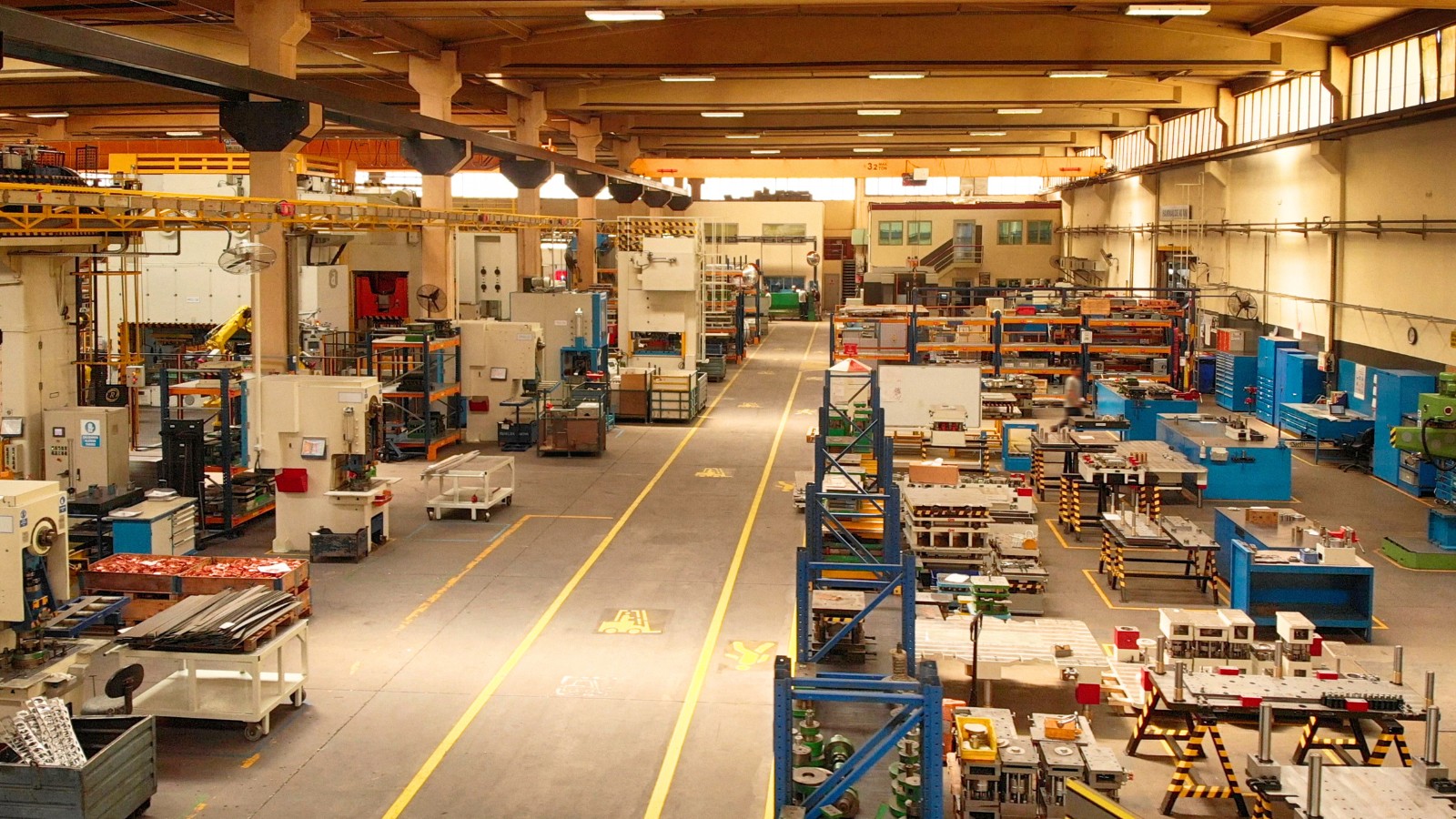
For Lean practitioners, sustaining change is one of the most challenging aspects of any implementation. This is especially true for 5S, a foundational tool in Lean methodology. Despite its widespread use over more than 50 years, many organisations struggle to sustain 5S initiatives. Studies and real-world experiences show that a significant proportion of Lean implementations fail to achieve long-term impact.
This article explores the relevance, value, and sustainability of 5S, offering practical insights for organisations seeking to achieve long-lasting success.
The Origins and Purpose of 5S
5S began as a method for workplace organisation and improvement. It is based on five steps: Sort, Set in Order, Shine, Standardise, and Sustain. These steps aim to create a clean, organised, and efficient work environment. Over time, 5S has become a core component of Lean methodology, helping businesses reduce waste, improve safety, and boost productivity.
While initially developed for manufacturing, 5S has proven its effectiveness across industries, from healthcare and education to service sectors and logistics. Its flexibility makes it a valuable tool for any organisation looking to enhance operational efficiency and foster a culture of continuous improvement.
The Five Steps of 5S
Sort
The first step focuses on removing unnecessary items from the workspace. By decluttering and prioritising essential tools and materials, organisations improve efficiency and reduce errors. Employees work more effectively in a streamlined environment where they can quickly access what they need without distractions.
Set in Order
This step involves organising items in a way that optimises accessibility. Using visual cues like shadow boards, labels, and colour coding helps employees quickly locate tools and materials, saving time and reducing wasted effort. A well-organised workspace promotes smoother workflows and reduces the likelihood of mistakes.
Shine
Cleanliness goes beyond aesthetics—it directly impacts safety, morale, and productivity. A clean environment reduces hazards, improves employee well-being, and reflects pride in the workplace. Regular cleaning also enables employees to identify potential maintenance issues before they escalate.
Standardise
Standardisation creates consistency across processes, ensuring that tasks are performed the same way every time. Clear standards and procedures reduce variability, improve quality, and establish a baseline for ongoing improvements. By making expectations explicit, organisations can eliminate ambiguity and enhance accountability.
Sustain
The final step is the most difficult to maintain over time. Sustaining 5S requires leadership commitment, cultural alignment, and employee engagement. Without these elements, the initial gains from 5S can quickly erode, leaving organisations to repeat the cycle of change without achieving lasting impact.
Key Challenges in Sustaining 5S
- Leadership Commitment
Leadership is the cornerstone of sustaining 5S. When leaders actively support and model 5S principles, they reinforce its importance and set the tone for the entire organisation. However, without visible and consistent commitment from leadership, employees may view 5S as a temporary initiative rather than an enduring practice. - Cultural Alignment
Successful 5S implementation requires aligning the methodology with the organisation’s existing culture and values. Organisations that attempt to replicate another company’s approach without adapting it to their unique environment often struggle to sustain results. A culture that embraces continuous improvement is essential for embedding 5S into daily operations. - Employee Engagement
Employees are the driving force behind 5S. If they are not involved in planning and implementation, they may see 5S as an imposed process rather than an opportunity for improvement. Engaging employees through training, feedback, and recognition is key to fostering ownership and commitment. - Ongoing Monitoring
Sustaining 5S requires regular reviews and audits to ensure adherence and identify areas for improvement. Without continuous monitoring, initial progress can fade as old habits resurface. Clear accountability and consistent follow-up are essential for maintaining momentum.
The Benefits of 5S
- Improved Efficiency
By organising the workspace and eliminating unnecessary items, 5S reduces the time employees spend searching for tools and materials. This streamlined approach improves workflow and ensures resources are used effectively. - Enhanced Safety
A clean and organised environment reduces the risk of accidents and injuries. Employees are more likely to notice hazards and take proactive steps to address them when cleanliness is part of the daily routine. - Cost Savings
5S eliminates waste, reduces inventory levels, and optimises resource utilisation. These efficiencies translate into tangible cost savings, making 5S a financially beneficial initiative for organisations of all sizes. - Increased Employee Morale
A well-maintained workplace fosters a sense of pride and ownership among employees. When employees feel valued and empowered to contribute to improvements, they are more engaged and motivated. - Consistency and Quality
Standardised processes lead to greater consistency in outcomes. Employees know what to expect and how to perform their tasks, resulting in higher-quality products and services.
Practical Tips for Sustaining 5S
- Make Leadership Visible
Leaders should actively participate in 5S activities, from conducting audits to celebrating successes. Their involvement signals that 5S is a priority and encourages employees to take it seriously. - Involve Employees from the Start
Engage employees in every stage of the process, from identifying improvements to developing standardised procedures. Their insights and buy-in are crucial for long-term success. - Train and Support Teams
Provide training that equips employees with the knowledge and skills needed to implement and sustain 5S. Offer ongoing support to address challenges and reinforce best practices. - Monitor and Adapt
Regularly review progress and make adjustments as needed. Use visual management tools to track activities and hold teams accountable for maintaining standards. - Celebrate Achievements
Recognise and reward teams for their efforts. Highlighting the positive impact of 5S fosters motivation and reinforces the value of the initiative.
Wrapping Up
5S is more than just a tool for workplace organisation—it is a powerful driver of efficiency, safety, and employee engagement. However, its long-term success depends on how well it is embedded into the organisation’s culture and daily practices. Leadership commitment, cultural alignment, and employee involvement are essential for sustaining 5S and achieving lasting improvements.
When implemented and maintained effectively, 5S delivers measurable benefits, from reduced waste and improved safety to enhanced productivity and morale. By treating 5S as a cultural shift rather than a one-time initiative, organisations can unlock its full potential and create a foundation for continuous improvement.
Through thoughtful planning, active participation, and consistent monitoring, 5S can transform the way organisations operate, driving both immediate and long-term success. For businesses committed to operational excellence, 5S remains a vital tool for achieving sustainable growth and performance.