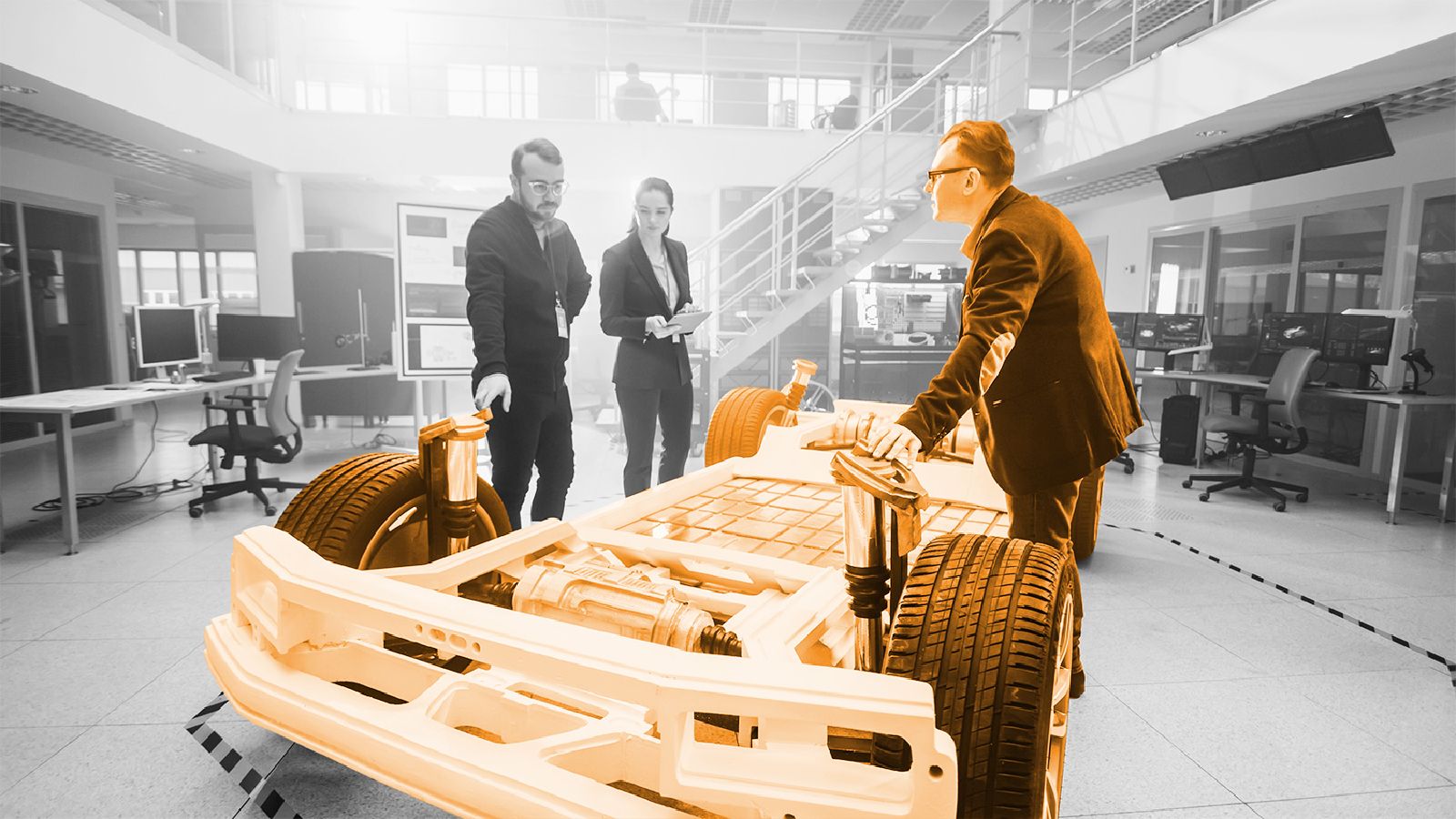
The long-standing criticism of the Construction industry for its poor productivity levels, high cost of rework and its command and control approach to job site coordination and planning has unfortunately remained consistent over the years. At the turn of the century, Sir John Egan published ‘Rethinking Construction’ highlighting the urgent need to address spiralling Construction costs, schedules, and defects. Several high profile reports have since reiterated this criticism, most notably the McKinsey Productivity Imperative
Report, and yet, the data suggests that little has changed.
A recent international study indicates that the measured direct costs of avoidable errors are in the order of 5% of the project value. If you overlay these poor performance factors against an industry in the UK with average profit levels of just 3%, this highlights the immediate and pressing case for change.
In this article, I will offer our insight into how other progressive companies have addressed their own productivity imperative and share views on what measures Construction companies can take to begin the journey to a high-performance culture.
Many automotive manufacturing organisations have successfully tackled the problem of poor productivity, quality, and reliability. Most notably perhaps being Toyota, who following World War 2 stood on the verge of bankruptcy and, from a small island nation with little to no natural resources of which to speak, managed
to outperform their European & American competitors year after year.
Toyota developed a systematic approach to waste elimination within their operating system (known as the Toyota Production System TPS) to improve their products’ productivity, safety, and quality.
Toyota has an innate sense of Respect for People and resources and has habitually adopted the scientific method for solving problems which have rightly led to the plaudits they have received todate. They implicitly apply their universally agreed principles and demonstrate an almost symbiotic relationship between people and processes.
This inner coding is why many western organisations who have merely tried to replicate the Toyota set of tools fail to reproduce similar results. Toyota emphasises the importance of optimising workflow through relentless daily improvements and increasing the value of production by making only “what is needed, when it is needed, and in the amount needed.”
Toyota developed a systematic approach to waste elimination within their operating system (known as the Toyota Production System TPS) to improve their products’ productivity, safety, and quality.
Toyota has an innate sense of Respect for People and resources and has habitually adopted the scientific method for solving problems which have rightly led to the plaudits they have received todate. They implicitly apply their universally agreed principles and demonstrate an almost symbiotic relationship between people and processes.
This inner coding is why many western organisations who have merely tried to replicate the Toyota set of tools fail to reproduce similar results. Toyota emphasises the importance of optimising workflow through relentless daily improvements and increasing the value of production by making only “what is needed, when it is needed, and in the amount needed.”
To put this into context, in 1984, each employee of Toyota Motor Company raised and delivered on average 45 improvement ideas.
How does this statistic compare to your Company?
Most companies don’t even ask this of their employees, never mind measure it or have a system or culture to empower this way of thinking.
Whilst recognising that the characteristics of the Construction industry are particularly unique compared to manufacturing, however, there are distinctive features that allow Lean thinking to transfer across industries, including a controllable production (trade) flow, repeatable processes and most importantly, Waste. The correct application of Lean thinking would go a long way to address Construction’s critical productivity challenges.
The introduction of Lean into Construction is not necessarily a new concept. The industry has made several attempts to eliminate Waste and replicate Toyota’s achievements with the implementation of Lean Construction over the last two decades with only limited success. Admittedly there are pockets
of ‘good practice’, but systemically the industry has failed to grasp the point of embracing Lean as an organisational thinking way, which has led many Construction Leaders to falsely assume that
“we are special in Construction, therefore Lean doesn’t work in our industry.”
So why hasn’t the ‘silver bullet’ that is Lean, not worked as many people thought it would? And what do Construction companies need to do differently?
Put Strategy into Action
Organisations are often excellent at developing ambitious strategies designed to tackle their most significant challenges, but they regularly fail to achieve the desired results. This failure is usually caused by the company’s strategic direction not effectively cascading down throughout the organisation and failing to connect with the business’s value-adding contingent. Successful organisations harness the effort of their entire enterprise to create positive outcomes greater than the sum of its parts.
Stop Paying Lip Service to Lean Transformation
In our experience, we see organisations hiring Lean ‘practitioners’ without the necessary practical experience of leading transformational change. Yet, they expect to yield the associated benefits of a high-performing progressive organisation. Simply because you have implemented 5S or collaborative planning doesn’t necessarily suggest A) you are a Lean Organisation or B) doing it very well. First and foremost, Lean is a thinking way that creates a healthy dissatisfaction with the current state and requires Leadership buy in to champion the entire organisation to relentlessly improve every day.
Address the Waste you can Control
The Construction industry has suffered from poor productivity and performance for decades. Whilst acknowledging that external factors such as COVID-19 and Brexit have caused enormous uncertainty and disruption to Construction Projects, laying the blame solely at the door of these generational anomalies fails to recognise the immense opportunity of the waste businesses can eliminate for themselves. Much like post-war ravaged Toyota, which teetered on the edge of bankruptcy and suffered from bomb-damaged factories, it still managed to navigate significant geopolitical circumstances to outperform its competitors year after year
By its very definition, Continuous Improvement is defined as a never-ending journey towards perfection in everything you do. Therefore, can organisations ever class themselves as ‘Lean’ or deem themselves as successfully solving the efficiency paradox? In my experience, genuinely progressive companies are incredibly humble, and in the spirit of Continuous Improvement,
they continually seek the next improvement to the standard. Changing an industry can take a long time. However, Construction firms can begin to set the precedence for high performance and seriously address the sector’s challenges by embedding the cultural enablers and operating system at an enterprise-level aligned to a Lean thinking way to improve safety, quality, and delivery performance.