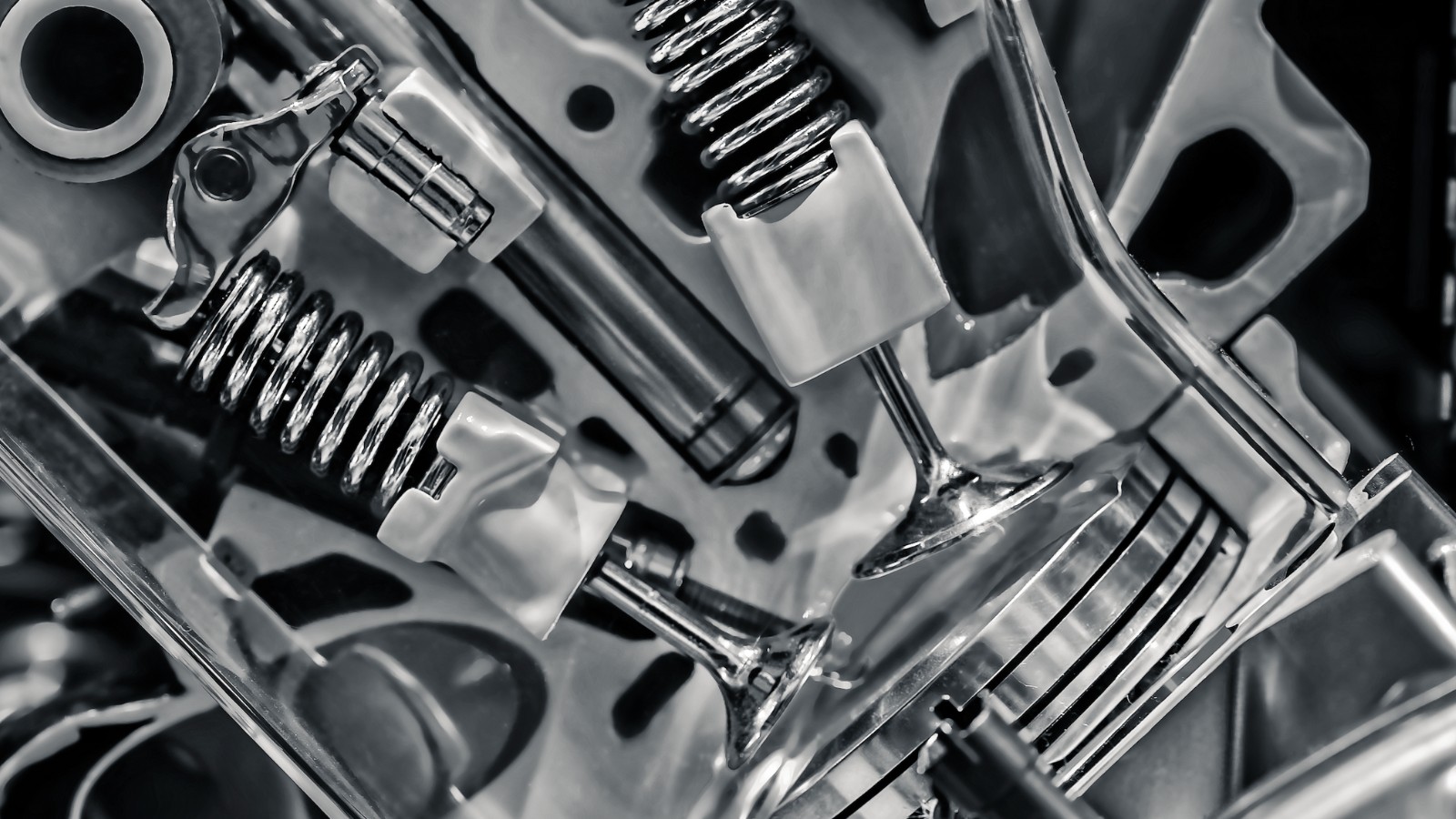
Over the years, we have had the privilege of working with some of the world’s most respected organisations to drive significant performance improvements. One such project was our Lean Plant Leadership Programme (LP2) with a leading engine valve manufacturer in the automotive industry. This reflection explores the challenges faced, the solutions implemented, and the impactful results achieved through our collaboration.
Our client is a major manufacturer in the automotive industry, supplying engine valves to most car manufacturers globally. In recent years, the company faced increasing competition from low-cost manufacturers, coupled with rising scrap rates and high levels of finished product. This competitive pressure necessitated a reevaluation of their processes to boost performance and sustain long-term success.
The company engaged Project7 to help coach and integrate a Lean Leadership Programme to enhance productivity and equipment reliability.
Our approach was designed to create a leaner structure, mentality, and culture within the organisation, ultimately leading to improved performance and a more resilient company culture.
The primary challenge was the need for a clearly defined, standardised operating system across their plants. This inconsistency led to varied processes, systems, product quality, and delivery outputs, negatively impacting customer confidence. The company urgently needed access to lean tools and principles to establish a standard foundation for operational excellence across its engine components division.
Specifically, the intervention required:
- Creation of a standard foundation for operational excellence.
- Integration of effective engineering maintenance processes to improve asset management and equipment availability.
- Identification of the right processes and the right people to achieve sustainable performance output.
These objectives were to be achieved through a Back to Basics approach, focusing on core manufacturing business elements.
After a thorough assessment, Project7, along with our client, decided to create and deploy the Lean Plant Leadership Programme (LP2). This solution aimed to design, implement, and evaluate a world-class operating system that would be standardised and applied across 14 manufacturing sites globally.
The programme encompassed seven steps of the P7 Way:
- Strategy into Action (Policy Deployment)
- Tiered Visual Performance Management (TVPM)
- Short Interval Control & Performance Dialogues
- Process Confirmation & Go Look See
- Setting Clear & Aligned Targets; Problem-solving Level 1
- Coaching for Success; Problem-solving Level 2
- Talent Management and Leadership Development
These steps were adapted and implemented to create an Engine Components Operating System. Project7 worked closely with the executive team to define their needs clearly and focus on developing the organisation through lean techniques and best practices.
Within each site, a master schedule was created with local leadership teams to drive measurable activities against performance targets. Clear directional targets were established, and processes were created to guide the improvements.
Implementing LP2 led to significant improvements in business performance across all operations. Each site underwent a four-month implementation period based on our 3P approach, yielding impressive results:
- 31% Improvement in Overall Equipment Effectiveness
- 33% Improvement in Equipment Cycle Time (Bottleneck)
- 67% Reduction in Premium Freight
- 21% Reduction in Change Overtime, Hit to Hit
- 4% Reduction in Scrap
- 7% Reduction in Temporary Resource
- 11% Reduction in Overtime
- 21% Reduction in Finished Goods Inventory
- $24 Million Cost Avoidance in Capital Investment
The programme’s success extended beyond these metrics, creating a high-performing team culture and standardising operations across all 14 plants. Introducing tiered visual performance management, short interval control, and robust governance structures ensured sustained improvements and continuous knowledge transfer.
Lessons Learned and Future Outlook
Reflecting on this project, several key lessons emerge:
- Standardisation is Key: Establishing a standardised operating system across multiple sites is critical for consistent performance and quality.
- Lean Leadership: Integrating lean principles and leadership development fosters a culture of continuous improvement and accountability.
- Collaborative Approach: Close collaboration with the client’s executive team ensures the solutions are tailored to their specific needs and objectives.
- Sustainable Change: Focusing on both process improvements and cultural shifts ensures that the changes are sustainable in the long term.
The Lean Plant Leadership Programme demonstrated the profound impact that structured, strategic interventions can have on an organisation’s performance. By creating a leaner, more resilient structure and culture, our client not only enhanced its operational efficiency but also strengthened its competitive position in the market.
At Project7 Consultancy, we remain committed to helping organisations achieve their strategic goals through targeted performance improvements.
Please get in touch with us for more information on how Project7 Consultancy can help your organisation achieve similar results.