoing training, to enable Depot to become self-sufficient in delivering Workplace Organisation training
- Implemented 5S Workplace Organisation within the Depot
- Developed pre & post shift routines, to ensure smooth start-up of production
- Created T Card system to support process confirmation, working with teams to understand core daily tasks
- Delivered Level 1 problem solving training to support root cause identification
- Level 2 Practical Problem Solving training, and coaching stakeholders through the process
- Process mapping workshops on a number of processes, to understand what actually happens and identify improvement area’s through gap analysis
- Visual Performance Management, set up a tiered system that supports the 3 levels within the Depot to drive performance
- Project management ensuring Depot Mobilisation and readiness for new shed
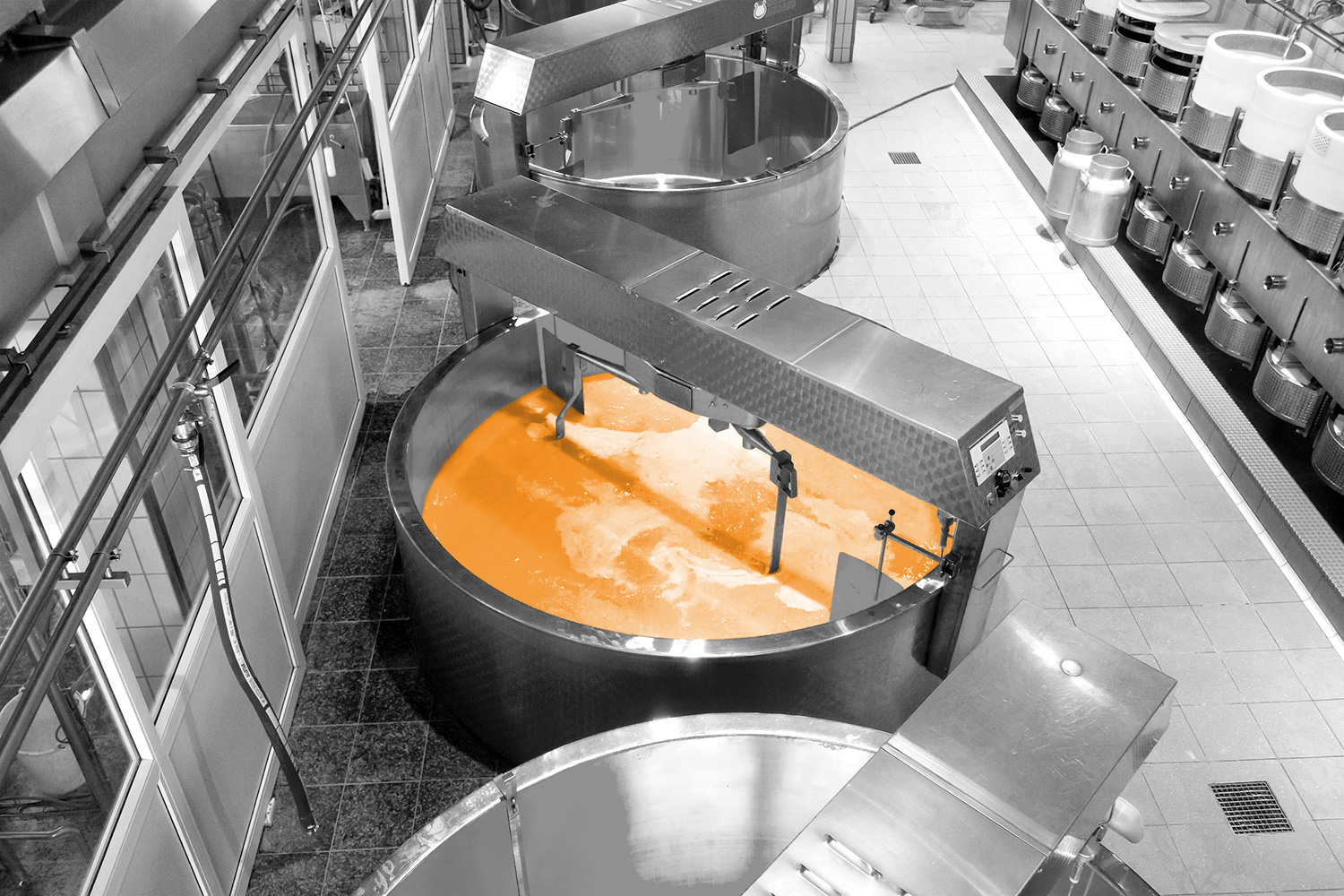
Quick Change Over
Our client is the UK’s leading ‘Food to Go’ business; based in Southall, London. With an annual turnover of £250m, their unrivalled portfolio includes some of the biggest brands in the UK retail and foodservice industry.
Project7 commenced engagement with the client to design, implement and coach a Standard Operational Procedure that would provide a stable output from production to processes, and maintain sustainable performance levels, positively impacting on productivity, consequently
resulting in increased efficiency levels as well as developing employees’ capabilities with specialist training; enabling substantial process improvements to the production line and Flow Wrap Machine process.
To achieve Quick Change Over (QCO) on the Flow Wrap Machine on Production Line 5, Project7 incorporated significant changes to operations, engaging the nightshift operational team and machine minders.
Before Project7 began the process of developing a Lean Standard Operational Procedure (SOP), a one week QCO study was conducted to define the current state of the recently installed Flow Wrap Machine, in order to identify the necessary improvements. This study helped to determine the losses that had been responsible for causing a bottleneck in the production flow, consequently impacting on efficiency and productivity levels.
The study revealed the level of losses, timed from changeovers, to running at around 20 minutes. Losses were occurring post-setup of the machine and post-changeover of the products.
Team brainstorming, between nightshift operational leaders and machine minders, established several possible causes for these losses. Two predominant reasons were the low training levels amongst machine minders, who lacked experience in the new Flow Wrap Machine configuration settings and technology. Particularly, the pre-set programme software which was challenging individuals’ production knowledge. Secondly, the absence of a formal procedure and process standards was causing confusion for employees and inconsistency within production.
A process confirmation tool was required to improve communication between shift leaders, and remove the significant variation in the process and resulting losses on the production line. With experienced Machine Minders having left the company, current Minders desperately needed process standards for their development and training in the new Flow Wrap machinery.
With these key issues considered, Project7 designed and implemented a series of standardised procedures for the Flow Wrap Machine Changeover; detailing the exact steps to be taken during the changeover process, along with operating descriptions to carefully instruct staff, key points and precise timings. This was further accompanied with diagrams and examples to visually demonstrate the step-by-step process to staff.
Coaching and specialist training was also provided for all Machine Minders, Line Leaders and Production Managers in both the newly-devised Standard Operational Procedures and Flow Wrap Machine technology, to bring all employees to the same standards in all aspects of the Flow Wrap process and to coach them on the latest settings and programmes. This also included further indepth coaching by an Engineer from Fuji.
Standard Operational Procedures are now used as a process confirmation tool to help maintain productivity levels. Production Managers, Line Leaders and Manufacturing Managers now contribute their feedback and data to a Process Confirmation Board that captures a live overview of production line data, on a daily basis. This data is then added to an Operations Board, which measures productivity and lost time, and is used as a focal point in Short Interval Control management meetings. This helps to significantly enhance team communication and enables a smoother running-condition. As a result, productivity and efficiency levels have increased dramatically, cutting changeover times and halving losses.
These implementations have not only improved direct productivity and efficiency results; they have enhanced team communication, and ensured that continuous improvement is maintained for the production line.
Lessons Learnt
- Regular coaching is vital in order to keep all employees up-to-date with new technologies and specialist knowledge.
- Standard Operational Procedures (SOPs) are crucial to ensuring everyone is working in the same way, following the same processes; resulting in improved productivity, efficiency and smoother- running condition.
- Identifying the possible causes to challenges and brainstorming as a team is important when focusing on key priorities and improving communication.
- Data capture helps to monitor losses and maintain a continuous improvement process.
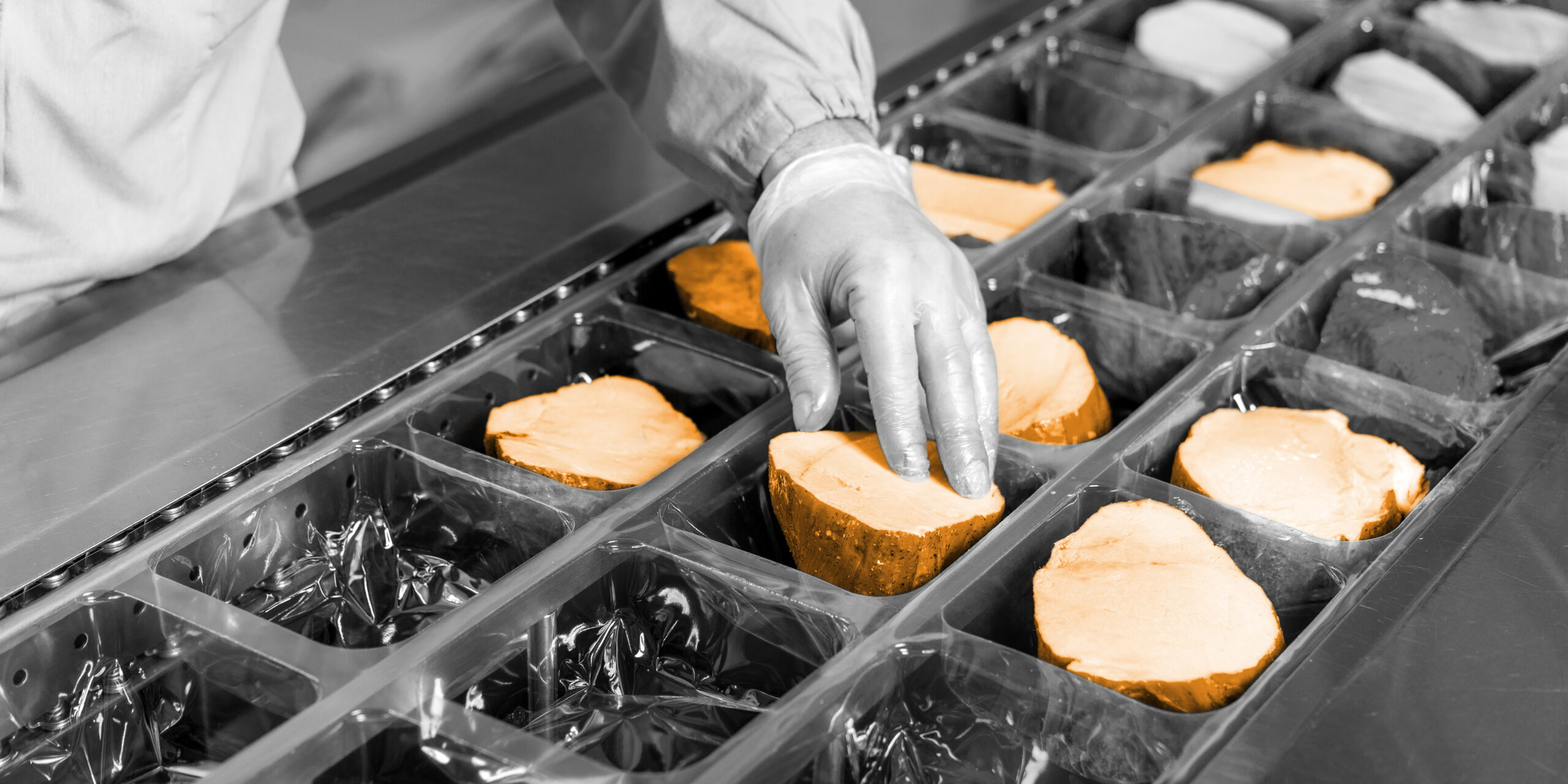
Lean Leadership & Line Performance Improvement
Our client is one of Europe’s leading food producing companies who produces and processes high-quality beef, pork, bacon and chicken, as well as a wide range of convenience products and added value cooked meats, for leading retailers across the UK and internationally.
Its UK operation has extensive facilities, located across the country – from farms and hatcheries to primary production, processing and packaging factories. The organisation supplies its products in response to customer and market demands, primarily focusing on the UK retail market, while
also encompassing major foodservice and wholesale clients within its portfolio.
While positioning our client as the head of operational excellence for the UK, an analysis of facilities across the UK revealed that the company were facing several major problems concerning operations and performance; resulting in a significant loss of money across sites. The initial application site sliced cooked meats plant, in particular, was enduring a weekly loss of approximately £195k.
Upon observation, the skillset of both operational and functional managers required vital improvements; in order to be able to effectively identify waste levels within existing processes.
The layout of the factory floors was also proving inefficient – with a high level of raw waste materials, and a lack of visual controls in place to help monitor movement of materials and priority settings. Further problems included suspect quality standards and a high number of customer
complaints.
Although the company had previously attempted to resolve elements of these challenges through the implementation of lean foundation toolsets; low engagement between operations and cross-functional teams, combined with a lack of ownership, meant attempts at performance improvements had proven unsustainable. This was due to the directive style of management and ideas not being encouraged at shop-floor level, significantly impacting on delivery of important cost metrics.
Identification and removal of waste, development of employees and robust operational processes were urgently required in order to drastically reduce costs and enhance line performance
With these challenges driving the project, Project7 intervened to design, develop and evaluate an effective pilot Lean Leadership Programme – initial application within one of the major operating sites, and progressively expanding across the majority of UK sites.
The scope of work encompassed several key areas:
- Design, delivery and evaluation of a Lean Leadership Training Programme
- The development of the facility layout plan and specification for a Lean Leadership Academy at the sliced cooked meats plant [initially]
- Execution of Line Performance Improvement projects at initial application sites
- The strategic deployment of the company operating system model
- Full coaching of the operating system central team, to co-deliver all of the above
The Lean Leadership Academy programme [LLA] was deployed and completed over a three-week period; addressing 52 operational leaders, covering technical, engineering, logistics and HR fields – enabling Line Performance Improvements [LPI] across a total of seven sites.
A sustainable timing, resource and investment plan was carefully developed, and incorporated into routinely review meetings – occurring at daily, weekly and monthly intervals. Milestones were established with flexibility, in line with our clients’ requirements, and project process reports were
formulated on a weekly basis to detail budget delivery across project timelines.
Together with P7’s implementations, our client invested in forming their own continuous improvement team – allowing relationships between teams to form quickly and be easily maintained.
P7’s intervention has led to a significant improvement in Leadership and Line Performance, including;
- Cost Saving Value of ideas raised and implemented through Value Stream Mapping activity = £991.6k
- Implementation of site tactical initiatives resulted in saving of £2.4m across seven sites
- Reduction of 66% in financial weekly loss at the initial application site
- Gold Standard Accreditation for food factory – enabling engagement with, and production for Marks & Spencer
- 60% reduction in customer complaints
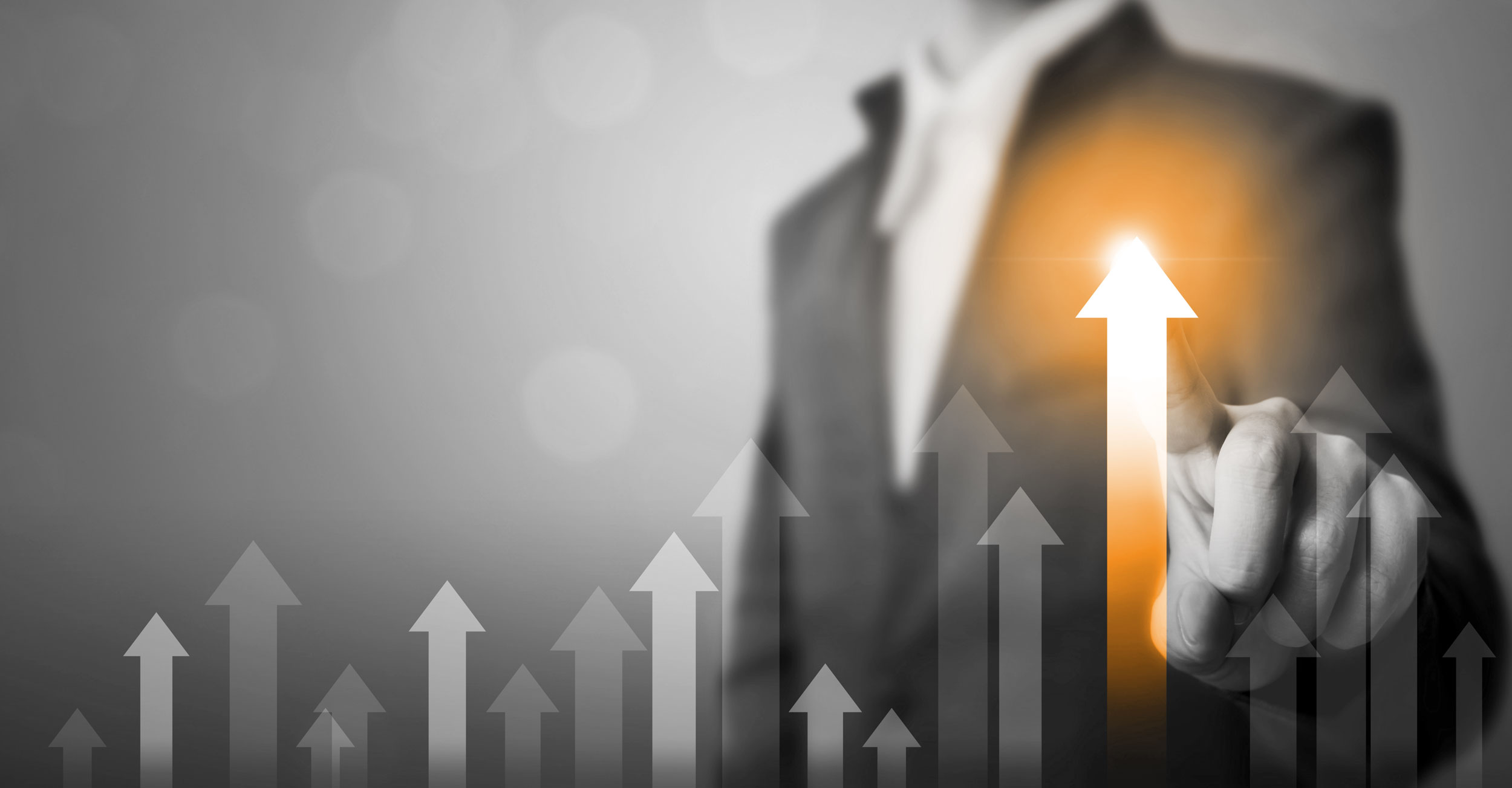
Structured Continuous Improvement
London North Western Route [LNW] is the largest of the Network Rail routes within the UK, running services from Euston and Marylebone, through the midlands, Birmingham, Liverpool and Manchester, up to Carlisle.
The Route employs a workforce of over 7000 staff across all the main disciplines of Maintenance and Asset Management, as well as Renewals and Infrastructure projects. With over 4500 miles of track, LNW represents 24% of the entire Network Rail organisation.
Key stakeholders from within the organisation included the LNW Route Executive Team and Route Managing Director, as well as a host of senior managers throughout the enterprise.
The project was part of the overriding Network Rail strategy to introduce a Better Every Day culture through structured Continuous Improvement. An initial figure of £300m in efficiency savings was introduced. LNW’s strategy was to be best in class for its Network Rail operations division.
When we first looked at our efficiency target and our goals regarding lean, we first thought we wanted the course to simply wipe its face; so what are the costs going to be for Year 1 and Year 2, could we realise those costs and bring them out our bottom line – we quickly hit those targets within about 9 months of starting our course! Since then we’ve moved on and actually found savings month on month, and have exceeded all previous targets. It does exactly what it says on the tin.”
– Jamie Cowan – Special Projects Manager at Network Rail
The key motive for this project stemmed from the lack of in-house tools and skills within the company – a significant challenge that was preventing the client from delivering a full Lean programme, necessary to achieve the desired savings and cultural improvements, across a large scale workforce.
For many years, Network Rail had trialled numerous options to attempt the establishment of a Continuous Improvement [CI] culture – with limited success. One of the key root causes for this was the lack of understanding of CI culture at an Executive level, in order to be able to not only sponsor, but to understand the key strategy, in turn gaining a sustained momentum of CI.
The organisation was left with a high variation of projects and improvement ideas that had little to no structure in place for required changes to be successfully integrated. Analysis of Alternatives:
- Initial discussions led to the development of a strategy and basis for a full tender process.
- The LNW Executive selected six tenders for full review and representations.
- Project7’s four-step approach and direct hands-on coaching methods were the main contributing factors for selection and winning the contract award.
In order to overcome the challenges within LNW, Project7 designed and implemented a solution, centered on their four-step Knowledge Transfer approach; which would improve awareness and provide coached training across all 408 of LNW’s key personnel. This initiated a roll out of “Lean” activities across each of the Route’s disciplines and departments.
Project7’s solution did not only provide some the UK’s leading experts, but facilitated a robust selection of early adopters to Lean from within LNW. A full program of learning through doing, in real time, with 100% full time coaching and mentoring support to the chosen delegates, ensuring the most effective knowledge transfer possible.
Implementation was split into 3 primary focus areas:
Part 1
The creation of 35 5-day Lean Learning Academies, scheduled over two years, to support the overall Knowledge Transfer programme, and provide a base-level understanding for the top 408 LNW Managers selected.
Part 2
The selection process via the Project7 four-step approach, ensuring that the delegate in question was well-informed and prepared for the learning and activities going forward.
Part 3
The Lean Learning Academy [LLA] itself with the selection and ongoing support for the delegate to work in real-time, within the business, incorporating a “Lean” workstream to support and develop the learning, as well as demonstrating to others within their teams the behaviours and techniques used to enforce both significant and sustained change.
As a result of these implementations, the initial savings target was met within the first 9 months of engagement. This target has seen month on month growth ever since.
Initial concerns with the proposed solution included incorrect selection of delegates due to understanding not being fully integrated amongst Executives. The Project7 Step 1 process quickly identified this issue and through further robust reporting was able to gain better control of up and coming candidates.
Gaining support from the Finance community was also an initial concern with the project; LNW had formerly been unable to model or understand the impacts of Continuous Improvement and waste removal, in terms of hard savings and cost avoidance. Attendance of Finance personnel on the LLA itself support the understanding and the key role which the Finance department fulfil. Further reporting systems were developed and financial trackers and calculation models were created to verify the savings to date.
Early adoption of both Finance and HR are critical in securing support for change and identifying how initial verified savings encourage further change and support sponsorship.
- To date 260 managers completed the LLA, with over 210 Lean work streams in place.
- Strengthened LNW reputation with leading customers.
- ROI of £10.4 million to date, with a further £37 million identified for the next 18 months.
- Best reliability figures in over seven years, with Virgin Trains performance at its highest to date.
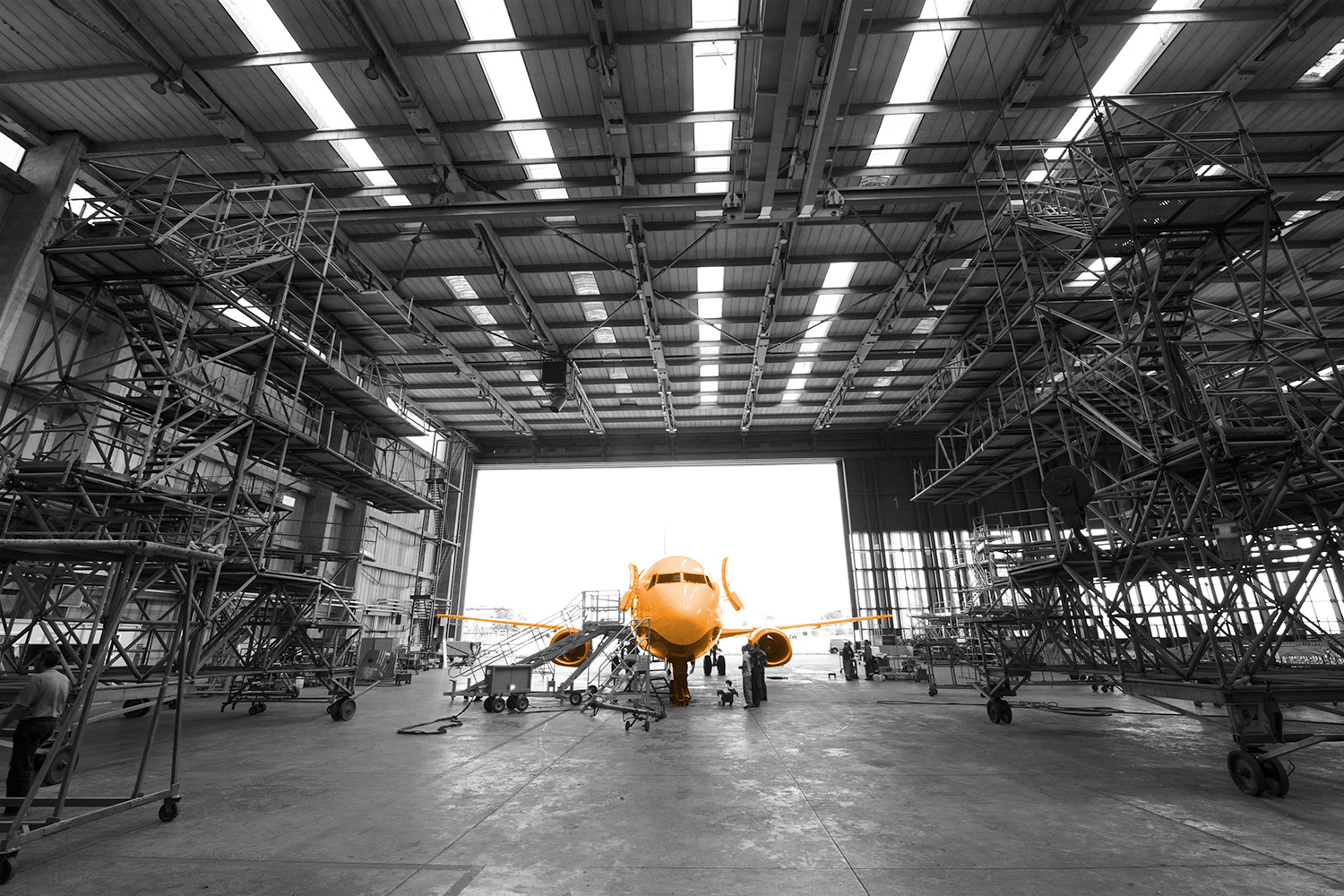
Creating a High-Performance Culture
Our client, Airbus, is the largest aeronautics and space organisation in Europe. As a global leader in manufacturing aircraft, the company is home to the most modern and comprehensive aircraft family in the world.
As part of a funding initiative facilitated by AIDT Workforce Development, funded by the Alabama State; Airbus US Final Assembly Line [FAL] approached Project7 [P7] with a major change programme concerning their workforce performance culture. Having previously worked with P7 on a successful project in Canada; a trusted relationship had already been established with the client.
The recently appointed General Manager, of a brand new Final Assembly Line facility in Alabama, was confronted with several issues. The facility was facing the challenging transition from a facility build phase, constructing two aircrafts per month to test capacity, to a fully operating Final Assembly Line producing four aircrafts per month – whilst losing the temporary expat expertise provided from Europe, and without significantly increasing employee numbers.
This change programme was essential, in order to maintain the Airbus Strategy to;
- Increase US market sector growth
- Meet committed increase in production volumes
The key challenges for Airbus, Alabama included;
Transition from experienced European Airbus employees to new, inexperienced US employees
- Airbus Operating System; the manufacturing maturity assessment level of deployment was
assessed at scoring D with a target condition of A. - A recent Employee Engagement Survey revealed 60% of base-level employees rated Leadership
as either Average or Poor. - 40-50% of the planned workload was being moved [travelled work] to the next workstation for
completion; instead of being completed at one workstation.
Our Client desperately needed to address Leadership issues, relating to both employee and material management within the workstation. Currently, the facility was working in ad-hoc ways to achieve final assembly of aircraft build; neglecting the formalised systematic approach – vital in organising materials, tooling, processes and people.
Although Senior Management were aware of the systematic methodologies, they were not being utilised or deployed – impacting all levels of the workforce. This left front line, value-adding employees without the necessary knowledge and awareness; which would be key in establishing a high-performance culture.
A reduction in out of station travelled work was also crucial, in order to cut costs and gain improved performance levels.
In order to overcome these key challenges, P7 were assigned with designing, implementing and evaluating a world class operating system through 4 levels of the Airbus, Alabama organisation.
This Solution would enable the effective delivery of aircraft; meeting quality, schedule, cost and safety – every time, in turn creating a high-performing culture.
P7’s Solution consisted of the seven steps of the P7 Way:
- Strategy into Action
- Tiered Visual Performance Management [VPM]
- Short Interval Control & Performance Dialogues
- Performance Confirmation & Go Look See
- Setting Clear & Aligned Targets; Problem-solving Level 1
- Coaching for Success; Problem-solving Level 2
- Talent Management and Leadership Development
Having carefully adapted these seven steps to the Airbus Operating System; the P7 Way was closely aligned with Airbus’ core principals in mind. This naturally fuelled the success of the implementations; providing the necessary focus to meet and go beyond the required standards. In order to unravel the complex structure of the diverse and highly technical organisation, P7 incorporated two additional tools/techniques into the working environment, including the RACI Diagram and ICOR Chart. This facilitated a significant breakthrough in the project’s success and enabled improvements in the identification of employee roles, tasks and timescales; further supporting the project’s implementations.
Despite the success of the project’s implementations, P7 recognised an over-estimation in the local knowledge of the new workforce in the Airbus Operating System standards. With hindsight, slowing down the pace of the implementations, extending the length of the project or employing extra team members may have helped further boost improvements.
As a result of the coaching and implementations deployed by P7; Airbus US FAL have achieved:
4 levels of tiered Visual Performance Management [VPM] fully integrated into Airbus daily
governance processes creating a World Class Operating System.
- 40% reduction in Travelled Work from station to station – enabling the first ever clean aircraft build within workstation.
- An increase from D to B in the Airbus Operating System Maturity Assessment [Six categories move to B and two to A].
- A positive swing in the Employee Leadership survey results on Leadership; moving from 60% below average rating, to 60% above average rating.
- $2.4 billion in annual sales by moving from two aircraft delivered per month to four aircraft delivered per month.
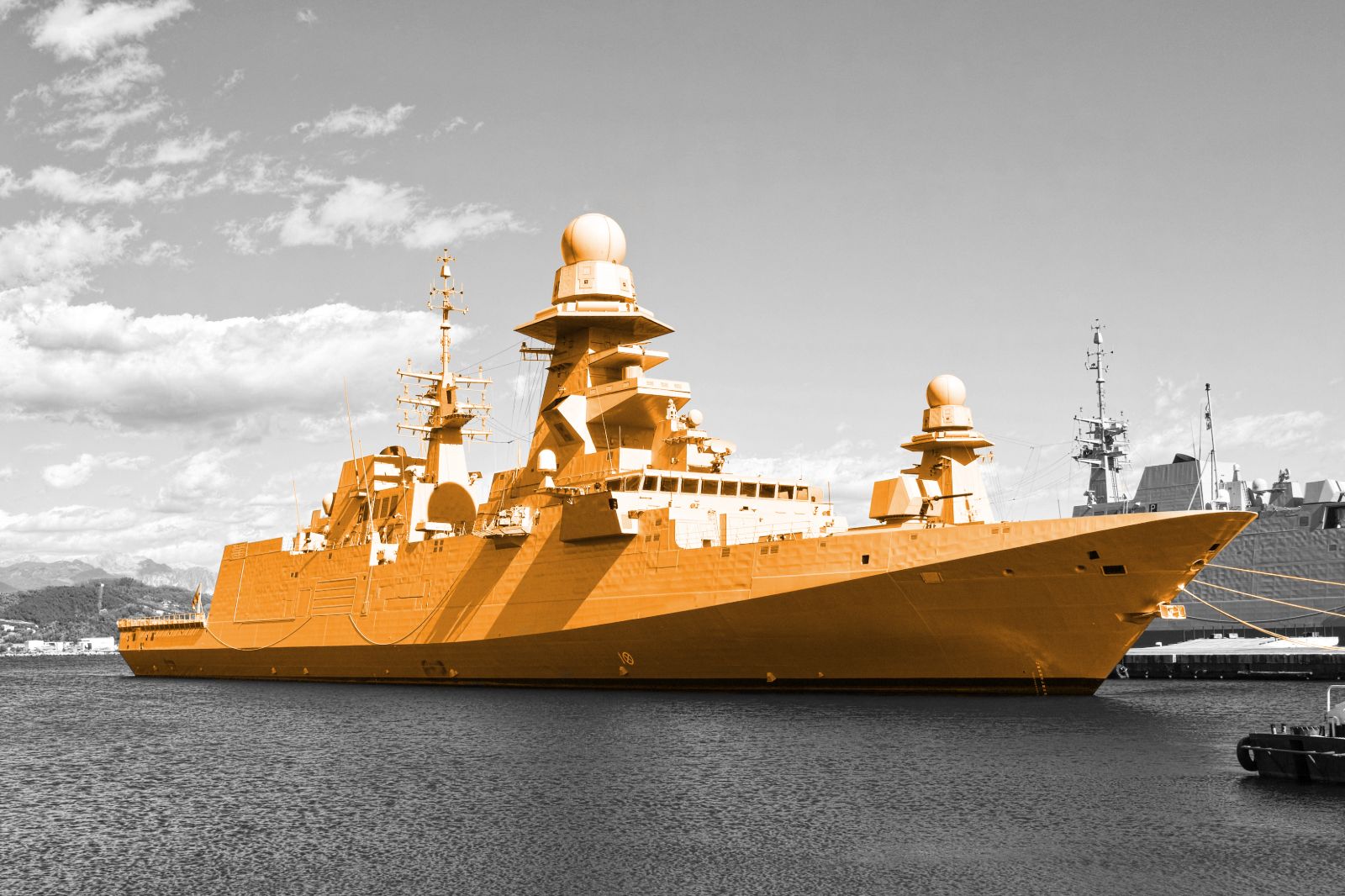
Organisational Design and Appointments
BVT Surface Fleet, the result of the merger of BAE Marine Systems and Vosper Thorneycroft, specialise in naval shipbuilding and combat systems integration – as part of a joint venture company.
It was noted that the organisation may have a number of synergies within the organisation structure that could prove to be inefficient or uneconomical. For this reason, the BVT organisation engaged the services of Project7 [P7] in order to streamline their processes and remove inefficiency.
Key stakeholders from within the organisation included the Group Operations Director, Operations Director, Group HR Director and site HR Directors, as well as a host of other senior managers across the three sites.
Following the merger, BVT had little experience of, or in-house resources for, conducting an organisation design programme.
Key objectives required of a reorganisation included:
- Supporting the aim to become a single unified business
- Fostering innovation through a diverse team, with a balance of business systems managers from different sites, backgrounds, etc.
- Considering the use of unconventional structures to enable agility, such as task forces, dual responsibilities, broad roles, etc.
- Being agile, flexible and able to transform further to meet the businesses needs as they evolve
- Delivering an organisation that supports business contiguity, enables integration and delivers savings
In order to plan the project, the following key stakeholders were identified:
- P7 – to design, manage and facilitate the project.
- Support functions [HR, Finance, SHE, Strategy, Commercial] – to provide services to delivery areas such as Operations. These functions are responsible for: developing processes in line with the strategic intent of the business; ensuring sound governance, especially regarding resource planning and deployment; and synergy savings across all of their own activities.
There were a few options available to them team:
Option 1 – Do nothing; continue to operate as they were, which would likely result in a higher resource level than required and with poor performance from personnel who not only fail to add value, but hinder other team members.
Option 2 – A arbitrary % cut in headcount. While many organisations do opt for this when they believe their organisation has grown to a level which may not be effective or economic, it creates a risk of losing effective and essential employees.
Option 3 – Create an Organisational Design & Appointment Process within the Economic and Effective [E&E] Framework. Change – whether it be technical, political, economic, legal or organisational – requires a systematic approach and a degree of rigour applied to it.
The recommended solution was to create an Organisational Design & Appointment Process with the E&E Framework.
P7 were engaged to conduct an Organisational Design and Appointments [OD&A] Project in order to define an economic and effective [E&E] business for BVT Surface Fleet, within its three sites at Portsmouth, Scotstoun and Govan.
The project began by analysing the existing situation of the organisation. The current organisation charts, job descriptions, operational processes, operational interfaces and personnel performance were studied and captured. Following this stage of the process, the design phase was initiated to provide a pragmatic solution that would transform the business into an economic and effective
organisation.
The OD&A project utilised an E&E process based upon lean thinking design principles around industry best practices, in order to deliver the objectives outlined below. These principles were created to facilitate the development of an organisation that would best enable the achievement of the business’ strategic aims.
The process was split into three defined phases:
Phase 1: Defining the design principles to support the business concept and aims [60 days].
This included:
- Demonstrating a reduced management overhead in support of the overall synergy savings target
- Establishing delegation of authority to enable agility and empower managers to deliver rapid decision-making
- Understanding the geographical constraints and acknowledging that the business may be split over multiple sites
- Considering the practicalities of managing people and the associated travel time and cost
- Driving efficiency through optimum spans of control, avoiding 1:1 or 1:2 reporting lines in favour of 1:6-8 reporting lines for management and 1:12-15 for operatives
Phase 2: Mapping the existing [As Is] structures and designing the proposed [To Be] structures [60 days].
Phase 3: Implementation of the proposed design [90 – 120 days]
As a result of project support from P7, the Client experienced a split impact for Operations in the North [Scotstoun & Govan] and the South [Portsmouth].
Operations in the North:
- As Is: Nine levels, with a span of up to 1:22 and a total headcount of 1023
- To Be: Five levels, with a span of 1:6-8 and 1:12-15 and a total headcount of 903
- A reduction of 120, equalling total savings of £3.9m
Operations in the South:
- As Is: Ten levels, with a span of up to 1:25 and a total headcount of 2963
- To Be: Five levels, with spans of 1:6-8 and 1:12-15 and a total headcount of 2716
- A reduction of 247, equalling total savings of £10.8m
The To Be implementation was phased in over a 24-month period to mitigate risk through the transition period.
Integrated work team managers were upskilled to enable them to become more agile and remove the need for area managers. The creation of a more agile workforce enabled the organisation to become more competitive within the market in order to meet its strategic objectives.
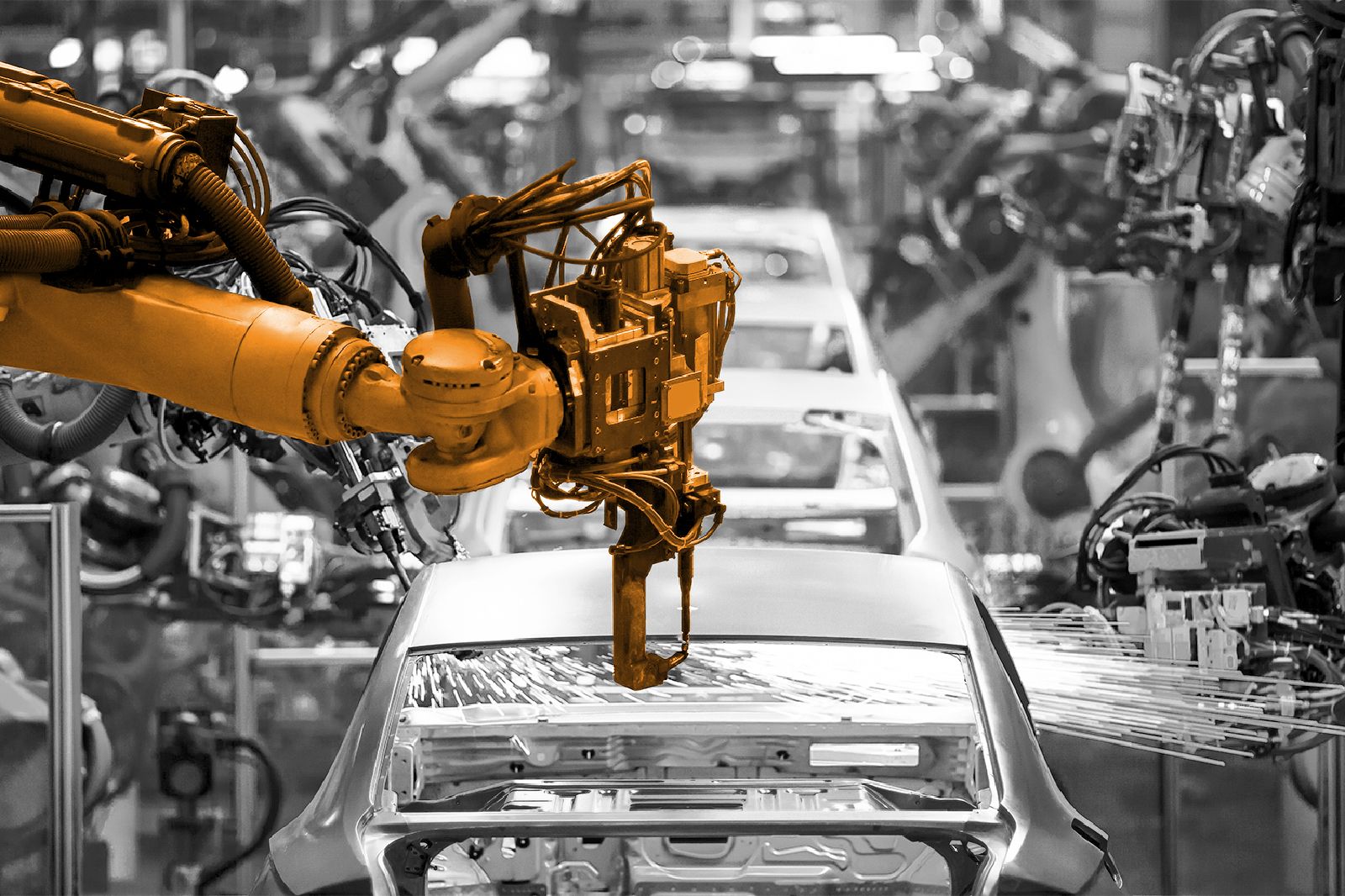
New Product Ramp Up
Project7 [P7] worked with a global holding company and a prominent Automotive Tier 1 supplier for a premium brand OEM. The organisation recently introduced a new front suspension sub-frame on a highly-automated line, which also included the introduction of brand new technologies. As such, the company committed to a ramp-up schedule with the OEM in order to meet increased demands.
Project7 were engaged in order to help them achieve their newly-raised production goals and raise productivity and efficiency on the shop floor.
Before the project, the client had struggled to keep up with the ramp-up schedule, which negatively impacted their relationship with the OEM. The OEM implemented weekly governance to drive improvement and confirmation due to the delayed production.
The production line operators, supervisors, engineers and maintenance members were inexperienced with the new product and technologies, and lacked the problem-solving ability needed to recover the complex situation. The company, in addition to not meeting the rampup commitment, was experiencing an increase in Health & Safety issues (namely an increase in accidents and decrease in reporting of near-misses), increased scrap, increased headcount (due to quality inspection and rework), and a negative EBIT impact. There were no maintenance regimes in place to support built-in Quality and Flow, and no cycle time or managed buffer controls to enable flow.
The client relationship deterioration put the future product placement within the plant at risk, and risked the withdrawal of the OEM accreditation altogether, blocking them from future business with the OEM.
The current state needed to be understood quickly in order to establish data that would provide information to support decision-making, defining priorities by highest impact and shortest lead time, agreeing actions & responsibilities and scheduling of production windows to conduct the experiments. Contrary to the incumbent mindset, the need to stop production when volume was not being achieved was a significant step in order to find and solve the problems causing the low output.
Run at Rate schedules were required to enable controlled implementation of actions, and to tangibly measure the impact of these actions against a suite of evolving performance KPIs.
Dedicated teams needed to be established from the existing structure and governed through short interval control performance dialogues. The current state needed to be visualised in order to be understood, and measured in order to be controlled.
P7 provided an interim Plant Manager, responsible for the overall plant performance, customer relationship and EBIT. The interim Plant Manager was also supported by two P7 Performance Improvement Specialists:
- Production Specialist – Experienced in NPI and Lean Principles, Systems and Tools; the Production Specialist was also responsible for the coaching of the line supervision.
- Maintenance & Engineering Specialist – Experienced in line design, installation and ramp-up, and qualified in Planned Maintenance and TPM. The Maintenance & Engineering Specialist had the technical ability to support Problem Root-cause identification and resolution. They were also responsible for coaching the line Maintenance and Engineering personnel.
The objectives were split into four key areas during the initial phases of the project:
Divide, Control & Conquer [Week 1] Aims:
- To establish a dedicated team of Production, Maintenance and Engineering personnel
- To design and implement temporary visual performance centres that are aligned to process flow
- To create KPIs to measure the current state, develop trends and identify priorities
- To commence short interval control review with the full team to drive containment actions, and countermeasures once the root-cause has been established
Create the Tension [Week 2] Aims:
- To calculate the improvement glide-path for each KPI and roll up into the overall JPH commitment to the OEM
- To encourage active customer engagement through regular Go-Look-See in order to demonstrate the actions and results, creative positive tension through the SIC review and customer presence
Run at Rate [Weeks 3 – 11] Aims:
- To schedule production stoppages to enable controlled line intervention
- To make the changes, driven by disruption analysis, and to test the containment and/or solutions and measure the impact using a SIC review and KPIs
- To repeat the cycles, increasing intervention time initially until the quality and volume increase to a sustainable level
Process Re-Engineering [Throughout Project Duration]
- Hour-to-hour controls [OEE management]
- Restructuring the Production and Maintenance
- The Line Performance Management Centre [the local team’s daily performance scrum dialogues]
- The Plant Performance Management Centre [Management & Supervision governance]
- Planned Maintenance regimes, including Line Patrol and Maintenance Satellites
- Operator Standardised work, including HSE
- Automation Yamazumi regarding motion analysis for waste in movement to support cycle time improvement
- Managed Buffer controls, to enable flow and bottleneck management
- The escalation procedure
- Digital Andon Board [stop-call-wait principle]
- Technical modifications to the line including a vision system [Error Proofing]
As a result of support from P7, the plant achieved the revised delivery commitments to the
customer and maintained the accreditation, as well as being awarded future business. The EBIT
was recovered and improved upon.
- 17% uplift on EBI
- 28% reduction in accidents
- 131% increase in JPH within 12-week period
- 61% reduction in overtime
- Shift operation reduced from 3 to 2
- 12% reduction in direct headcount cost
- 23% reduction in scrap
- 63% reduction in customer complaints
- ROI 8:1 within the 12-month project period*