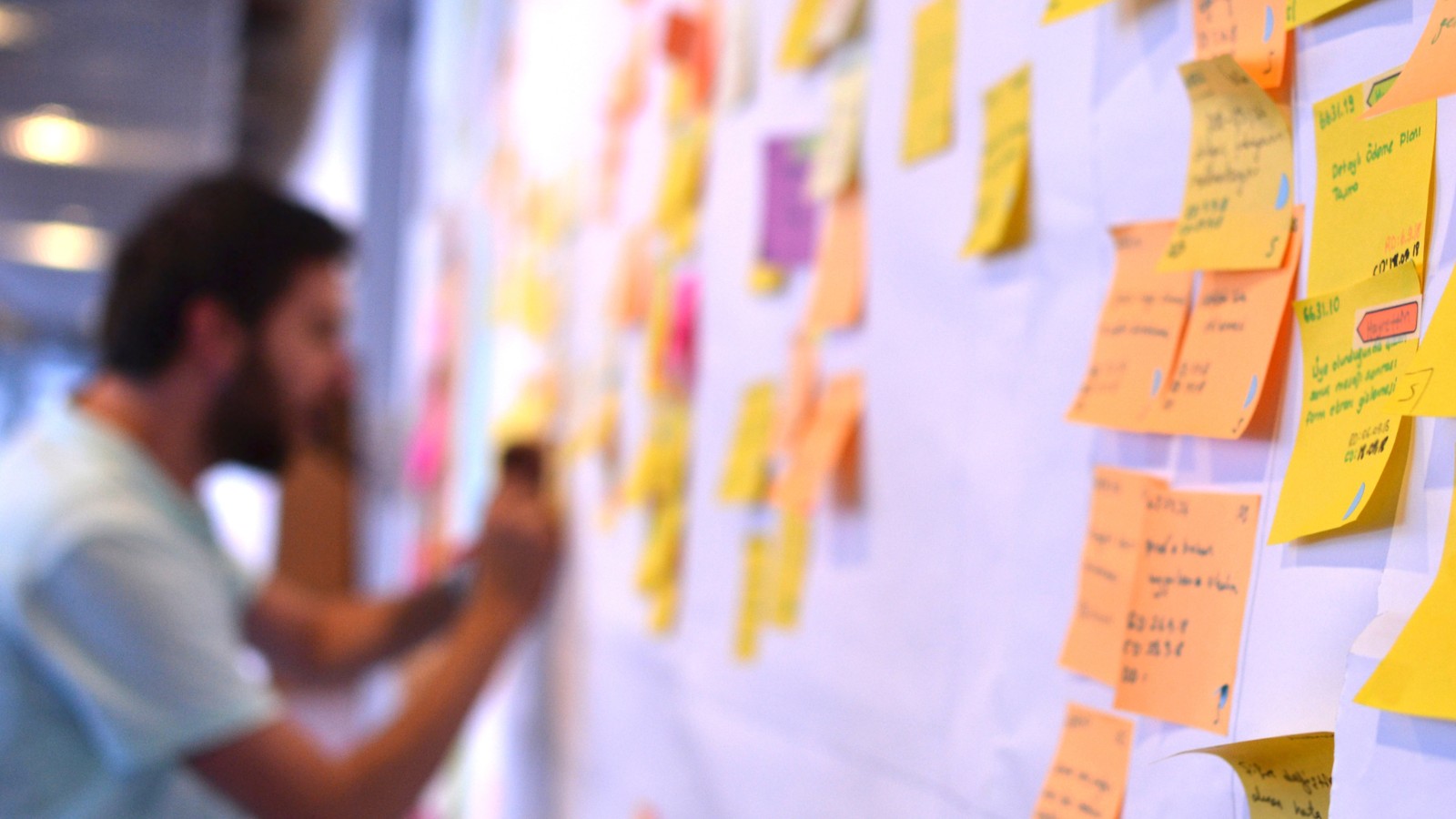
Problem Solvers and Decision Makers as Drivers of Lean Culture
It is well established that Lean cultures can only be successful when all team members become problem solvers and decision-makers. However, the reality of creating such high-performance teams and individuals is consistently underestimated. So, what does it take to transform a group of individuals into a cohesive team of decision-makers and problem solvers? Building on 30 years of military leadership experience and 15 years of industrial leadership and consulting experience, we will highlight some of the characteristics critical to nurturing groups of individuals to become high-performance problem solvers and decision-makers.
Critical Characteristics
Establish Clear Goals and Objectives
When team members understand and commit to the same objectives and goals, they align their efforts and make decisions that support these objectives and goals. Goal alignment seemed easier in the military than in civilian practice. Even when the business ‘mission and vision’ is proudly exhibited on a poster in reception, civilian processes can be stymied by self-interest, hidden agendas, and poor decisions based on short-termism. Successful implementations of Lean by companies such as Toyota, Airbus, Rolls Royce, and Procter & Gamble operate at a maturity level more akin to the military. They cut through local politics, rise above the average, and have decision-makers operating from the bottom up when it comes to problem-solving, decision-making, and ownership.
Effective Communication
Open and transparent communication is critical. Team members need to share information, listen actively, and provide constructive feedback. Here, the Lean tools of Genba, Visual Management, RCPS, and process confirmation promote communication. These tools, essentially leadership practices in the military, foster mutual understanding and help in making informed decisions as leaders and teams follow the most current information to make the best decisions.
Defined Roles and Responsibilities
Clarifying each team member’s role and responsibilities helps prevent overlap and confusion. When individuals know their specific contributions to the team’s goals, they can focus on their tasks and make decisions pertinent to their areas of responsibility. This should include practised SOPs, one-point lessons, SMED schedules, and detailed TPM work orders.
Trust and Mutual Respect
Trust among team members is the foundation of effective teamwork. When individuals trust and respect each other, they are more likely to share ideas, take risks, and support one another’s decisions. That trust is built on competence and character and is the foundation of authentic leadership, respect, humility, psychological safety, and emotional intelligence.
Psychological Safety
Psychological safety plays a critical role in team decision-making by fostering an environment where members feel comfortable expressing their thoughts, ideas, and concerns without fear of ridicule or retribution. This openness encourages diverse viewpoints and constructive dialogue, leading to more thorough and innovative problem-solving. When team members trust that their contributions are valued and respected, they are more likely to engage actively, take risks, and collaborate effectively, ultimately enhancing the quality and effectiveness of decisions made by the team.
Emotional Intelligence
Emotional Intelligence (EI) significantly enhances team decision-making by enabling members to navigate interpersonal dynamics with empathy, self-awareness, and effective communication. High EI allows team members to understand and manage their own emotions and recognise and influence the emotions of others, leading to improved collaboration and conflict resolution. By fostering a supportive and empathetic environment, emotionally intelligent teams can better leverage diverse perspectives, address issues constructively, and make decisions that consider both the logical and emotional aspects of a situation. In practice, this means leaders must get out of the office, interact, and build relationships with all their people. Leaders cannot lead those whom they do not know.
Collaborative Climate
A positive and collaborative team climate encourages members to work together harmoniously. This involves fostering a sense of belonging, encouraging cooperation, consciously building trust, and valuing diverse perspectives. It also means avoiding hidden agendas. In the military, frequent postings necessitated immediate collaboration when joining a new team. While the rank system helped, sustained collaboration depended on leaders walking the walk.
Decision-Making Processes
Establishing clear and efficient decision-making processes ensures that the team can make timely and well-considered decisions. This includes defining how decisions will be made, who will be involved, and how conflicts will be resolved. Sustaining these processes as cultural norms is critical. Choose a process that meets the complexity of the problem and stick with it. Reinventing the wheel with each decision-making process is inefficient and only sustains chaos.
Leadership and Guidance
Effective leadership is critical for steering the team in problem-solving until the team is ready to take on the responsibility of problem-solving themselves. Leaders should facilitate discussions, encourage participation, and provide direction while empowering team members to take ownership of their decisions.
Diversity and Inclusion
A diverse team brings a variety of perspectives and experiences, which can enhance decision-making. Inclusive practices ensure that all voices are heard and considered, leading to more comprehensive and innovative solutions. In one particularly difficult engineering problem, bringing in an HR professional and a receptionist provided considerable insight that complemented the usual engineering-focused thinking.
Conflict Resolution Skills
Conflict is not unusual when developing and nurturing teams. However, developing skills to manage and resolve conflicts constructively ensures that disagreements do not hinder the team’s progress but instead can lead to better decision-making.
Continuous Improvement
A commitment to continuous improvement helps teams to reflect on their processes and outcomes, learn from their experiences, and make necessary adjustments to enhance their effectiveness. Enable the team to set aside time to learn from their experiences and build their expertise or live with lost opportunity.
Wrapping Up
We have detailed the critical characteristics that will enable you to nurture your teams to become decision-makers and problem solvers. Now comes the tough part: the path of change.
In our next article, we will detail how you can nurture your people through the complex path of change, teach you about change readiness, how to avoid change fatigue, and how to be successful by following the RESPECT© change program.
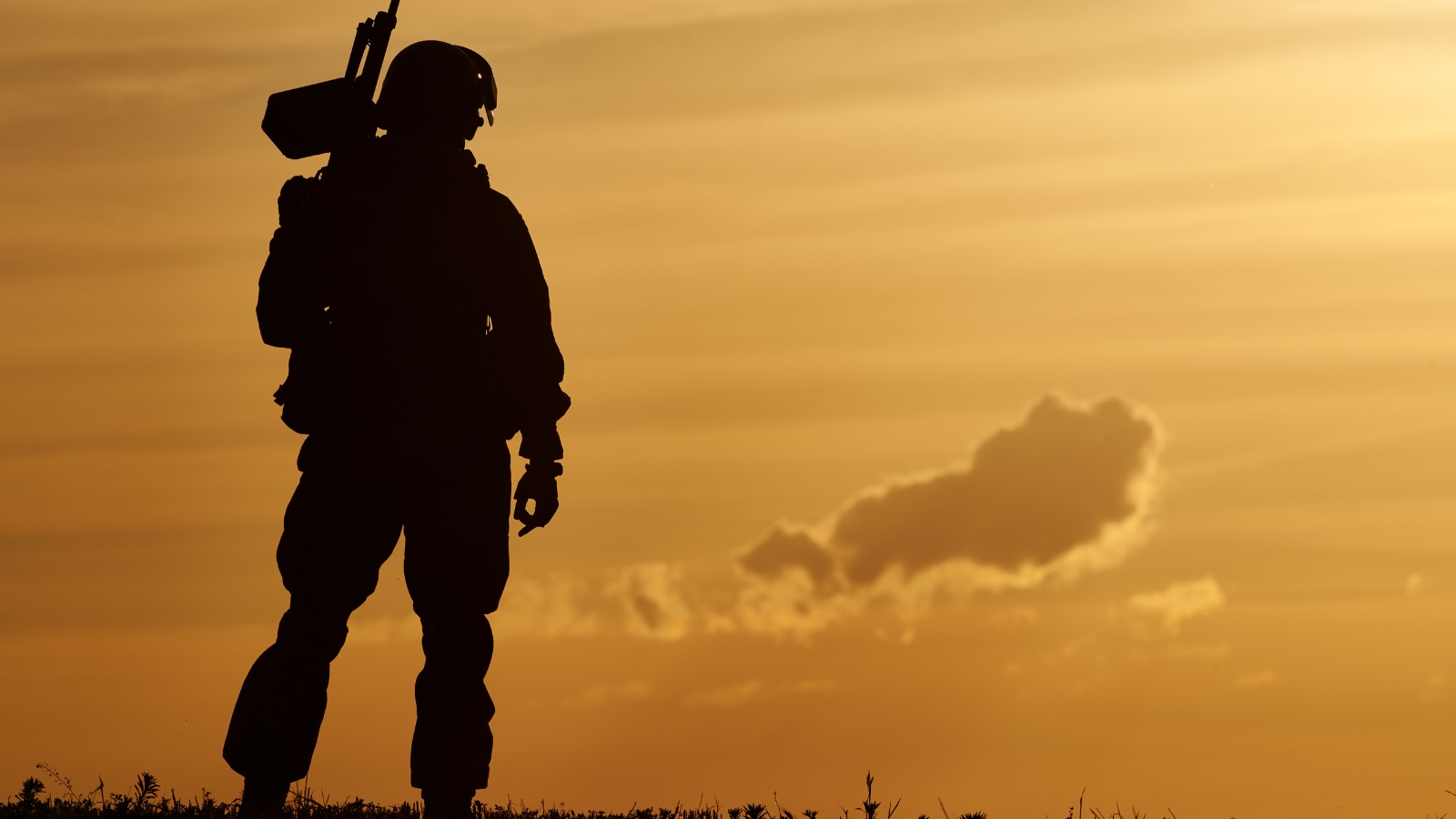
Leadership Lessons for Civilian Life
Leadership is often shaped by defining moments, and how leaders reflect on these experiences can define their future growth. Drawing from personal leadership insights during military service—particularly from the high-pressure environment of the Kosovo War—we have identified key lessons that translate seamlessly into civilian and industrial leadership practices.
Seizing Unexpected Opportunities
One defining leadership moment came from an unexpected call to deploy as a spokesperson in Kosovo during the war. At the time, stationed at RAF Coningsby, the news came suddenly: within a week, it was time to pack bags, re-certify on a personal weapon, and prepare to face an unfamiliar role in a challenging environment.
Reflective Point: Leadership opportunities often arise at unexpected times and in unexpected ways. Embracing these challenges can accelerate personal and professional growth. The ability to step outside of comfort zones and adapt quickly is a critical trait for effective leadership, whether in a war zone or the business world.
Leading with Unconditional Trust
In Kosovo, the leadership challenge involved managing a diverse team of 38 military and civilian personnel from 15 different countries, including individuals from groups historically in conflict, such as Serbs and Albanians, Turks and Greeks. To further complicate matters, team members were constantly rotating in and out, creating an unstable and fluid environment. There was no time for trust to develop gradually—trust had to be given immediately.
Rather than waiting for trust to form, the approach was to grant trust from day one. By trusting the team’s professionalism, integrity, and expertise upfront, cohesion was built rapidly, even among individuals from conflicting backgrounds. Only once did this trust break down, but overall, it was key to the team’s success.
Reflective Lesson: In high-pressure environments, leaders don’t always have the luxury of time to build trust gradually. Sometimes, trust needs to be given unconditionally from the outset. By leading with trust, leaders can create quick cohesion, fostering collaboration even in diverse and challenging settings.
The Power of Asking “What Else?”
Leadership isn’t just about completing the mission—it’s also about asking, “What else can I do to improve the situation?” In Kosovo, the mental well-being of both soldiers and civilians was a significant concern. Far from home, dealing with the constant pressures of conflict, many struggled with stress and isolation. Recognising this, leaders established a “drop-in centre” where personnel, regardless of nationality or rank, could gather for support and conversation. This simple initiative provided an informal space for connection and helped reduce some of the mental health pressures facing the team.
Additionally, several tragic accidents involving children and unexploded munitions became another pressing concern. A media campaign was launched to educate local children on the dangers of discarded munitions, ultimately reducing child fatalities related to these explosives. Over six months, the deaths dropped from 23 to zero.
Reflective Point: Great leadership goes beyond simply achieving goals—it’s about looking at the bigger picture and asking, “What else can I do to make a difference?” Even small actions can create meaningful, lasting impacts on the lives of those you lead. Leaders must remain aware of the broader context and take steps to address challenges that may not be immediately obvious.
Leading with Intentionality
Intentional leadership means taking the time to build genuine relationships with the people you lead. Whether in a war zone or a corporate setting, every interaction is an opportunity to strengthen bonds, foster trust, and boost team performance. Simple gestures—such as regularly asking team members, “How are you?” and following up with “No, really, how are you?”—can create a culture of openness and psychological safety. These moments of genuine care lead to stronger relationships, better communication, and higher-performing teams.
Reflective Point: Leadership requires intentionality. Every interaction with your team is an opportunity to build trust, show empathy, and strengthen relationships. Being intentional about how you engage with your team can have a profound impact on team morale, performance, and overall success.
Wrapping Up
Effective leadership is rarely straightforward. It involves seizing unexpected opportunities, building trust quickly, going beyond the immediate task to ask “What else can I do?” and leading with intentionality. At Project7 Consultancy, we believe that reflective practice is essential to multiplying the value of experience. Reflection helps leaders learn continuously and improve their leadership practices, making them more effective and impactful.
Leadership is more than just achieving business objectives—it’s about creating lasting, positive change in the lives of those you lead. By reflecting on experiences and asking deeper questions, leaders can drive not only success but also meaningful impact.
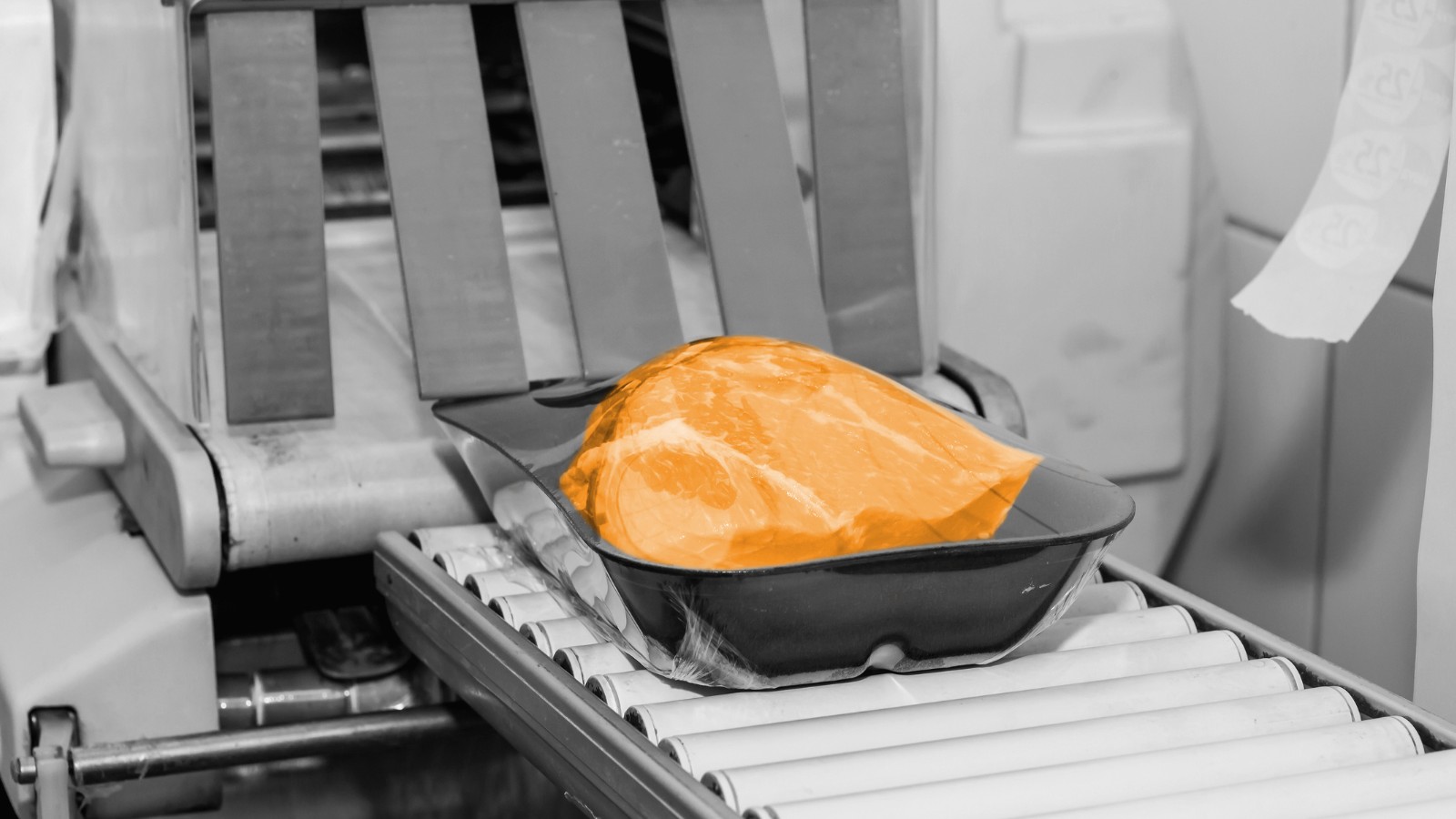
Reflecting on our Lean Leadership & Line Performance Improvement Project
Delivering targeted interventions that result in measurable improvements is essential for any organisation looking to enhance operational performance. One of our previous projects involved working with a leading food producer in Europe to transform leadership capabilities and improve line performance across multiple sites. This post explores the challenges, solutions implemented, and the significant outcomes we achieved.
Our client, a leading producer of beef, pork, chicken, and convenience products, was facing significant operational issues across its UK facilities. One site, in particular, a sliced cooked meats plant, was experiencing a weekly financial loss of approximately £195,000. The company was also dealing with inefficient factory layouts, excessive raw material waste, and low engagement between cross-functional teams. These issues were compounded by poor customer satisfaction due to a high number of complaints, making it clear that sustainable improvements were urgently needed.
Challenges
Several critical issues were identified during the initial analysis:
- Operational Inefficiencies: Factory layouts were inefficient, resulting in high levels of waste and poor visual controls for tracking material movement and setting priorities.
- Low Engagement: Engagement between operations and cross-functional teams was lacking, with little ownership of ideas at the shop-floor level.
- Directive Management Style: The existing management approach was more directive than collaborative, stifling innovation and failing to motivate employees to engage in continuous improvement.
- High Financial Losses: The sliced cooked meats plant, in particular, was losing approximately £195,000 per week, a situation made worse by poor-quality standards and repeat customer complaints.
Solutions
In response to these challenges, a comprehensive Lean Leadership Programme was designed and implemented. The programme focused on improving leadership skills and operational efficiency, with the initial deployment taking place at the sliced cooked meats plant and later expanding to seven other sites across the UK.
Key solutions included:
- Lean Leadership Academy (LLA): A training programme that engaged 52 operational leaders across various disciplines, including technical, engineering, logistics, and HR. This programme was instrumental in developing leadership skills and creating a culture of continuous improvement.
- Facility Layout Redesign: A detailed plan was developed to improve the layout and efficiency of the plant, reducing waste and improving material flow.
- Value Stream Mapping (VSM): This activity identified areas of waste within the processes and enabled the team to implement targeted improvements.
- Line Performance Improvements (LPI): Specific projects were undertaken to improve the performance of production lines across the UK sites.
- Continuous Improvement Team: A dedicated team was established by the client to sustain improvements and ensure ongoing collaboration across functions.
Impact on Performance
The outcomes of these interventions were substantial, leading to significant cost savings and operational improvements:
- £991,600 in Savings: Ideas generated through Value Stream Mapping activities were implemented, delivering nearly £1 million in savings.
- £2.4 Million in Cost Avoidance: The implementation of tactical initiatives across seven sites resulted in £2.4 million in cost avoidance.
- 66% Reduction in Weekly Losses: The financial losses at the sliced cooked meats plant were reduced by 66%, representing a major turnaround.
- Gold Standard Accreditation: The improved processes and leadership led to Gold Standard Accreditation for food production, allowing the client to engage with high-profile customers such as Marks & Spencer.
- 60% Reduction in Customer Complaints: By improving product quality and operational processes, customer complaints were reduced by 60%.
Final Thoughts
This project demonstrated the transformative power of strong leadership, efficient processes, and a collaborative culture. By investing in leadership development and continuous improvement, the client was able to not only reduce costs but also improve product quality and customer satisfaction. The success of this project highlights the importance of a holistic approach to operational excellence, where leadership and line performance go hand in hand to achieve sustainable results.
For more information on how similar interventions can help your organisation achieve operational excellence, feel free to contact us.
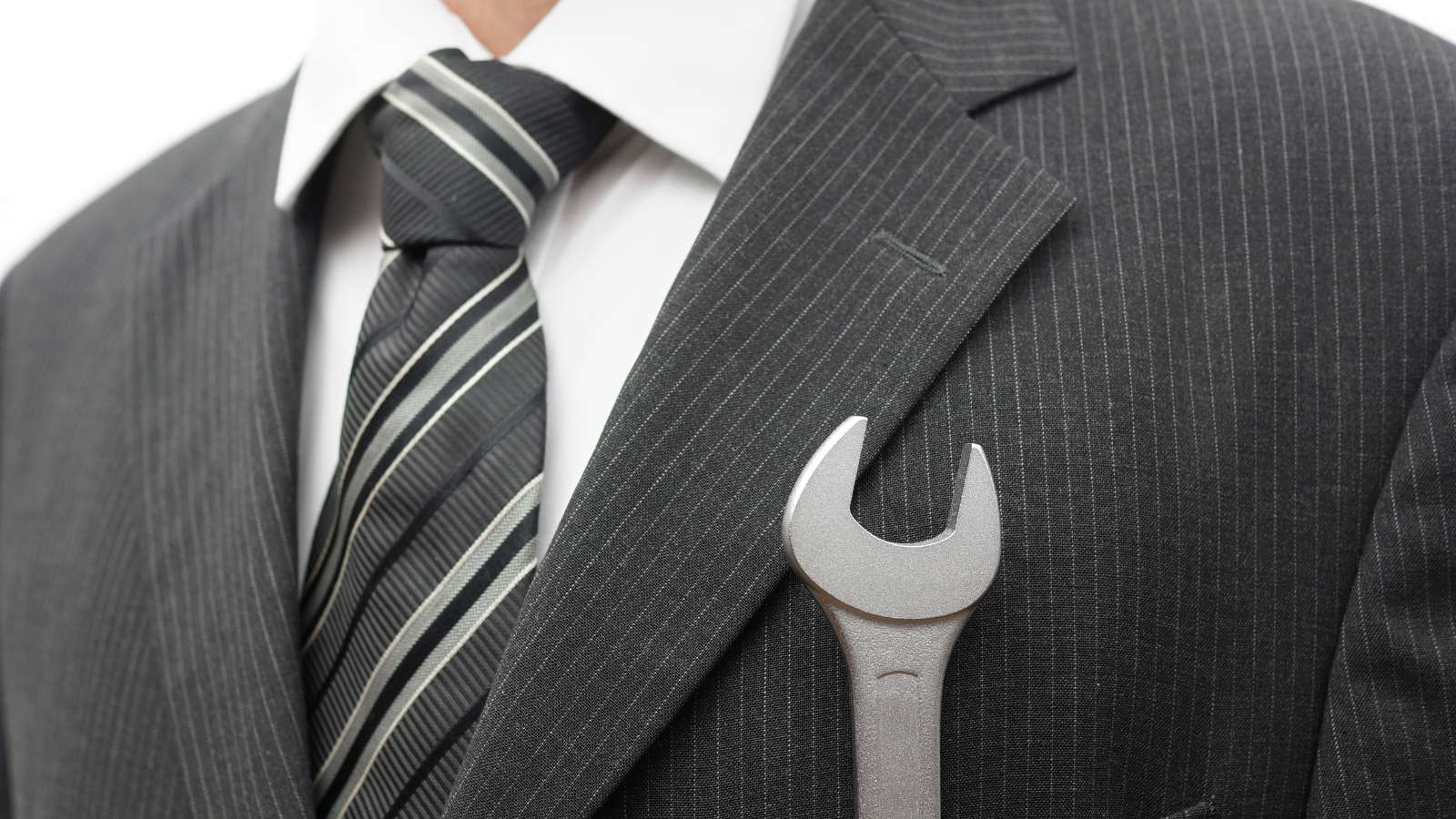
A Survival Guide for New Leaders
We frequently encounter leaders who have recently transitioned from expert technical roles to leadership positions, often with little or no preparation. While the promotion is gratifying, many quickly realise they are not fully equipped for the shift. This lack of preparation not only impacts the individual but also affects the wider team and department.
There are two main reasons why this is bad for business:
- The organisation loses a top performer in their technical role, who may now struggle in leadership, taking months to adjust or potentially leaving the company.
- The department suffers because the new leader is not set up for success, which can lead to disengagement and confusion.
This survival guide is designed to help you navigate this transition, providing practical tips and strategies to move from expert technician to effective leader, while building on the skills you already possess.
Part 1: Embracing Your New Role as a Leader
- Understand the Shift from Technician to Leader
As a technician, your role was about “doing the work.” As a leader, your focus shifts to “enabling others to do the work.” Your primary responsibility is now your team’s performance, development, and engagement. Success is no longer about what you achieve personally, but what your team achieves collectively.
Reflection: Think about what support and guidance you needed when you were in a technical role. Now, your job is to provide that for your team.
- Leverage Your Technical Expertise Wisely
Your technical knowledge is an asset, but it’s important to use it strategically. It helps build credibility with your team, but your role is to mentor and guide, not to do the work yourself. Avoid micromanaging or stepping in to “fix” everything—this undermines your team’s confidence.
Reflection: Consider the times when your manager helped you solve problems versus when they stepped in to take over. Strive to be the leader who empowers, not the one who controls.
- Adopt a Leadership Mindset
Leadership is about people, not just processes. Shift your focus from your own tasks to understanding your team members—their strengths, weaknesses, and motivations. Developing emotional intelligence (self-awareness, empathy, and active listening) is key to creating a positive work environment.
Reflection: Reflect on moments when you felt valued and supported by a leader. What behaviours made you feel that way, and how can you apply them with your team?
Part 2: Building Trust and Credibility Quickly
- Start by Listening
One of the fastest ways to build trust is to listen. Conduct one-on-one meetings with each team member to understand their roles, challenges, and career goals. Listen more than you speak, and care about their answers. Take the time to learn about your team members on a personal level to build rapport.
Reflection: Think about a time when a leader took the time to listen to you. How did it make you feel, and how can you replicate that with your team?
- Communicate Transparently and Often
Set clear expectations from the start—communicate your vision, goals, and how you plan to support the team. Be honest about what you know and what you’re still learning. Transparency builds credibility and trust.
Reflection: Remember times when you were kept informed versus when you were left in the dark. Use that experience to shape how you communicate with your team.
- Establish Early Wins
Look for small opportunities to make meaningful improvements. This demonstrates your commitment to the team’s success and builds momentum. Recognising team achievements, big or small, helps boost morale and set a positive tone for the future.
Reflection: Reflect on times when a leader celebrated team wins and how it affected morale. Make it a priority to celebrate success.
Part 3: Managing and Motivating Your Team
- Delegate Effectively
Delegation is key to leadership. Assign tasks based on each team member’s strengths and trust them to deliver. Avoid the temptation to micromanage—your role is to guide, not to control.
Reflection: Consider how empowering it was when your leader trusted you with responsibilities. Give your team the same level of trust to foster growth and accountability.
- Foster a Positive Team Culture
Create opportunities for collaboration and open communication. A strong team culture is built on trust, and it grows when people feel that their contributions are valued. Provide regular, constructive feedback and encourage an open two-way dialogue.
Reflection: When have you felt part of a supportive team culture, and how did your leader contribute to that? Model similar behaviour to strengthen your team.
- Motivate Through Recognition and Development
Recognition is one of the most powerful motivators. Acknowledge both individual and team achievements publicly and privately. Additionally, invest in the development of your team members by offering training and mentorship opportunities.
Reflection: Think about how you felt when your work was recognised by a leader. Now make it a priority to do the same for your team members.
Part 4: Developing Yourself as a Leader
- Seek Continuous Learning Opportunities
Leadership is a journey, not a destination. Seek out mentors who can guide you and offer wisdom. Engage in leadership training, read books, and attend workshops to continually build your skills.
Reflection: Reflect on your own development. Just as you became an expert technician, now focus on becoming an expert leader.
- Practice Self-Reflection
Regularly reflect on your actions and decisions. Ask yourself what went well and what could be improved. Seeking feedback from your team and peers is also essential in refining your leadership approach.
Reflection: Set aside time each week to review your leadership actions. Think about their impact on your team and how you can improve.
- Manage Your Time and Energy
Prioritise tasks that have the greatest impact on team and organisational goals. Use tools like the Eisenhower Matrix to manage time effectively. Also, remember that leadership is demanding—prioritise self-care to ensure you’re at your best.
Reflection: Think about how you manage your time. Focus on high-impact tasks and delegate where possible.
Quick Reference Tips for New Leaders
- Find a Mentor: Seek someone you trust to guide you through your leadership journey.
- Communicate Clearly and Frequently: Keep your team informed and aligned.
- Build Relationships: Invest time in building trust with your team.
- Lead by Example: Model the behaviour you expect from your team.
- Delegate and Empower: Trust your team to take ownership of their work.
- Stay Humble and Open to Learning: Always acknowledge what you don’t know.
- Ask Questions: There’s no such thing as a dumb question—be curious and open.
Wrapping Up
Transitioning from a technical expert to a leader is challenging, but with the right mindset, you can succeed. Leadership isn’t about having all the answers; it’s about creating an environment where your team can thrive. Use your technical expertise as a foundation, but focus on developing the soft skills necessary to motivate, engage, and lead your team to success. Leadership is a journey, and with time, practice, and self-reflection, you’ll grow into the role and thrive.
If you find yourself in a leadership position for which you feel unprepared, Project7 has experts and training programmes that can help. Contact us for a chat to see how we can support your leadership development journey.
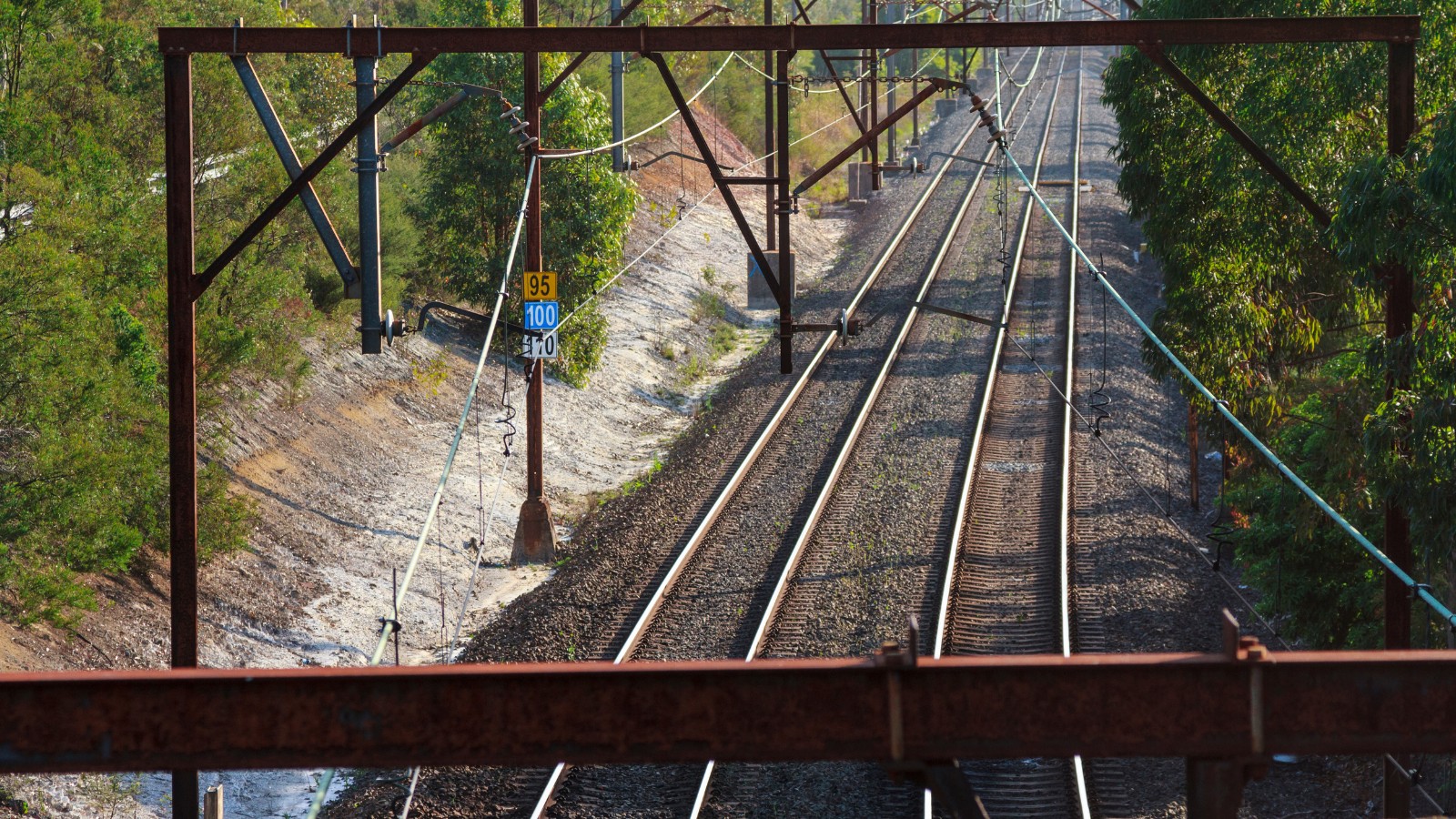
Production Planning Process Improvement Project
Delivering impactful change that enhances operational efficiency and delivers measurable results is critical for any large-scale organisation. In one of our previous projects, we helped transform the production planning processes at a major suburban rail network in New South Wales, Australia. This reflection explores the challenges faced, solutions implemented, and the outcomes achieved throughout the collaboration.
The company operates over 815 km of track and 178 stations, serving millions of passengers annually. The Major Works division, responsible for maintaining and upgrading the rail network, was undergoing a transformational reform to improve the efficiency and performance of its operations. The team engaged Project7 to assist in developing a Production Planning Process that would enhance the delivery of their annual works programme and drive a cultural shift towards better coordination and commercial focus.
Challenges
The company faced several operational challenges that hindered their ability to meet service and maintenance goals. These included:
- Incomplete Work and Rework: Many projects were not completed within the allotted time, leading to repeated site visits, rework, and increased costs.
- Poor Forecasting: A lack of visibility into the work demand forecast from the annual works programme made it difficult to plan effectively, resulting in delays.
- Safety Concerns: Inconsistent pre-work site inspections and safety briefings led to a high Total Recordable Injury Frequency Rate (TRIFR).
- Unstructured Planning: An inconsistent approach to planning across teams led to resource underutilisation and poor communication within and between departments.
- Lack of Accountability: The absence of structured pre- and post-possession reviews meant that lessons were not learned, and planning was not adjusted for future projects.
Solutions
We undertook a comprehensive diagnostic phase to understand the current state of Project Operations. Through collaborative workshops and process mapping exercises with the delivery teams, we developed a robust Production Planning Process focused on improving safety, quality, delivery, cost, and people performance metrics.
Key solutions implemented included:
- Policy Deployment: We aligned corporate goals with actionable targets for staff at all levels, ensuring everyone was working towards common objectives.
- Visual Performance Management: Standardised visual management boards were introduced across different teams (Track, Signals, Electrical), providing a transparent system to track progress and communicate project status.
- Structured Performance Reviews: Weekly reviews led by team managers ensured accountability and provided regular updates on the status of each project, improving ownership and responsibility across the team.
- Safety and Pre-Work Improvements: Safety briefings and pre-works meetings were reintroduced, along with a Short Interval Control system to track plan versus actual performance in real-time.
- Clear Communication Channels: Improved communication within and across teams was achieved by integrating Team Leaders into the production planning process, helping to streamline project execution.
Impact on Performance
The implementation of the Production Planning Process led to substantial improvements in operational efficiency, cost control, and safety:
- 40% Reduction in TRIFR: Consistent safety briefings and improved pre-work site inspections led to a significant reduction in injuries.
- 1% Increase in Delivery: The Annual Works Programme saw a 1% increase in completion, reflecting a more efficient project execution process.
- $2.5 Million in Cost Savings: Continuous improvement initiatives identified significant opportunities for cost reduction, resulting in a 6:1 Return on Investment.
- $13 Million Reduction in Maintenance Costs: Net operating costs came in $13 million under budget, highlighting the financial impact of better planning and execution.
- 10% Improvement in Post-Works Asset-Related Delays: Improved planning and coordination resulted in fewer delays following project completion, enhancing service reliability.
Final Thoughts
This project demonstrated how structured planning, clear communication, and consistent performance management can lead to significant operational improvements. By implementing a clear Production Planning Process and encouraging a culture of accountability, this New South Wales based train operator saw improved efficiency, reduced costs, and enhanced safety, ultimately delivering a better service to its passengers.
At Project7 Consultancy, we remain dedicated to helping organisations achieve their operational goals through tailored solutions and strategic interventions. For more information on how we can help your organisation achieve similar success, contact us directly.
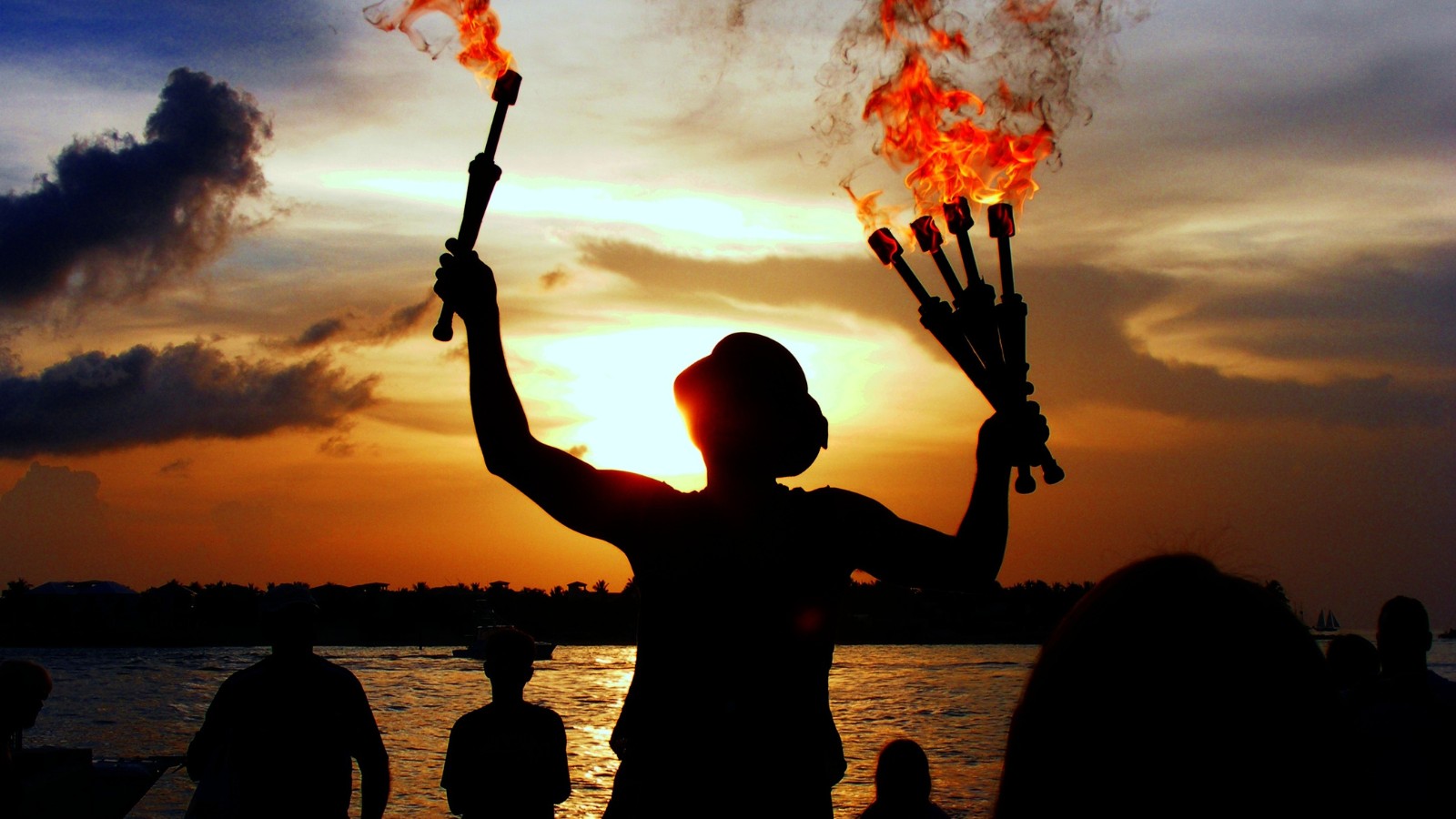
Balancing Authentic Leadership in Industry 5.0
Industry 5.0 represents the next phase of industrial evolution, characterised by the integration of human intelligence with advanced technologies like artificial intelligence (AI), robotics, and the Internet of Things (IoT). This evolution builds on Industry 4.0’s focus on automation and efficiency but places greater emphasis on human-centric values, sustainability, and resilience. In this context, authentic leadership becomes critical.
Reflective practice and perception are vital components that enable leaders to navigate this complex landscape effectively.
These are areas that may have previously been only cursory considerations as leaders focused on looking after their people, building production, maintaining efficiency, and constantly driving to cut costs. Sometimes, it can feel like juggling multiple priorities at once.
This article explores the role of reflective practice and perception in fostering authentic leadership within the framework of Industry 5.0, discusses their alignment with the human-centric values that Industry 5.0 promotes, and offers insights into how leaders can balance these responsibilities effectively.
The transition to Industry 5.0 marks a significant shift in how industries operate, moving from a purely technology-driven approach to one that emphasises a greater understanding of how humans collaborate with AI. This new way of working requires leaders who are not only technologically savvy but also deeply authentic—leading with empathy, ethical integrity, and a focus on the well-being of both employees and the broader impact of industrial outputs on society. Reflective practice and how others perceive leadership now become critical in developing and maintaining this authenticity.
Reflective Practice in Authentic Leadership
Reflective practice involves continuously analysing one’s actions, decisions, and interactions to learn and improve. For leaders in Industry 5.0, reflective practice is essential for maintaining authenticity in a rapidly changing technological landscape. It fosters self-awareness, enabling leaders to align their actions with their core values and the human-centric ethos of Industry 5.0.
The rapid advancements in AI, robotics, and IoT require leaders to constantly adapt. Reflective practice allows leaders to evaluate how these technologies impact their decision-making processes and the well-being of their teams. By reflecting on experiences, leaders can keep pace with technological changes while ensuring that their actions align with both their values and the broader goals of Industry 5.0.
Industry 5.0 places a strong emphasis on ethical considerations, particularly in the use of advanced technologies. Reflective practice provides the reference experiences needed to navigate new ethical dilemmas, ensuring that decisions are aligned with personal values and the ethical standards of the industry. This helps maintain authenticity by ensuring that actions are consistent with ethical beliefs, even when faced with new and complex technological challenges. Understanding one’s “true north” becomes essential in this context.
The need for rapid decision-making has always been present, but the integration of AI and other technologies into decision-making processes adds a new layer of complexity. Overcoming these challenges requires a commitment to conscious, reflective practice, honest self-examination, and building self-awareness, including understanding how external perceptions of leadership may evolve.
Perception and Authentic Leadership
Perception refers to how others view a leader’s actions, behaviours, and intentions. In the context of Industry 5.0, where human-centric values are paramount, the perception of a leader’s authenticity is important. Leaders perceived as authentic are more likely to inspire trust, foster collaboration, and drive innovation. Those who do not see authenticity as a virtue will quickly find themselves isolated from colleagues and their teams.
Industry 5.0 emphasises the importance of human creativity and innovation, which thrive in environments where leaders are perceived as authentic. When employees perceive their leaders as genuine, they are more likely to engage fully with their work, collaborate effectively, and contribute to innovative processes. This engagement is critical in a landscape where human creativity and machine efficiency must work in harmony.
The integration of advanced technologies in Industry 5.0 adds complexity to managing perceptions. Leaders must navigate the dual expectations of being both technologically competent and deeply human-centred. This requires transparency about decision-making processes, especially when these involve AI or other automated systems, to ensure that leaders are perceived as acting in the best interests of their teams and the wider community.
Perception gaps can be particularly challenging in Industry 5.0, where technology can either bridge or widen the gap between leaders and their teams. For example, the use of AI in leadership decisions might be perceived as impersonal or detached unless leaders actively communicate how these tools align with the organisation’s human-centric values. This is especially true if a leader merely repeats what an AI suggests without integrating their values or understanding the business culture.
Aligning Reflective Practice and Perception with Industry 5.0
Industry 5.0 also focuses on sustainability and ethical responsibility. Reflective practice and perception management are critical for leaders to navigate and sustain change in these complex areas. Leaders who regularly reflect on the ethical implications of their use of technology and seek to understand how their actions are perceived by others are better positioned to lead in ways that are both authentic and aligned with the sustainable goals of Industry 5.0. For example, repetitive manual tasks replaced by robots should be considered not only for efficiency but also for the impact on employment and societal well-being.
Reflective practice enables leaders to create environments that encourage innovation—a key component of Industry 5.0. By reflecting on leadership practices and how they are perceived, leaders can foster cultures where employees feel valued and empowered to innovate. This alignment of reflective practice and perception with the goals of Industry 5.0 ensures that leaders can drive both technological and human-centric progress.
Wrapping Up
Reflective practice and perception are critical components of authentic leadership, particularly in the context of Industry 5.0. Reflective practice helps maintain self-awareness, ethical integrity, and adaptability in the face of rapid technological change. Perception, on the other hand, ensures that leaders are seen as genuine and trustworthy, which is essential for fostering engagement and innovation in a human-centric industrial landscape.
By aligning these elements with the principles of Industry 5.0, leaders can effectively navigate the complexities of this new era, ensuring that their decisions remain authentic while driving both technological and human progress.
Leadership in this new era is challenging, but on reflection, being a leader rather than a juggler is where the true impact lies.
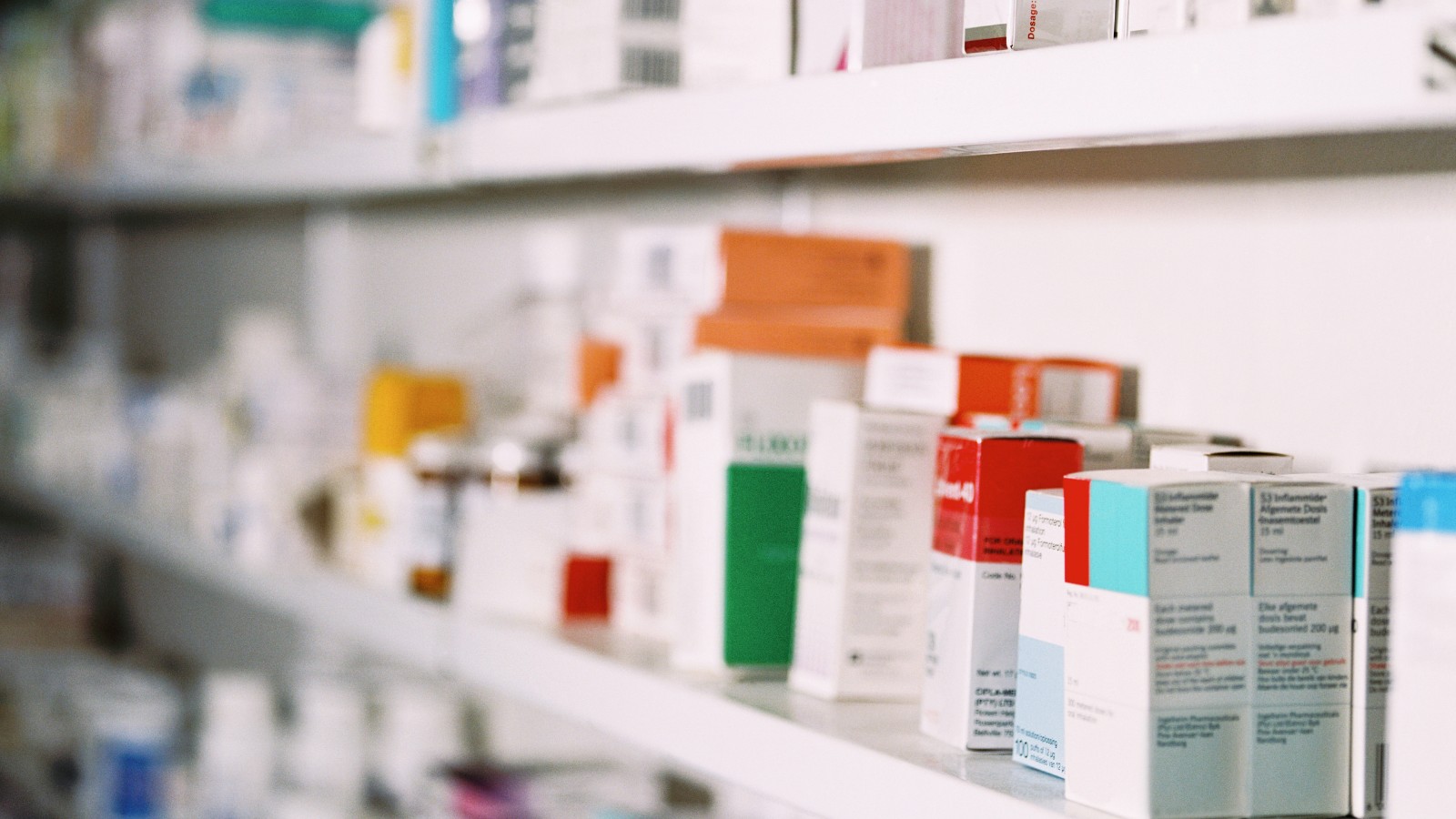
Reflecting on our Pharmacy Service Improvement Project
At Project7, our mission is to drive meaningful change that enhances operational efficiency and delivers tangible results. One of our previous projects involved a significant transformation in the pharmacy department of a UK Learning NHS Trust. This reflection explores the challenges, solutions, and outcomes of this pharmacy service improvement initiative.
The UK Learning NHS Trust, serving areas such as East Surrey, North-East West Sussex, and South Croydon, was facing significant operational and financial pressures. With an annual budget of £300 million and a £20 million overspend, the trust needed to find ways to reduce overall costs while maintaining or improving service quality. The pharmacy department, in particular, was underperforming, with high levels of patients being discharged without their necessary medication. This issue led to increased costs, inefficiencies, and low staff morale.
The challenges in the pharmacy were multifaceted. There was difficulty in processing a high volume of prescriptions, especially those arriving late in the day after ward rounds. Often, medications were delivered to wards after patients had already been discharged, leading to unnecessary waste and storage issues. Additionally, the pharmacy operated without a “first in, first out” system, causing significant delays in processing prescriptions. There was also no tracking system in place, which meant that staff often had to search for prescriptions manually, leading to further inefficiencies.
To address these challenges, Project7 took a comprehensive approach. We began by reviewing the pharmacy’s staffing levels and competencies to ensure they were aligned with the volume of work required. Through process mapping with professional staff, we identified areas for improvement and implemented a range of solutions.
One of the most impactful changes was the introduction of a “first in, first out” processing system, which significantly reduced wait times and improved overall efficiency. We also implemented short interval control to manage the variation in demand throughout the day. Additionally, a Plan, Do, Check, Act (PDCA) confirmation system was introduced to ensure that medications were only delivered if the patient was present to receive them, thereby eliminating unnecessary storage on wards.
The results of these interventions were substantial. The pharmacy saw a 59% reduction in turnaround time, bringing it down from an average of 3.4 hours to within the trust’s target of 2 hours. The department’s establishment was redefined with a plan for implementation, leading to a reduction in headcount by three substantive posts and a 70% reduction in locum spend. Moreover, a tracker system was introduced, providing better oversight of prescription processing and ensuring a more efficient workflow. The standard delivery route and times for porters were also formalised, further streamlining the process.
Reflecting on this project, several key lessons stand out:
- Process Standardisation: Implementing a “first in, first out” system and standard delivery routes drastically improved efficiency and reduced turnaround times.
Effective Use of Resources: Aligning staffing levels with the required workload and reducing reliance on locums not only saved costs but also improved overall service delivery. - Continuous Improvement: The introduction of a PDCA confirmation system ensured that improvements were sustained and that medications were delivered only when needed, reducing waste and inefficiencies.
- Collaboration and Communication: Engaging staff in process mapping and decision-making fostered a sense of ownership and commitment to the improvements, leading to a more motivated and effective team.
This project demonstrates the transformative impact that targeted operational improvements can have on service delivery within a healthcare setting. At Project7 Consultancy, we remain committed to helping our clients achieve operational excellence through innovative solutions and continuous improvement strategies.
For more information on how Project7 Consultancy can help your organisation achieve similar success, contact us directly. We can help you maximise your business change potential.
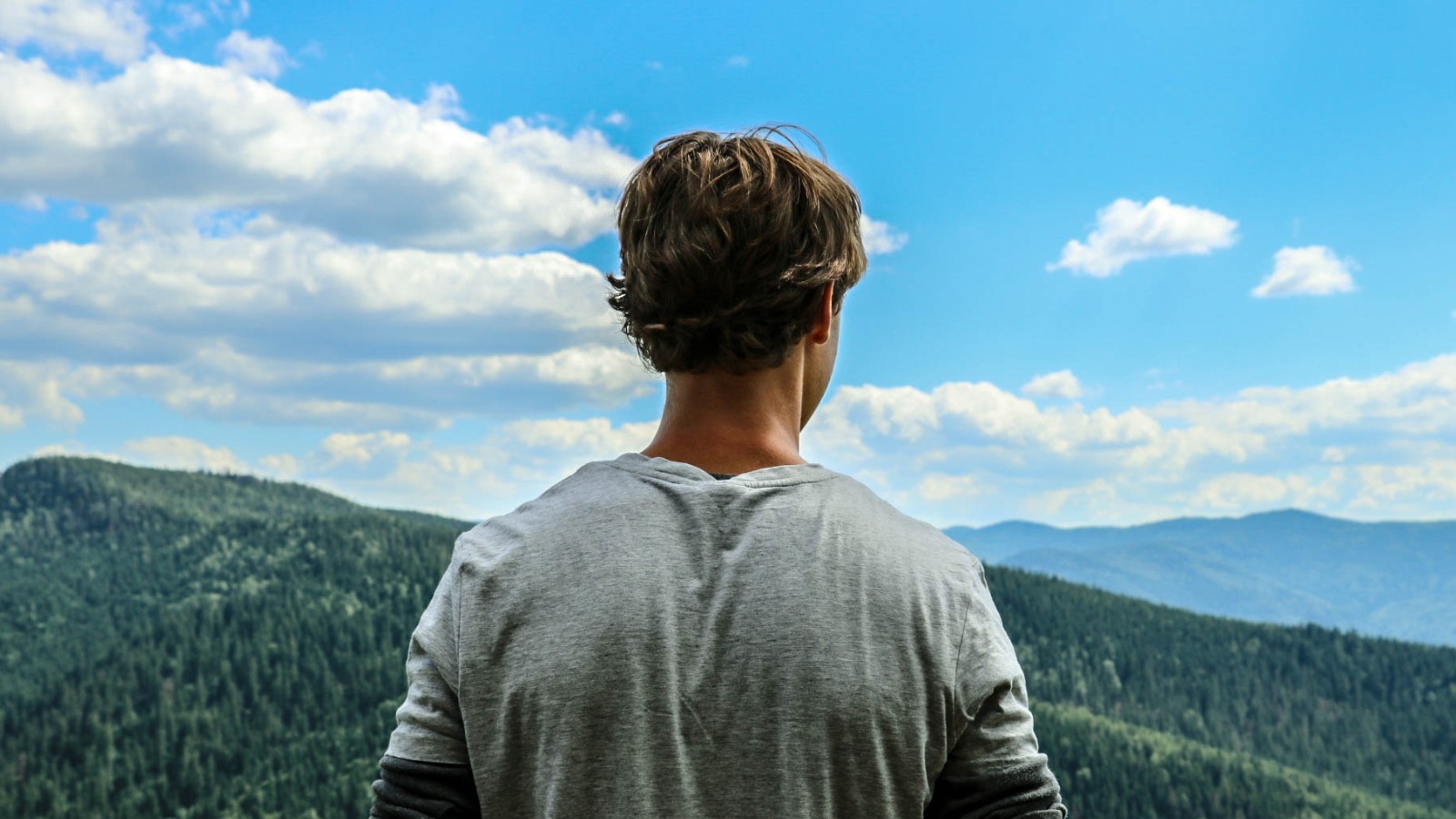
Change: Victim or Participant?
A common belief in business is that “People do not like change.” However, our experience shows that people actually live in and understand the need for constant change. What they resist is the feeling of a lack of control, which can bring insecurity, confusion, and disorientation.
Change is a constant in life, driven by factors such as politics, economics, societal shifts, technological advancements, and environmental urgency. These changes profoundly influence individuals and businesses. What people struggle with is not change itself, but the way it is implemented, which significantly affects how they perceive and react to it.
In our experience, the success of change hinges on how it is implemented. The way people are involved determines whether they see themselves as participants in change or as victims of it. When people feel like they are part of the process, they are more likely to embrace change, rather than resist it.
The Dynamics of Successful Change
Successful change, characterised by inclusivity and collaboration, begins with engaging people in the initial planning and implementation stages. This early involvement is known as a business’s readiness for change and is critical for long-term success. When people and teams are engaged and empowered from the start, they are more likely to embrace change, adapt positively, and take ownership of its longevity.
This approach is grounded in principles such as psychological safety, emotional intelligence, authentic leadership, transparency, two-way communication, and focused empowerment. By involving those impacted by the change in the decision-making process, leaders can tap into innovative ideas and fresh perspectives, leading to more robust and acceptable solutions. Early engagement also helps prevent change fatigue, which arises from ongoing, relentless change without a clear understanding of its purpose or results.
A key element of participatory change is communication within a culture of psychological safety. Clear, honest, and ongoing communication builds trust and understanding. It allows individuals to voice their concerns, ask questions, and contribute ideas. This two-way interaction ensures that the change process is responsive to the needs and aspirations of those involved. When people feel heard and valued, they are more likely to support and drive the change.
True empowerment is key—not just the word “empowerment” used as a buzzword, but actual empowerment that involves providing individuals with the tools, resources, and authority to lead and influence change. Leaders must focus on removing barriers so their teams can succeed. This requires trust, training, opportunities for collaboration, coaching, and mechanisms for feedback. When people are truly empowered, they become active participants in the change process, contributing their skills and enthusiasm to achieve shared business goals.
The RESPECT Model of Change
A practical tool to guide people through change is the Project7 Consultancy RESPECT model:
- R: Realise that your business’s history, built by your people, has brought you to where you are today. Honour that history as you move forward. Take time to conduct a thorough diagnostic before implementing any change.
- E: End point. Clearly articulate your end goal so your people know when they have reached the destination of the change journey.
- S: Survey the road ahead. Work with your people to delineate milestones that track the progress of change and celebrate incremental achievements.
- P: Plan for ongoing change. Be open to adaptation as new data emerges. The path to or even the end point may change for the better as everyone contributes to the journey.
- E: Engage your people from the outset in communication about the ‘why’ of change. Engaged people will lead; disengaged people will become obstacles.
- C: Coach through the change process. Remember, “Coach, don’t tell.” Motivated people will find ways to overcome seemingly impossible obstacles.
- T: Set a timed goal to reach the end point of the change. Both business and individuals need to see an end on the horizon to measure success and avoid change fatigue.
The Pitfalls of Top-Down Change
Far too often, change is imposed from the top down in businesses without conversation or engagement, leaving individuals asking, “Why are we doing this?” and “What was wrong with the old way?” Top-down change often leads to feelings of disenfranchisement and victimhood, where decisions are made by those at the top with little or no input from those affected. This lack of involvement fosters resistance, apathy, and a sense of helplessness among those on the receiving end of change.
One of the primary consequences of top-down change is the erosion of trust. When change is imposed without explanation or consultation, it creates suspicion and fear. People may feel that their needs and opinions are being ignored, leading to resentment and opposition. This lack of trust undermines the effectiveness of the change and damages relationships within the organisation and its leadership.
The Importance of Participation
To transform potential victims of change into participants, it is essential to create an environment that fosters communication and collaboration. This begins with a shift in leadership mindset, from one of control to one of facilitation. Leaders must recognise the value of involving people at all levels in the change process and be willing to relinquish some power and responsibility. This approach not only leads to more effective and sustainable change but also builds a stronger, more resilient business. People who feel like active participants in the change process will be engaged, motivated, and committed to achieving business goals.
Wrapping Up
Change is an inevitable part of business life, but how it is experienced can vary dramatically. Successful change is a function of real empowerment, honest collaboration, open communication, and active participation, all of which foster a sense of ownership and control. In contrast, top-down change can leave people feeling like victims, disconnected from the process and its outcomes. By prioritising participation and inclusivity, leaders can transform change from a source of anxiety and resistance into an opportunity for business growth and innovation. Through effective communication, empowerment, and collaboration, leaders must ensure that people feel like participants in change, not victims of it.
If you are facing a change scenario, are unsure how to prepare for change, or are in an organisation suffering from change fatigue, contact us. We can help you maximise your business change potential.
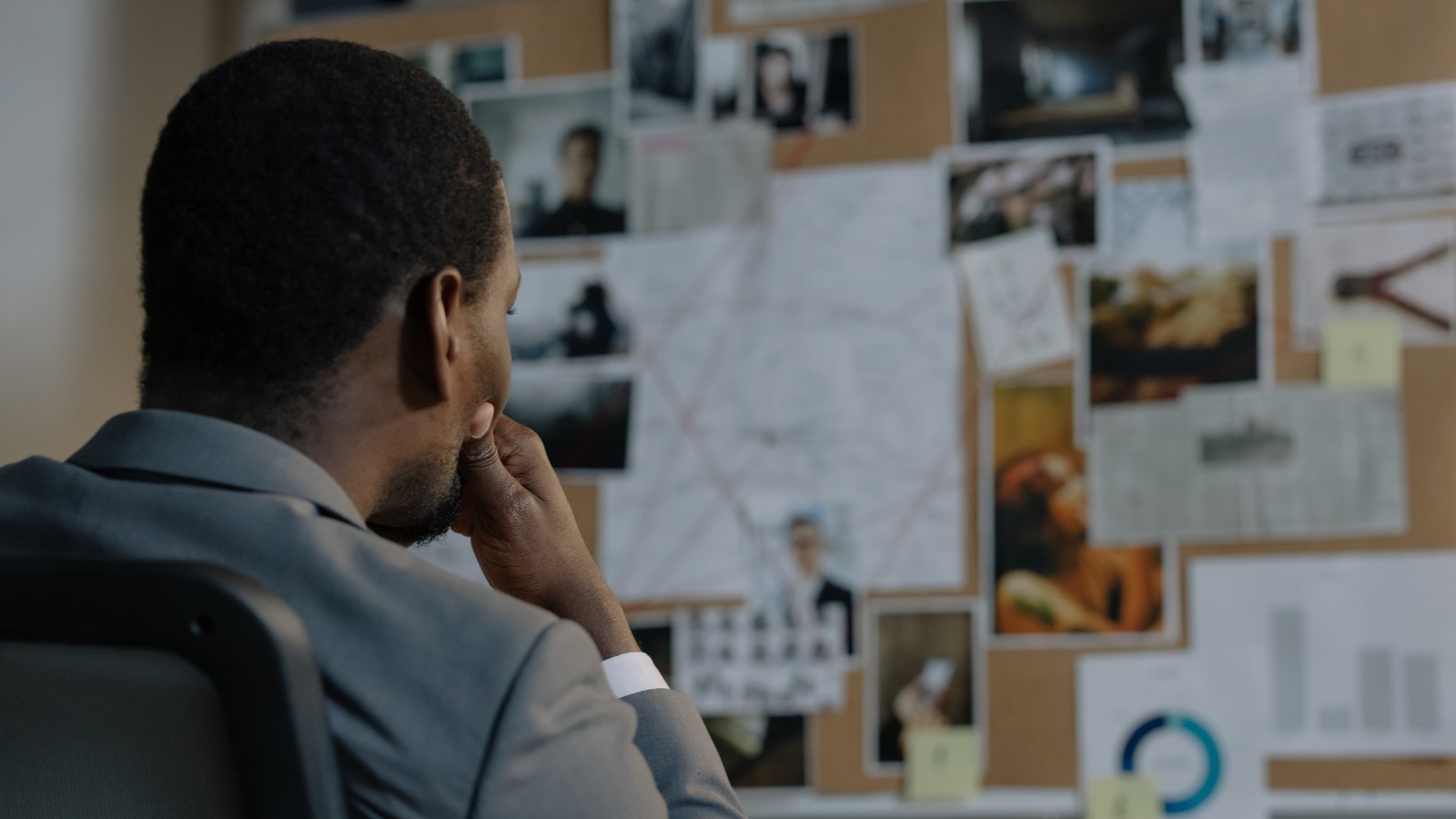
Why Hermeneutics Matters in Progressive Leadership
Embracing progressive leadership approaches is vital for fostering innovation, inclusivity, and growth. Progressive approaches, such as the need for and understanding of psychological safety, are now seen as key to promoting inclusivity and growth. However, what often goes overlooked is the significance of hermeneutics—understanding how meaning is shaped through language—in creating effective leadership strategies.
At its core, hermeneutics teaches us to delve beyond surface meanings and uncover deeper layers of understanding. By applying hermeneutical principles in leadership, we can cultivate empathy, foster more constructive communication, and enable transformative collaboration within our teams and organisations.
Understanding Diverse Perspectives
Hermeneutics encourages leaders to approach situations with an open mind, recognising the multiplicity of interpretations that exist. By valuing diverse perspectives and experiences, leaders can foster a culture of inclusivity and innovation. This interpretive flexibility is important in leadership because it encourages leaders to remain adaptable and open to multiple viewpoints. By acknowledging that different team members may interpret the same message in varied ways, leaders can tailor their communication strategies to better meet the needs of their audience and avoid misunderstandings.
Facilitating Meaningful Dialogue
Effective leadership involves more than just issuing directives; it requires the ability to engage in meaningful dialogue with team members. Drawing upon hermeneutical principles, leaders can create spaces for dialogue where individuals feel heard, valued, and empowered to contribute their insights. Hermeneutics reminds us that understanding is a two-way process, which is vital for fostering open communication and mutual respect in the workplace.
Navigating Complexity
Leaders must navigate ambiguity and uncertainty with agility. Hermeneutics equips leaders with the critical thinking skills necessary to interpret complex situations, identify underlying patterns, and make informed decisions that drive progress. The historical roots of hermeneutics, originally developed for interpreting religious texts, emphasise the importance of interpretation in understanding human behaviour and communication. This deep-rooted method remains relevant in helping leaders navigate the complexities of modern business challenges.
Inspiring Vision and Purpose
Successful leadership is often characterised by a compelling vision that inspires others to action. Hermeneutics can help leaders articulate their vision in a way that resonates with diverse audiences, fostering a sense of purpose and direction within the organisation. By understanding the deeper meanings behind words and actions, leaders can connect with their teams on a more profound level, inspiring commitment and enthusiasm towards shared goals.
Hermeneutics and Ethical Leadership
Hermeneutics also plays a significant role in ethical leadership. By encouraging leaders to consider the deeper meanings and implications of their decisions and actions, hermeneutics fosters a more reflective and ethically aware leadership style. Leaders who practice hermeneutical thinking are better equipped to consider the broader impact of their decisions on various stakeholders, leading to more ethical and socially responsible outcomes.
Hermeneutics and Conflict Resolution
In situations of conflict, hermeneutics provides a valuable framework for understanding the underlying issues and motivations that may not be immediately apparent. By applying hermeneutical principles, leaders can delve into the root causes of conflicts, understand the perspectives of all parties involved, and work towards resolutions that are more thoughtful and effective. This approach not only resolves conflicts but also strengthens relationships and trust within teams.
Hermeneutics and Continuous Learning
Hermeneutics encourages a mindset of continuous learning and growth. By embracing the idea that understanding is never complete and that there is always more to learn from others, leaders can cultivate a culture of continuous improvement within their organisations. This perspective aligns closely with the principles of Lean and other continuous improvement methodologies, reinforcing the idea that leadership is an ongoing process of learning, interpreting, and adapting.
As we embrace the challenges and opportunities of progressive leadership, let us not overlook the transformative power of hermeneutics. By incorporating hermeneutical principles into our leadership practices, we can cultivate environments that foster innovation, inclusivity, and meaningful change.
Take the time to understand what is going on beyond surface meanings and uncover deeper layers of understanding to develop your leadership and enable your teams to constantly improve and drive business through your leadership.
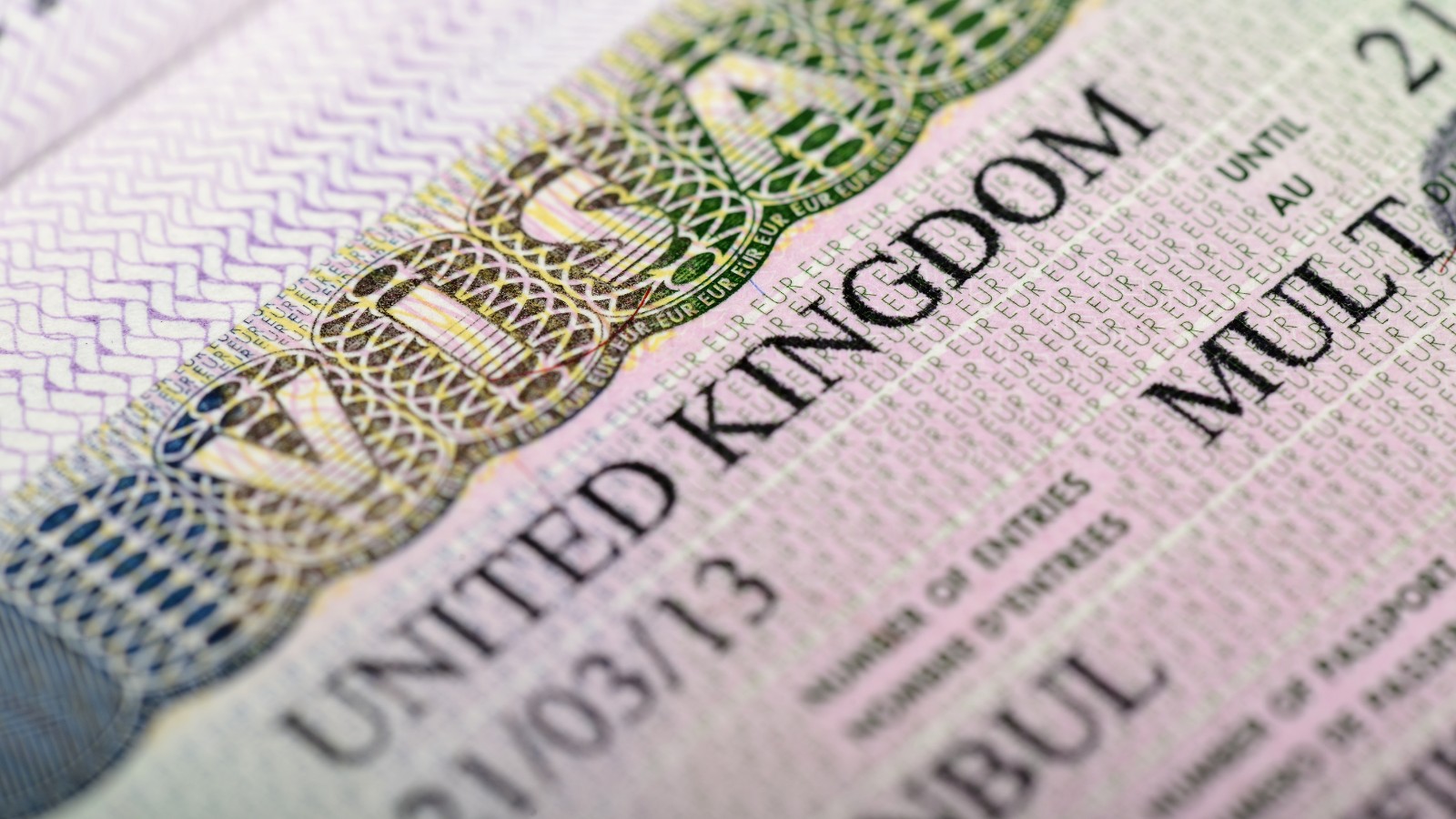
Reflecting on our Practical Problem Solving and Kata Coaching Project
One of the major outcomes of a Project7 engagement is to empower organisations with the tools and methodologies needed for continuous improvement. One of our significant previous projects involved enhancing the problem-solving capabilities of a major manufacturing facility. This reflection explores the challenges faced, solutions implemented, and the impactful outcomes achieved through practical problem-solving and Kata coaching.
Our client is a leading provider of secure products and services, operating across 24 global locations with a workforce of 3,230 employees. One of their key manufacturing sites, responsible for producing a significant portion of the company’s output, had been facing issues with problem-solving. Despite having an in-house Operational Excellence framework that delivered several improvements over three years, the site struggled with a lack of a defined approach to problem-solving, leading to recurring issues and inefficiencies.
The primary challenge was the absence of a standardised methodology for problem-solving, resulting in shallow solutions such as firefighting and troubleshooting rather than addressing root causes. This lack of a systematic approach led to repeat occurrences of problems and impacted quality and cost metrics. Additionally, there was no leadership coaching capability in place to support problem management. Approaches to problem-solving were more directive than questioning, leading to a lack of learning and understanding.
To address these challenges, Project7 engaged with the site’s leadership team to develop and integrate a practical problem-solving system and methodology. This involved “Improvement Kata” coaching to help the management team define and improve their approach while developing their teams’ capabilities.
The implementation was divided into three phases:
- Phase 1: Problem Management We determined the management team’s role in site problem-solving and identified nine staff members for training in a Nine Step Problem Solving methodology. A site problem management system was introduced to govern the approach and ensure process confirmation.
- Phase 2: Kata-based Gemba The team was trained and coached in Kata coaching and Improvement Kata, leading to the implementation of these methodologies in the print area. This helped develop critical thinking and was incorporated into a Kata-based morning Gemba walk.
- Phase 3: Learning Through Experimentation The Kata routine coaching plan was further developed to include observations of the management team’s onsite coaching and feedback. We introduced a go-look-see methodology as part of problem-solving, which led to the development of a Kata-based A3 methodology for applying experimentation to improvement projects.
The impact of these new approaches on the facility’s performance was significant. The site achieved £5.3 million in savings through the implementation of the Nine Step problem-solving and Kata coaching.
Examples of these savings include inventory reduction, polymer spoil reduction, ink utilisation, and polymer BPS model adaptation. Additionally, the site realised £1.1 million in cost avoidance through the same methodologies, including mitigation of polymer spoilage and cut registration issues.
This project demonstrated the profound impact that a structured and systematic approach to problem-solving can have on an organisation. By fostering a problem-solving mindset and developing leadership coaching capabilities, the client was able to achieve substantial improvements in performance and efficiency.
At Project7 Consultancy, we remain dedicated to helping our clients achieve their goals through targeted performance improvements and leadership development. Our work on this project underscores the value of practical problem-solving and Kata coaching in driving continuous improvement and achieving lasting results.
Please contact us for more information on how we can assist your organisation in achieving similar success.