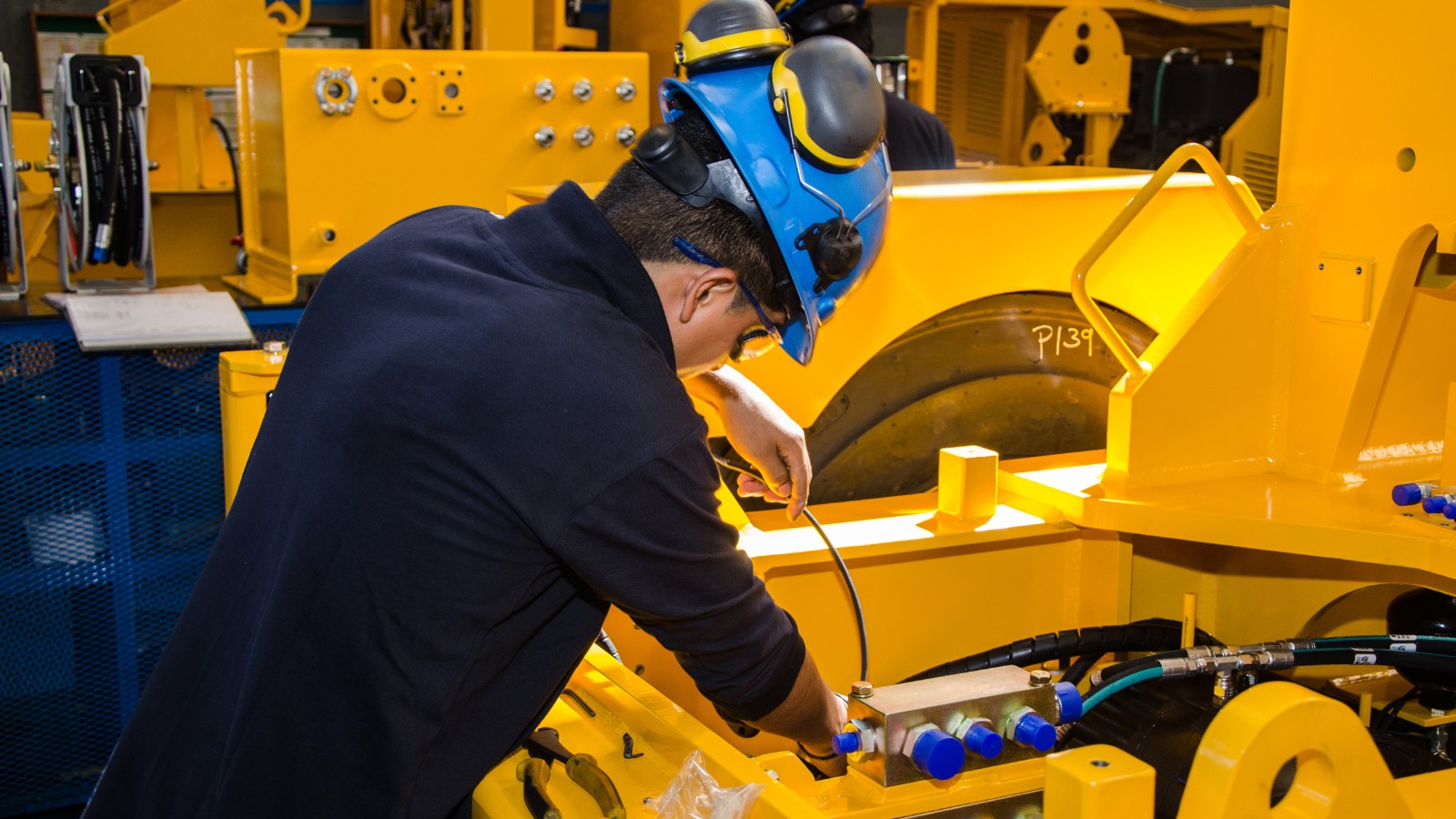
Process confirmation is a vital element in Lean manufacturing. It ensures that standardised processes are followed consistently and that they deliver the intended results. By systematically verifying adherence to these processes, deviations can be identified and corrected promptly. However, in practice, process confirmation is often overlooked, leading to diminished production quality and efficiency.
This article explores the significance of process confirmation, the challenges that prevent its consistent application, and the consequences of neglecting this essential practice in manufacturing.
What is Process Confirmation?
Process confirmation is the practice of checking that operations are performed according to agreed procedures and standards. Its primary goals are to maintain process integrity, ensure product quality, and support continuous improvement. When done correctly, it prevents errors from going unnoticed and ensures that processes remain optimised over time.
Examples of Process Confirmation
1. Assembly Line Inspections
- Example: In a paper manufacturing facility, supervisors must check that tasks like installing motors, pumps, and couplings are done according to the Standard Operating Procedures (SOPs).
- Confirmation Activities: Inspect torque settings on bolts, confirm torque wrenches are calibrated, and ensure correct-grade bolts are used.
- Impact: In one instance, using uncalibrated tools and lower-grade bolts led to sheared bolts, causing $50K in losses from a single incident.
2. Quality Control Audits
- Example: In food processing, quality control inspectors monitor hygiene standards during food packaging.
- Confirmation Activities: Check that employees wear gloves and hairnets and follow documented cleaning procedures.
- Impact: A failure to ensure proper footwear changes at one plant led to hygiene breaches, risking product contamination.
3. Routine Maintenance Checks
- Example: In a tea bag paper production plant, routine maintenance should confirm that machinery is lubricated with the correct materials and on schedule.
- Confirmation Activities: Verify that food-grade grease is used in food-contact machinery.
- Impact: In one case, non-food-grade grease caused contamination, leading to production downtime and reputational damage.
Why is Process Confirmation Often Overlooked?
Despite its importance, process confirmation is frequently neglected. Here are some common reasons:
1. Time Constraints
- Reason: “We’re too busy.” The pressure to meet production targets often takes precedence over process verification.
- Consequence: Hidden wear or minor deviations go unchecked, leading to costly breakdowns and longer downtimes later.
2. Lack of Awareness or Training
- Reason: Employees and supervisors may not fully understand the importance of process confirmation or how to perform it effectively.
- Consequence: Without proper training, checks become superficial, and deviations remain unnoticed until they escalate.
3. Overconfidence in Established Processes
- Reason: A belief that once a process is optimised, it will function correctly without further checks.
- Consequence: Process drift occurs, errors accumulate, and standards erode over time.
4. Resource Limitations
- Reason: Insufficient personnel or budget prioritises visible tasks over routine confirmations.
- Consequence: Critical issues like improper lubrication are missed, leading to production delays and higher costs.
5. Cultural Factors
- Reason: A lack of emphasis on continuous improvement and accountability creates an environment where process confirmation is undervalued.
- Consequence: Leadership focuses solely on output, ignoring the long-term benefits of consistent process verification.
Consequences of Neglecting Process Confirmation
Failing to implement process confirmation thoroughly can have severe repercussions:
1. Quality Issues
- Impact: Products fail to meet standards, increasing rework, waste, and customer complaints.
- Example: A packaging line error led to defective products reaching customers, damaging the company’s reputation.
2. Increased Costs
- Impact: Inefficiencies and undetected issues drive up costs.
- Example: Failure to address minor defects in a printing plant escalated into costly repairs when problems were discovered late in production.
3. Safety Risks
- Impact: Ignoring safety protocols increases the likelihood of accidents and injuries, leading to legal and medical expenses.
- Example: Skipping safety checks in a chemical cleaning plant resulted in injuries and regulatory fines.
4. Reduced Process Efficiency
- Impact: Processes lose efficiency over time due to undetected deviations.
- Example: Worn components led to extended machine setup times, undermining productivity gains achieved through SMED practices.
5. Loss of Continuous Improvement
- Impact: Without regular checks, continuous improvement initiatives stagnate, eroding leadership credibility and employee engagement.
- Example: In a welding company, failure to verify robotic setups resulted in recurring defects and a rework line that undermined Lean manufacturing goals.
The Importance of a Culture of Process Confirmation
Process confirmation is more than a technical exercise; it requires a cultural commitment to accountability, improvement, and quality. Leaders must prioritise process confirmation, recognising its long-term value for operational stability and growth.
Key actions include:
- Training Employees: Provide thorough training on process confirmation techniques and their importance.
- Empowering Teams: Engage employees at all levels in identifying and correcting deviations.
- Leadership Commitment: Ensure leaders model and support process confirmation as a non-negotiable practice.
- Regular Audits: Conduct routine process checks to identify trends and prevent drift.
Wrapping Up
Process confirmation is a cornerstone of Lean manufacturing, ensuring that processes operate as designed and deliver consistent results. When overlooked, it leads to quality issues, higher costs, safety risks, inefficiencies, and a stagnation of continuous improvement efforts.
By embedding process confirmation into daily operations and fostering a culture of accountability and improvement, businesses can sustain the benefits of Lean practices and achieve long-term success. Ignoring it is simply too costly—both financially and operationally.