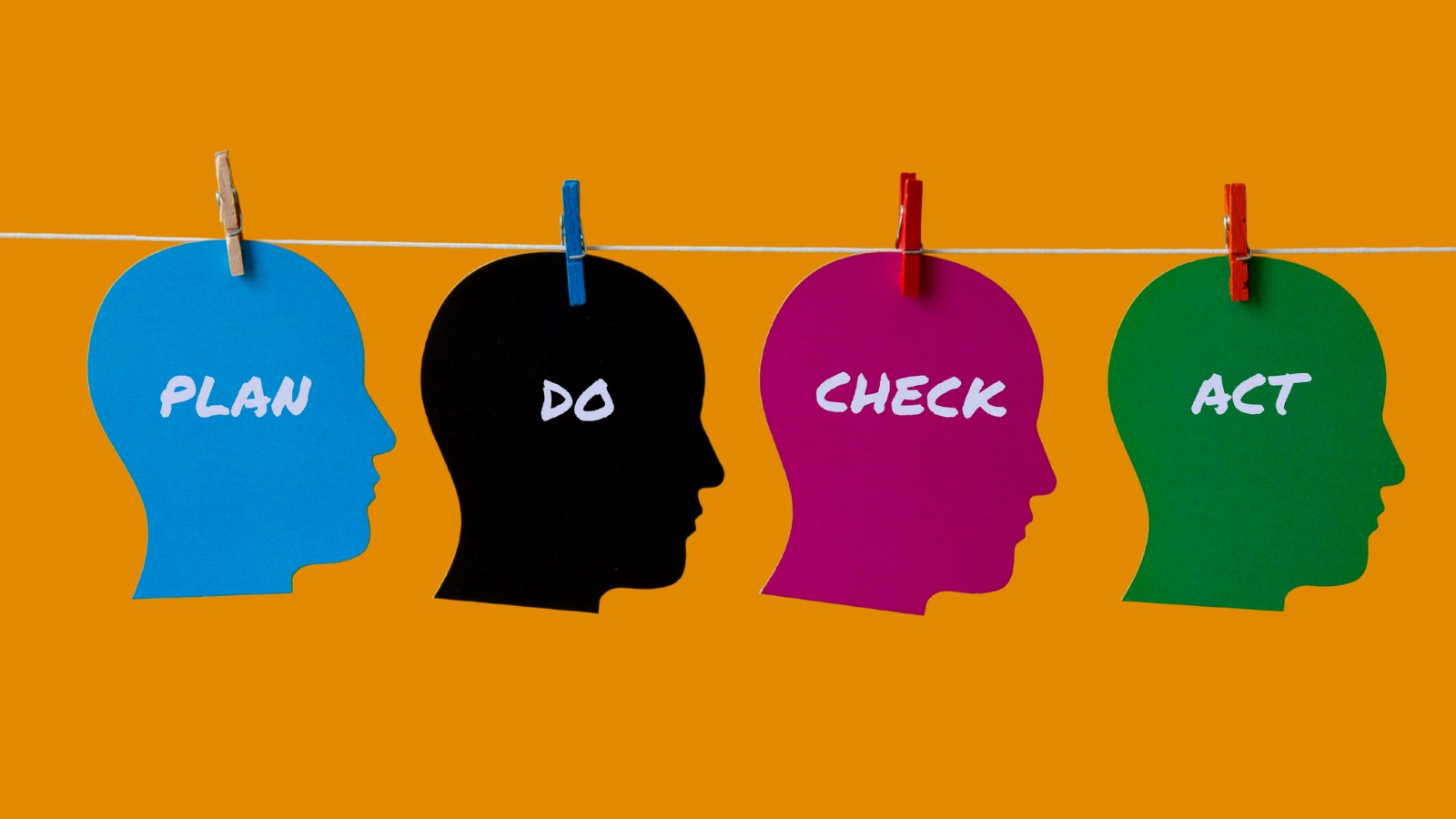
When speaking with leaders outside the manufacturing industry, one of the most common questions we encounter is: “How can Lean principles be effectively and sustainably integrated into service-based industries, where processes and outcomes are often more variable and less tangible than Lean’s origins in manufacturing?”
This question is challenging because Lean manufacturing principles, initially developed for the automotive industry and other manufacturing settings, rely heavily on the standardisation of processes, reduction of waste, and continuous improvement.
These principles are straightforward to apply in environments with repetitive, predictable processes and tangible outputs.
However, the variability, customer interaction, and intangible outputs typical of service industries (such as healthcare, finance, and hospitality) present unique challenges in adapting Lean methodologies.
Exploring how to customise and implement Lean principles in such environments while maintaining their effectiveness and sustainability is a critical area of ongoing research and practice. However, don’t let this deter you. We have seen Lean successfully applied in diverse areas, from running the London Underground, transporting human organs across the USA, organising care homes, optimising call centres, and reducing the time for end-of-month closing in a large corporate finance department.
We believe that Lean, when intelligently applied, will reduce waste in any process, develop a culture of continuous improvement, and delight both the customer and the shareholder or business owner.
Implementation Strategies
To address the challenge of integrating Lean principles into service-based industries effectively and sustainably, several strategies can be pursued:
- Customisation of Lean Tools and Techniques
Adaptation of Tools: Modify traditional Lean tools such as Value Stream Mapping (VSM), 5S, and Kaizen to fit service processes. For example, in healthcare, VSM can map patient flow through different departments, or in finance streamline supplier payments, or in hospitality speed up room cleaning and standardise hotel bedroom layouts. Don’t just replicate what manufacturing plants have done; adapt the core principles to be meaningful in your business.
Service-Specific Metrics: Develop metrics that capture service quality and customer satisfaction alongside efficiency and waste reduction. The key is to make the process and the metrics meaningful in driving your business.
2. Training and Education
Lean Education: Provide Lean training tailored to your employees so they understand not only the tools of Lean implementation but also why they are useful in driving your particular business. This way, they will see how the principles can solve their problems and improve their daily operations. In designing this training, engage with those who will own the new process to ensure you are solving real problems.
Cross-Industry Learning: Encourage learning from sectors where Lean has been successfully applied, such as Lean healthcare, to adapt best practices to your particular industry or need.
3. Cultural Change and Leadership
Leadership Commitment: Ensure strong leadership support for Lean initiatives. Leaders should champion Lean principles, become catalysts for change, and demonstrate commitment through actions. Without this commitment, sustaining a Lean programme in any industry is impossible. Find leaders at all levels who are passionate about Lean change as they will need this passion to drive change and transform cultures on what can be a difficult journey.
Employee Involvement: Foster a culture of continuous improvement where employees at all levels are rewarded and encouraged to identify inefficiencies and suggest improvements.
4. Pilot Projects and Iterative Improvement
Small-Scale Pilots: Start with pilot projects to test Lean principles in specific service areas. Use the lessons learned to refine and expand Lean initiatives.
Iterative Approach: Apply Lean iteratively, continuously assessing and refining processes based on feedback and performance data. Practice PDCA (Plan-Do-Check-Act) to constantly reflect on and refine your processes.
5. Customer-Centric Focus
Customer Feedback: Regularly gather and integrate customer feedback into your continuous improvement processes to ensure Lean improvements align with customer needs.
Customer Journey Mapping: Use customer journey mapping to identify pain points and opportunities for Lean improvements from the customer’s perspective. Too many organisations keep the customer ‘on the other side of the wall.’ This is an outdated behaviour based on protectionism and fear. Be transparent and ethical, which Industry 5.0 customers now rightly demand.
6. Technology and Automation
Digital Tools: Leverage digital tools and automation to streamline service processes and reduce variability.
Data Analytics: Use data analytics to gain insights into service performance and identify opportunities for Industry 4.0 integration to optimise areas for Lean improvements.
7. Collaboration and Knowledge Sharing
Industry Collaboration: Encourage collaboration between different service sectors and internal departments to share Lean success stories and challenges. Bring in people from other industries who have successfully engaged with Lean principles so that you do not have to ‘reinvent the wheel.’
Lean Communities: Participate in Lean communities and forums to exchange knowledge and experiences. Attend online and in-person Lean events from other industries to learn from them and adapt their experience to your needs.
If you require support to begin your Lean optimisation journey in the service industry, we invite you to get in touch. We offer a no-cost discussion to explore your opportunities and demonstrate how Project7 can assist in driving Lean implementation for your business.