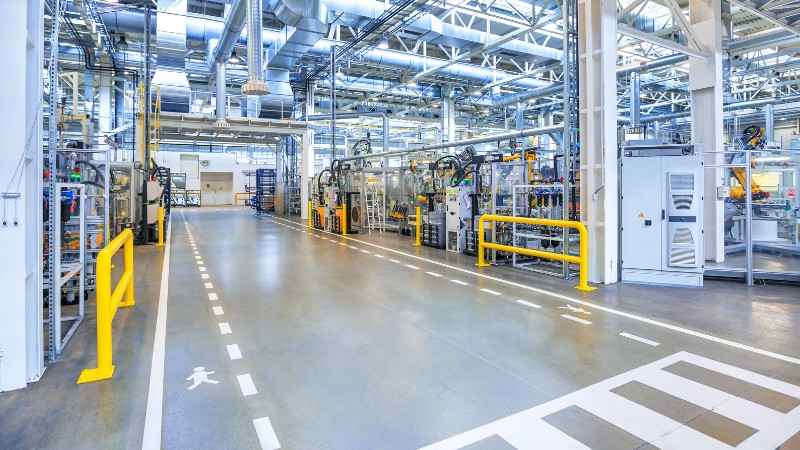
5S is a well-known and widely implemented methodology. Its steps—Sort, Set in Order, Shine, Standardise, Sustain—are fundamental to creating an organised and efficient workplace. However, for anyone who feels they have mastered 5S, there are always new layers of value and insight to uncover. This article explores how 5S can be continually leveraged to drive innovation, efficiency, and cultural transformation.
The Deeper Value of 5S
Lean tools, including 5S, have often been the subject of gimmicks or complex graphics to try and make a supposed original point. Many of you, we are sure, will have seen new constructs around 8S, 11S, or even 14S. However, the essence of 5S has proven sufficient for around 50 years to transform from the simplest to the most complex work environments, both inside and outside of manufacturing. This is why we argue that if you learn why the 5 S’s are important and execute them correctly, then nothing else is needed.
Simplicity
The original 5S methodology (Sort, Set in Order, Shine, Standardise, Sustain) is simple and easy to understand. It provides a clear framework for organising workspaces, eliminating waste, and improving efficiency without adding unnecessary complexity. The key to this simplicity is to let all the individuals who work in the area be engaged in the change and particularly understand why the change is needed. In this way, they become their own experts, understanding the process and the need without becoming overcomplicated. As a result of this engagement, they are also far more likely to sustain the change. We often see ‘experts’ parachuted in to run a 5S exercise only to see the area back to its chaotic state, sometimes within hours, as those who will need to own the solution were not integral to building the newly organised 5S area. 5S doesn’t need experts; it needs engagement.
Comprehensive Coverage
The 5S methodology covers a broad range of areas essential for workplace organisation and efficiency. It addresses the key aspects of sorting out unnecessary items, organising necessary items, cleaning, and maintaining workspaces, establishing standardised procedures, and sustaining improvements over time. Don’t get fixated on making things pretty; make them functional, be that in organising a production line or even at home.
In one paper converting plant, a very large spanner was used under a ream cutter. It was the only place that spanner was ever used. In the 5S exercise, the operator said:
I suppose that this spanner will now have to go in the tool store or on a shadow board.”
The operator had always kept the spanner under the machine ‘at the point of use’ where he needed it. As it wasn’t a trip or other hazard, we enabled him to put a shadow right at the place he needed it. He had his tool to hand at the right and most efficient place, and as a bonus, became an advocate for 5S methodology. 5S is about workplace optimisation, not beautification.
Adaptability
The 5S methodology has proven to be highly adaptable and has been applied to various types of commerce and industry, including manufacturing, office settings, healthcare facilities, and even virtual workspaces. You can even 5S your computer desktop! Just using 5 ‘S’s has proven in all these environments to be adaptable, allowing organisations to customise and scale the approach to suit their specific needs and circumstances. So why add unnecessary steps that over-complicate what already works?
Focus on Fundamentals
By focusing on the fundamental 5 steps of workplace organisation and standardisation, the 5S methodology helps build a solid foundation for continuous improvement initiatives. Just 5 ‘S’s used properly will instil discipline, orderliness, and a culture of cleanliness and efficiency within any organisation.
Low Cost and High Impact
Implementing the 5 ‘S’s typically requires minimal financial investment, as it primarily involves changes in behaviour, processes, and workplace layout rather than complex nugatory steps, costly equipment, or new technology. Yet, these simple steps consistently yield significant benefits across businesses in terms of productivity, quality, safety, and employee morale when leadership and teams commit.
Gateway to Further Improvement
While some organisations have chosen to expand beyond the original 5S framework, starting with the proven basics provides a stepping stone for more advanced Lean practices. Once the 5S principles are firmly established and sustained, learning organisations may choose to explore additional Lean tools and techniques to further enhance performance. However, these do not need to include overcomplicating 5S, which has already been proven to work. Expand from 5S into Leader Standard Work, Short Interval Control, Process Confirmation, Visual Management, etc., rather than trying to fix what is not broken.
Focus on Continuous Improvement
The essence of the 5S methodology lies in its emphasis on continuous improvement. By regularly reviewing and refining workplace practices, organisations can continually strive for higher levels of efficiency, quality, and safety without adding more “S’s” to the framework. Continually refine the workplace solution using PDCA, and reinforce what is known to work without adding extra complexity to 5S, which also adds risk.
Summing Up
While some organisations may find value in expanding the 5S methodology to include additional “S’s,” we don’t see the value. With our many years’ of proven experience, we put considerable weight behind the argument that just the original 5 S’s are sufficient, complemented by this methodology’s simplicity, comprehensive nature, adaptability, cost-effectiveness, and focus on continuous improvement.
Implementing the 5S methodology completely and proactively will provide a solid foundation for Lean transformation and drive meaningful improvements in organisational performance. In short, ‘we can put our house in order’ without messing with what already works; keep it simple, commit, sustain, and quickly move on to the next step in your continuous improvement journey.
For more information on how Project7 Consultancy can help you with your Operational Excellence, please contact us.