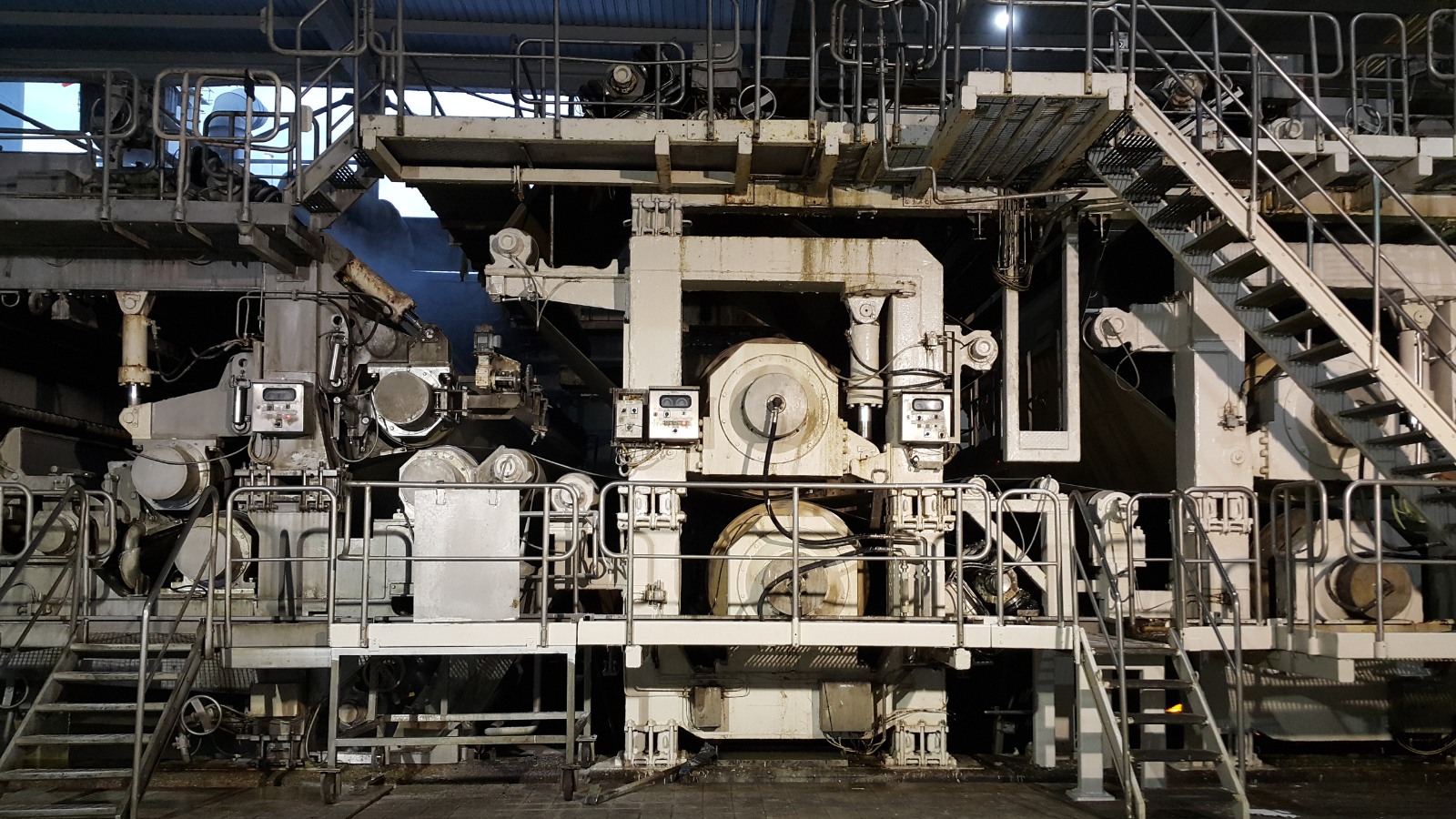
Solving persistent operational issues requires a structured, data-driven approach. In one of our previous projects, we tackled a long-standing issue with a Hydra-Purge system at a paper production facility. The system had consistently been blanking over during maximum production, particularly when handling heavier paper grades, severely affecting throughput. Despite efforts to resolve it, the root cause had remained undetected for over five years.
Operations initially believed the problem lay with incorrect settings between the extraction plate and the impeller. At maximum capacity, the Hydra-Purge would stop functioning, causing pulp flow to drop to zero. Using Six Sigma DMAIC principles, we took a data-led approach to investigate and identify the root cause.
When operations inspected the system during the next occurrence of zero flow, they found it clean, ruling out the original assumption of blanking over. This prompted a deeper analysis of the process. We assembled a team, including the Plant Chief Engineer, the Hydra-Purge OEM, the process engineer, the Operations Manager, and the wet-end operator, to review the data.
On further examination, we discovered that the feed to the Hydra-Purge was being starved during maximum production. The issue was traced to a weir plate that hadn’t been cut low enough, restricting the pulp flow from the pulper to the Hydra-Purge at peak demand.
The solution was straightforward: lower the weir plate to allow sufficient pulp flow. This low-cost modification resolved the problem after more than five years of production issues.
The impact was immediate. The problem was solved in just three days, throughput improved instantly, and the modification boosted production to record levels, adding the equivalent of an extra shift of production time per month.
This project demonstrates the power of focused leadership, data analysis, and collaboration. By questioning assumptions and thoroughly analysing process data, long-standing operational issues can be solved, unlocking new levels of performance.
For more information on how similar strategies can benefit your organisation, feel free to reach out to us.