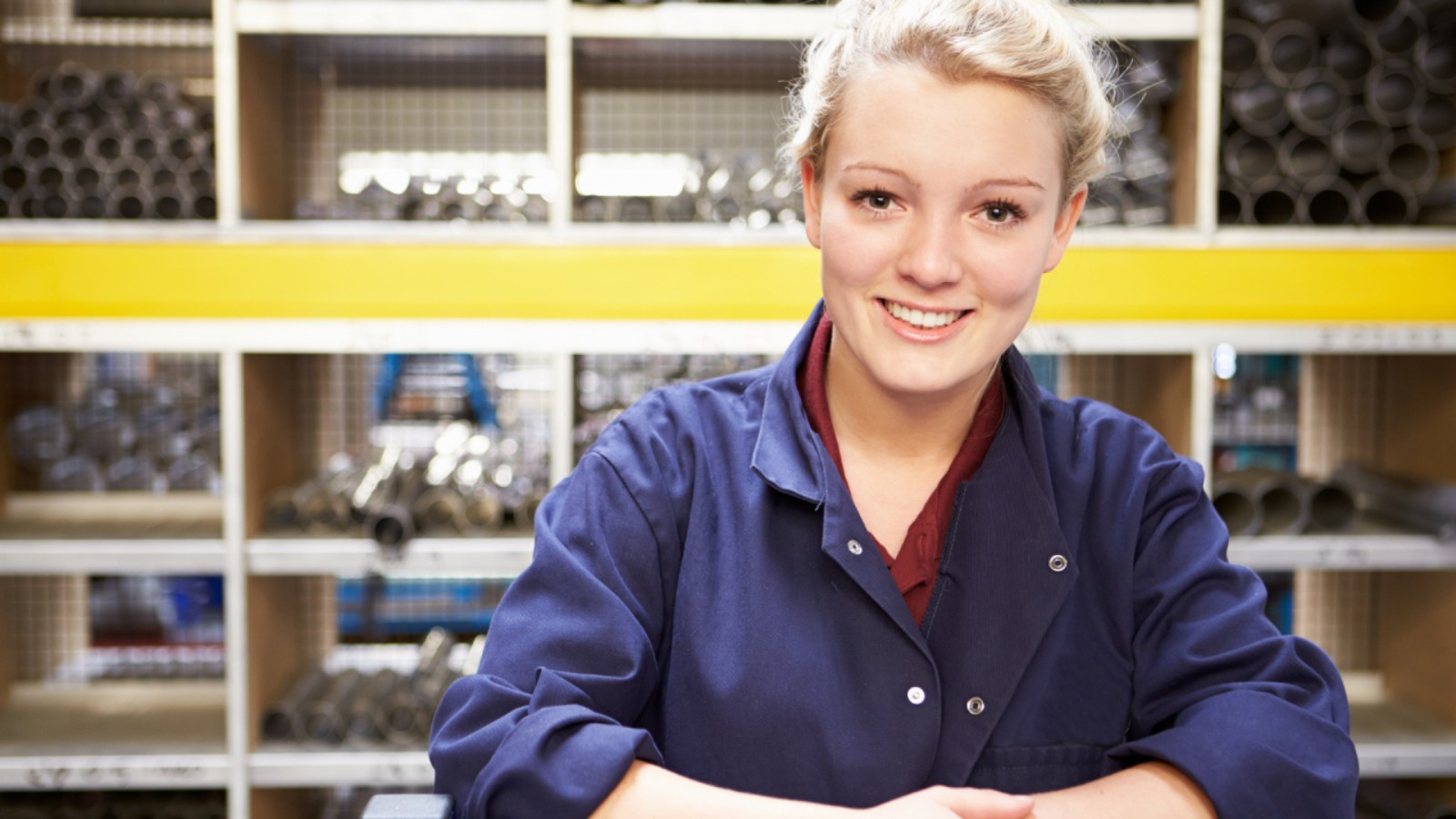
Working closely with storeroom and purchasing leadership is essential to determine asset criticality and managing spare parts inventory. The goal is to maintain high OEE through availability and optimum process speed while minimising inventory value. Often, excess inventory ties up capital while critical components are lacking.
Here are effective strategies to build a robust critical asset and inventory management process:
Conduct an Asset Criticality Assessment
- Identify assets with the greatest impact on production and maintenance costs. Consider factors like function, process criticality, failure history and failure impact.
- Assign a criticality ranking to each asset:
- Criticality 1 – Shuts down entire plant or multiple lines
- Criticality 2 – Shuts down one line
- Criticality 3 – Slows production
- Focus time, effort and money where it will achieve the best ROI.
Perform Failure Mode Analysis
- Do Failure Mode and Effects Analysis (FMEA) on critical assets. Identify potential failure modes, causes and consequences.
- Prioritise assets based on failure severity and likelihood.
- Alternatively, leverage existing failure data to build a Failure Reporting and Criticality Analysis (FRACAS) database. FRACAS supports proactive failure management, reducing downtime and costs.
Analyse Reliability Data
- Analyse historical maintenance data and reliability metrics like MTBF, MTTR.
- Identify failure patterns and critical spares for frequently failing or long lead time components.
Classify Spare Parts
- Categorise spare parts as critical, essential or non-critical:
- Critical – Required to restore asset/line functionality promptly
- Essential – Necessary but may have longer lead times
- Non-critical – Readily available or minimal production impact
Evaluate Spare Part Availability
- Consider availability, lead time, supplier reliability and cost for each critical spare.
- Prioritise spares with higher failure probability or long lead times.
Optimise Inventory Levels
- Determine appropriate stock levels based on asset criticality, failure rates and lead times.
- Implement inventory techniques like JIT and min/max to balance availability and excess inventory.
Build Supplier Relationships
- Foster supplier relationships and service agreements to enable prompt delivery of critical spares.
Continuously Review and Optimise
- Regularly review assets, inventory and strategy based on updated data and operational changes.
- Continually align maintenance strategy to business needs.
Set Minimum and Maximum Levels
To establish component min/max levels:
- Analyse historical usage, lead times and failure data. Understand consumption rate, frequency and lead times.
- Calculate reorder point (ROP) based on lead time demand and safety stock to account for uncertainties.
- Set minimum level above ROP to avoid stockouts before replenishment.
- Determine maximum level based on storage space, costs of excess inventory and other factors.
- Prioritise levels based on component criticality.
- Optimise using techniques like EOQ, JIT and MRP.
- Maintain inventory accuracy through disciplined removal tracking.
- Continuously monitor, review and adjust levels based on changing requirements.
The criticality of assets and required spares evolves over time. Maintain ongoing evaluation and adjustment to align your strategy with business needs. Setting stock levels is an iterative process requiring discipline, data analysis and refinement based on circumstances.