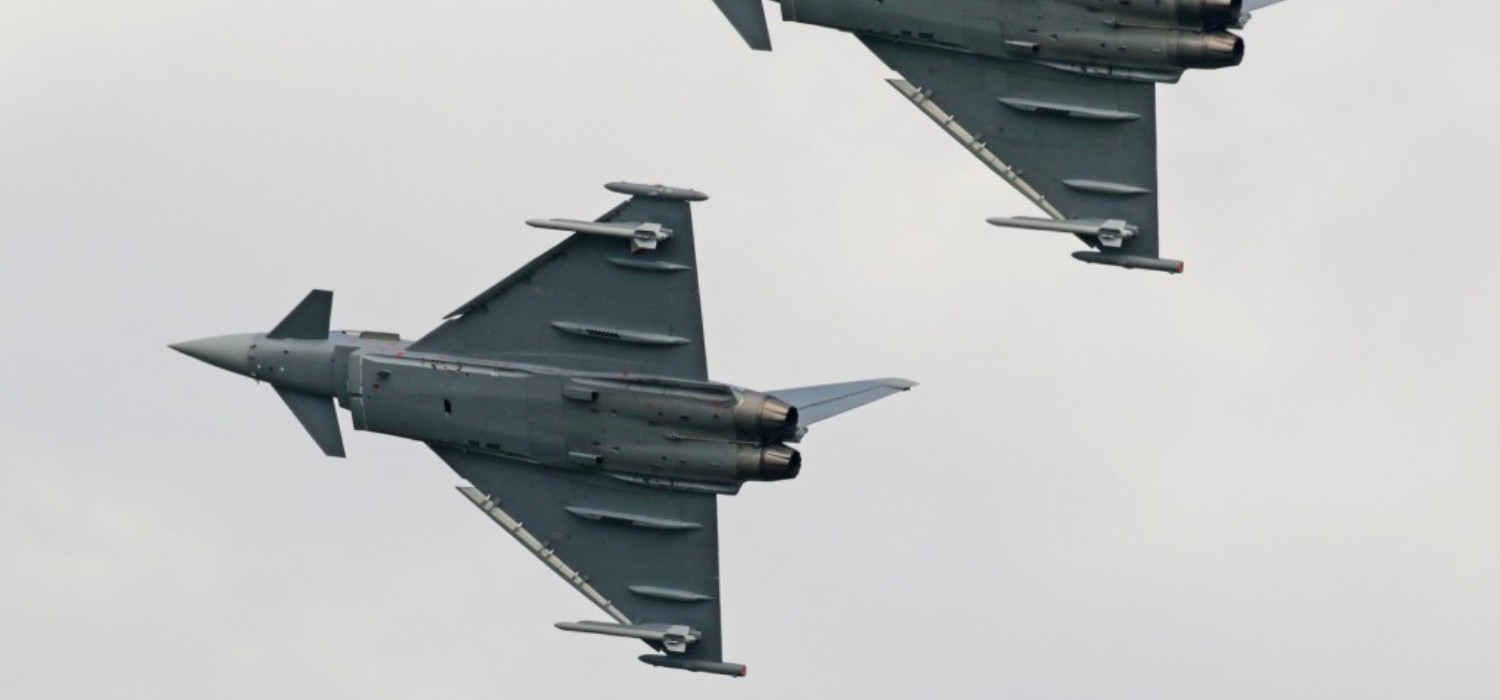
Personal Reflection – An Introduction
My career spanning nearly four decades in Total Productive Maintenance (TPM) still amazes me with the quick progression and significant gains achieved by moving through the 8 stages of TPM.
My initial 30 years as an aircraft maintenance engineer were with the Royal Air Force, where I worked on a variety of aircrafts from the 1950s models like the Hunter, Canberra, and Vulcan, to 1960s and 70s models such as the Buccaneer and Harrier, and finally, to the Tornados of the 1970s and 80s. This journey continued with our most advanced platforms of the time, including the C130J Hercules and the Eurofighter Typhoon from the 2000s.
These aircrafts represented more than half a century of aerospace technology and operational brilliance.
Mission Centric
Despite the vast differences in technology, mission, and reach of these aircrafts, a common thread was their readiness to take-off on schedule, whether for troop movements to Northern Ireland, bombing missions to the Falklands, airlifts from Cyprus, combat missions over Baghdad, or delivering emergency aid worldwide. This readiness stemmed from the exceptional team and optimised processes, ensuring aircraft reliability and mission availability.
Business Centric
My education in TPM, although not explicitly called that then, was shaped by this unique excellence and extraordinary individuals. Transitioning to continuous process manufacturing in the civilian sector in the US, I maintained the same approach to ensure maximum availability, speed, and quality of our plant and machinery. My military mission focus transformed into the three business elements described in Overall Equipment Efficiency (OEE): availability, quality, and speed.
The Air Force’s mature TPM process, based on history and generous funding, didn’t prevent me from transferring this focus to my civilian career, generating transformative results for my employers and clients.
TPM Result Illustrations
One example of implementing TPM was during an autonomous maintenance event on a rotary cutter in a book cover manufacturing plant. The event led to an 8% OEE improvement and a 6% waste reduction. In another instance, an autonomous maintenance event and value stream analysis on a tube and core machine boosted OEE by 14%. In a paper manufacturing mill, we managed a 15% increase in production speed by adopting the same methods used for aircraft servicing, including a detailed planning and scheduling system. Through work order planning and robust RCPS and 6 Sigma problem-solving, we achieved an extra production day per month at a second paper mill.
The key to these achievements was a dual focus on developing people and optimising processes. The team needed to feel valued, respected, and integral to problem-solving, while the processes had to be owned and optimised by those performing them daily.
People and Processes as Force Amplifiers
Empowering people and processes turned each team member from a perceived “victim of change” into a driver of change. This mindset, which we constantly sought to expand in the military, should be the norm in civilian organisations that truly aim to drive TPM and other changes from the ground up.
These concepts need to transition from mere catchphrases to reality for businesses to truly achieve excellence.
This excellence directly relates to TPM. My civilian career has shown me that TPM is still a journey, with tools needing adjustments to meet client needs. This journey could last from 6 months for a mature client to 18 months or more for a client transitioning from no TPM through Failure Modes and Effects Criticality Analysis (FMECA), Preventative Maintenance Optimization (PMO), Predictive Maintenance (PdM) to the integration of a Computerised Maintenance Management System (CMMS) to drive ongoing reliability through a Failure Reporting and Corrective Actions System (FRACAS). The evolution of these tools always coincides with the growth and development of leaders and teams who are genuinely involved and passionate.
Emphasis on the TPM Journey
Adding my 14 years of civilian maintenance engineering experience to my military background has taught me that any business can profit from the journey towards TPM excellence. Even if they integrate just one element of TPM at a time, the key is to focus on maintaining the change, adhering to the equation:
People + Processes = Performance
In civilian maintenance, as in military aviation maintenance philosophy, TPM can empower any business to “Rise Above the Rest” as the RAF would say. Committing to the TPM journey requires courage, but in every case I’ve observed, the evolution of TPM from one pillar to the next has made a significant impact on businesses.