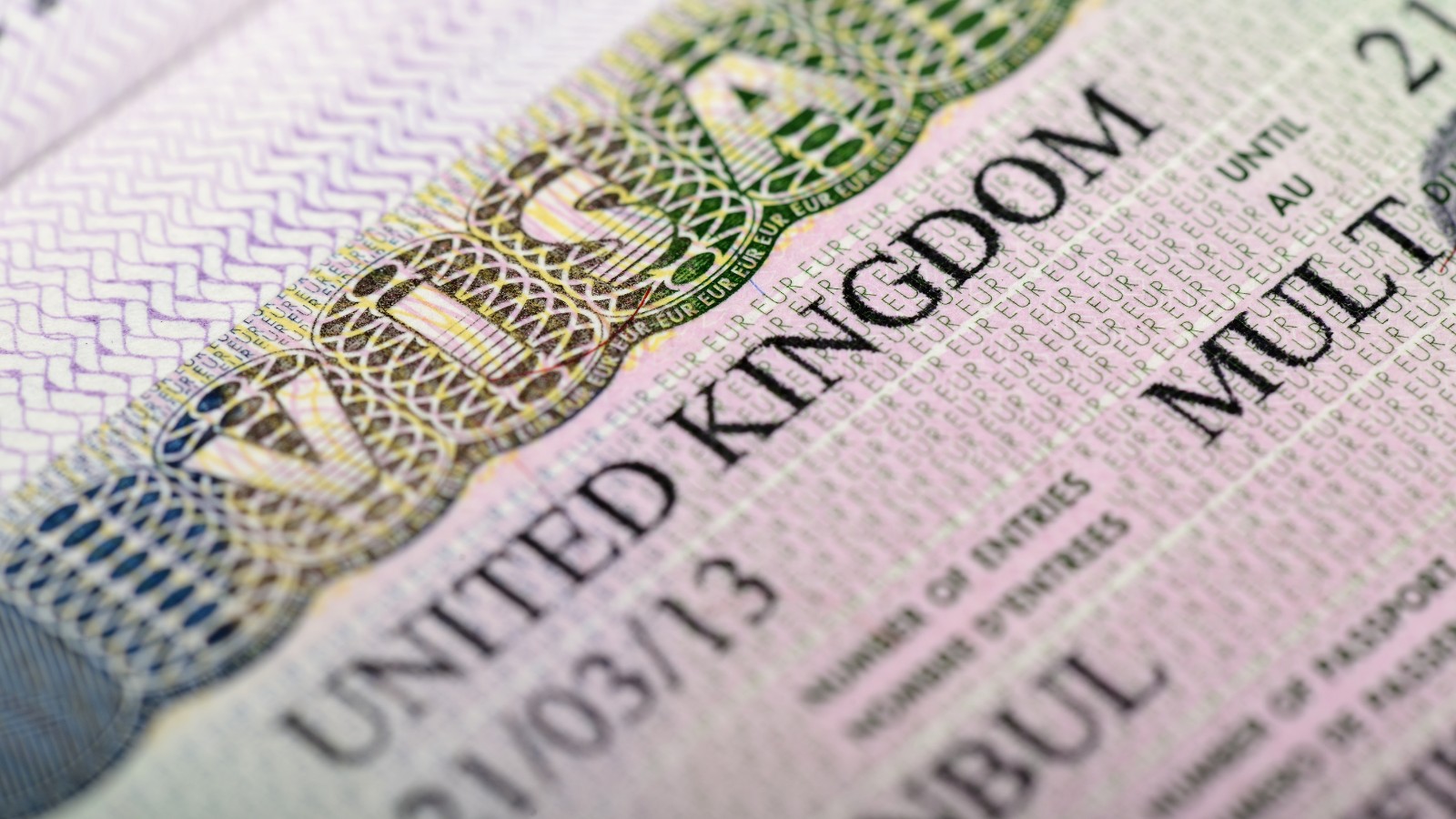
One of the major outcomes of a Project7 engagement is to empower organisations with the tools and methodologies needed for continuous improvement. One of our significant previous projects involved enhancing the problem-solving capabilities of a major manufacturing facility. This reflection explores the challenges faced, solutions implemented, and the impactful outcomes achieved through practical problem-solving and Kata coaching.
Our client is a leading provider of secure products and services, operating across 24 global locations with a workforce of 3,230 employees. One of their key manufacturing sites, responsible for producing a significant portion of the company’s output, had been facing issues with problem-solving. Despite having an in-house Operational Excellence framework that delivered several improvements over three years, the site struggled with a lack of a defined approach to problem-solving, leading to recurring issues and inefficiencies.
The primary challenge was the absence of a standardised methodology for problem-solving, resulting in shallow solutions such as firefighting and troubleshooting rather than addressing root causes. This lack of a systematic approach led to repeat occurrences of problems and impacted quality and cost metrics. Additionally, there was no leadership coaching capability in place to support problem management. Approaches to problem-solving were more directive than questioning, leading to a lack of learning and understanding.
To address these challenges, Project7 engaged with the site’s leadership team to develop and integrate a practical problem-solving system and methodology. This involved “Improvement Kata” coaching to help the management team define and improve their approach while developing their teams’ capabilities.
The implementation was divided into three phases:
- Phase 1: Problem Management We determined the management team’s role in site problem-solving and identified nine staff members for training in a Nine Step Problem Solving methodology. A site problem management system was introduced to govern the approach and ensure process confirmation.
- Phase 2: Kata-based Gemba The team was trained and coached in Kata coaching and Improvement Kata, leading to the implementation of these methodologies in the print area. This helped develop critical thinking and was incorporated into a Kata-based morning Gemba walk.
- Phase 3: Learning Through Experimentation The Kata routine coaching plan was further developed to include observations of the management team’s onsite coaching and feedback. We introduced a go-look-see methodology as part of problem-solving, which led to the development of a Kata-based A3 methodology for applying experimentation to improvement projects.
The impact of these new approaches on the facility’s performance was significant. The site achieved £5.3 million in savings through the implementation of the Nine Step problem-solving and Kata coaching.
Examples of these savings include inventory reduction, polymer spoil reduction, ink utilisation, and polymer BPS model adaptation. Additionally, the site realised £1.1 million in cost avoidance through the same methodologies, including mitigation of polymer spoilage and cut registration issues.
This project demonstrated the profound impact that a structured and systematic approach to problem-solving can have on an organisation. By fostering a problem-solving mindset and developing leadership coaching capabilities, the client was able to achieve substantial improvements in performance and efficiency.
At Project7 Consultancy, we remain dedicated to helping our clients achieve their goals through targeted performance improvements and leadership development. Our work on this project underscores the value of practical problem-solving and Kata coaching in driving continuous improvement and achieving lasting results.
Please contact us for more information on how we can assist your organisation in achieving similar success.