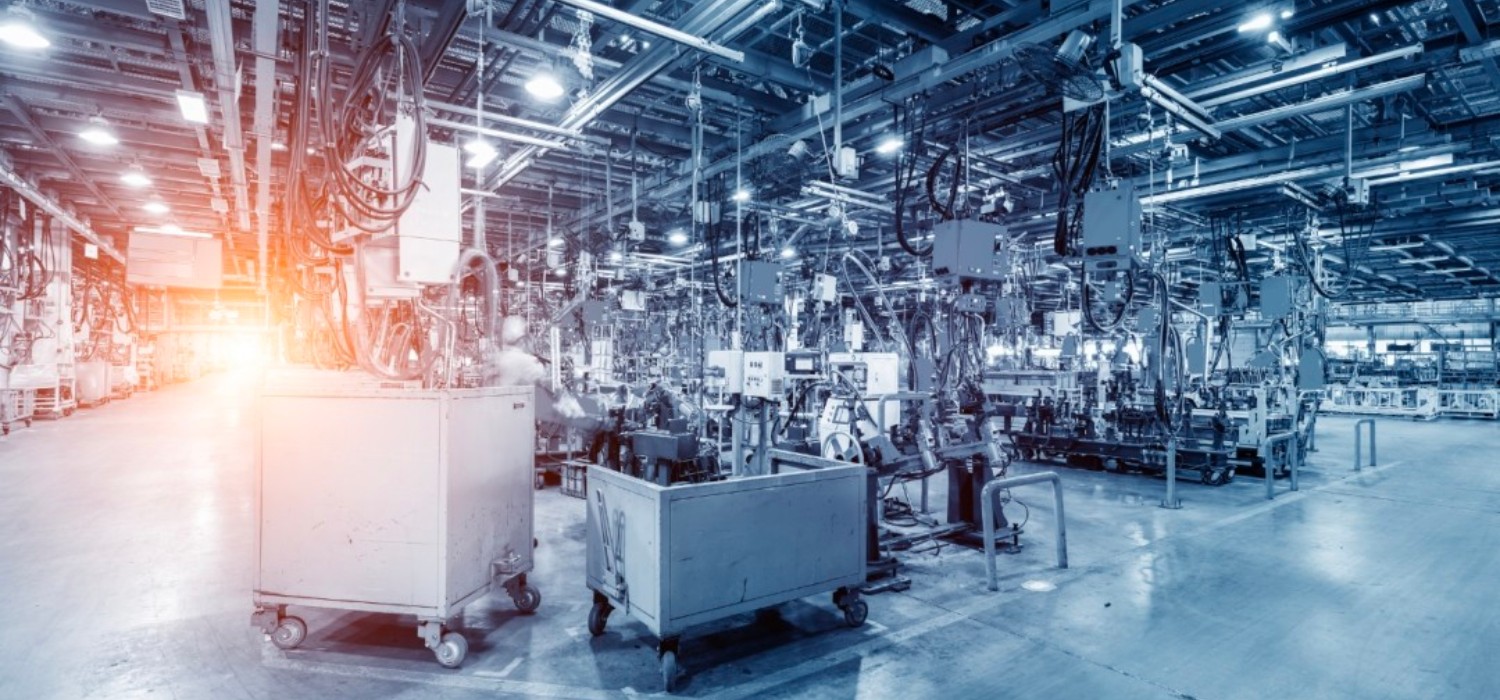
Never has there been a greater responsibility for every business to maximise its efforts to drive to net zero. Correct machine maintenance coupled with Lean processes (once just the domain of operations) is now proving to be a force multiplier across maintenance and engineering in the drive to net zero.
Irrespective of the industry, the drive to net zero can be accelerated as business drives out waste in all its forms.
This article does not have all the answers, but aims to promote a discussion to find some of those answers. The examples in this article illustrate situations that I have experienced in my role as a TPM and Lean consultant.
Lean manufacturing focuses on driving out waste in 8 areas that I list below, and I will look at how considering these areas as a Maintenance and Reliability Engineer can reduce waste and add to a facility’s intent to be carbon neutral.
1. Waiting time
When I am auditing weekly planned maintenance for compliance to schedule, I frequently see that work was not completed due to ‘waiting on parts’. It must be a tenant of work order planning and prioritization that before any job is put onto the schedule, particularly if it is on the critical path, that parts are on-site, in the storeroom or in the job box.
I can hear some of you saying that in the ‘real world’ jobs get put onto the schedule without the parts being in-house “because we know they will be here on time.” Well, unless you have an iron-clad reason to believe that they will be on hand when you need them, resist the temptation to put them on the schedule.
What happens far too often is that parts of a production line are shut down in anticipation of the work being carried out, whilst the remainder of the line is running without producing anything, and there is a last-minute scramble by maintenance to try and do a workaround. This means frustration from operations, lost productivity and wasted energy; and it is this wasted energy that detracts from the drive to net zero. Moreover, the line will have to go through the whole process a second time when the parts do arrive. The solution is maintaining a planning discipline; if the parts are not on hand, don’t put the job on the schedule.
2. Over Production
Manufacturing product just to keep a machine running with no customers for the finished product is wasteful of energy and resources, let alone a very poor business model, and yet it happens. Lean tools will help you predict customer orders and manufacture Just in Time (JIT). Tools such as level loading and understanding the Coefficient of Variance (COV) of customer orders enable you to correctly predict your customer demand and will help you reduce waste, and thus reduce your carbon footprint due to that unnecessary over production.
Over production also causes machine wear with no business value, which then requires unnecessary cost to maintenance and impact to your maintenance program. I will talk about this in more detail in the discussion on inventory.
Run your machines to add value not to add inventory and environmental carbon.
3. Re-work
Re-work, re-building, re-engineering, re-surfacing, re-wiring, in fact ‘re’ anything burns energy by extending task duration. I am surprised when I am told “I didn’t have time to do it properly,” but that the same individual did have time to do the re-job twice! A Lean process produces the highest first pass yield and ensures product gets to the customer, be that internal or external, at the rate and condition expected, right first time, every time. Short interval control and KATA coaching with Root Cause Problem Solving (RCPS) be that in manufacturing paper, or maintaining a train engine, drives out waste and so reduces the carbon footprint.
Re-work is also increased when machines are not operating at standard due to wear, misalignment, oil leaks, air leaks, loose connections, lack of lubrication, failing bearings and a host of other defects. Operations know about these issues often long before maintenance and should have a simple accessible system to be able to enter work orders into the CMMS. Keep your machines running to at least OEM condition to maximise first pass yield and takt time and drive out waste.
Even better is when a business implements Autonomous Maintenance where possible and has trained the operators on how to look after their own machines. Not only does this optimise the machines to drive out re-work and waste, but it also releases maintenance to work on the more complex jobs that will add further value to the business. Efficient machines run far more economically than inefficient machines and thus also add to the drive for net zero.
4. Movement
Having people move around a production area be that a building site, manufacturing work cell or an aircraft hangar to collect parts and materials is wasteful of effort and time. Wasting time means the lights are burning longer, the forklift trucks are wearing out faster, fuel is being used unnecessarily etc.
In maintenance, and again I see this far too often, downtime is extended when the technician takes 15 minutes to go back to the stores for one more bolt, or back to the tool room for another socket or to the oil store for another can of WD40 because the one that they have is empty. When the storeroom is a mile away and they travel by truck this is adding to their carbon footprint. Again, plan the whole job, collect everything in one go and avoid extended downtime and its associated waste.
Reducing movement with models such as robust work order planning, Kanban, and task boxes, reduces your carbon footprint.
5. Over Processing
Over processing is a sign of a poorly designed process. Poor leadership, poor instructions, unnecessary administration, poor communications, all these cause over processing. Over processing may also be the result of poor machine design, inadequate maintenance, inadequate job station tooling or facility layout. Design for Maintainability, Design for Reliability and Autonomous Maintenance are all tools that reduce over processing.
Completing hard copy work orders is another area that can be irradicated in the drive to net zero through a paperless work order system. There are now many CMMS systems that can be accessed via Pads, phones and laptops that remove the need to print WOs that will be either used once and recycled, or worse, stored in filing cabinets never to be seen again. Integrating the work order system with electronic PMs or video not only removes paper but allows the new generations of technicians to interface with tech in a way that is completely intuitive to them and removes a source of waste.
6. Too Much Inventory
The 14 billion square feet of warehousing across the USA generated 380 million tons of carbon dioxide in 2017 alone (Ries et al., 2016).
Too many companies still manage huge warehouses of product, that they then call ‘Work in Progress’ WIP, whilst that product has no immediate customers. In one plant the leadership solution to overspill of ‘WIP’ was to rent more warehouse space, increasing the carbon footprint even further, rather than solving the problem. Adding more space is not the solution, true Just In Time (JIT) manufacturing is the solution. Solve the problem, not the symptom.
I also find that heavy industry is sometimes guilty of storing old machinery and old equipment for years and years “just in case,” and I know that many have stories of when “the bone yard saved our bacon”, but this is often just because of poor planning, and old bone yard poorly maintained parts will need to be replaced causing more waste. In one plant, getting rid of scrap that was taking up warehouse space returned $50K to the maintenance budget, far better use of the resource than ‘just in case’. Store what you need and only what you need and reduce your carbon footprint.
7. Not Using Your People’s Intellect
Your people are your best soldiers in the fight to achieve net zero. By giving them a culture where they can contribute to continuous improvement such as Preventative Maintenance Optimization, Work-Place Organization, and Kaizen Tieon, and through nurturing corporate citizenship and building High-Performance Teams, people become the powerhouse of change to reduce waste in all areas and driving the reduction to net zero.
One team had been changing out electrical parts that had a three year ‘life’ and throwing them into the scrap and had been for years. A new team member asked, “Have we ever carried out an experiment to see how long they really last”? It transpired that the business had never had a failure in 15 years and after changing from a 3 yearly changeout to an agreed ‘run to failure policy’, with components now in place for 5 years they still hadn’t had a failure. Using your team’s intellect can save waste and when they then share what they have learnt with others (in Lean this is part of Yokoten), they also encourage others in the drive to net zero.
8. Transportation
Transportation is often seen as the bad boy of carbon and the drive to take dirty fuel of the streets is now getting some traction with electric vehicles. However large fuel-hungry vehicles will still be needed for some time, but their considered use can reduce carbon footprint. Far too often, for example in work we have done in the paper industry, we see half empty trucks leaving the depot. Better planning with level loading, workplace organization and integrated IT processes can ensure trucks are carrying out fewer journeys, are more often completely full or travel shorter distances before they fill up will also reduce cost and carbon. I have also seen how VSM to understand how orders are processed and how and when loads are planned has considerably reduced cost and carbon. As a by-product, the search for an ever-reducing pool of qualified drivers becomes that bit easier so when full loads are ready to go, there is also a driver available to move that load.
In one plant they routinely flew parts on commercial aircraft to service machines that were down because they had not done a critical parts analysis to hold essential spares at min/max in their own storeroom. A $100 part on a first class seat burning airmiles is no substitute for professional asset management and planning.
So, we can see that at every turn Total Productive Maintenance and Lean Continuous Improvement processes, drive out waste.
Optimising these methodologies ensures your people and processes are ready to drive out waste, save money and improve productivity; every effort helps in the drive to carbon zero.
Experience shows that it’s the small changes that you sustain that make the long term impacts, so what change can you make in your maintenance operation today as your contribution to drive to net zero? If you would like to add to this discussion join me on the Maintenance World Linkedin page to continue the discussion.
References
Ries, J., et al, 2016. Environmental Impact of Warehousing: A Scenario Analysis for the United States. International Journal of Production Research.