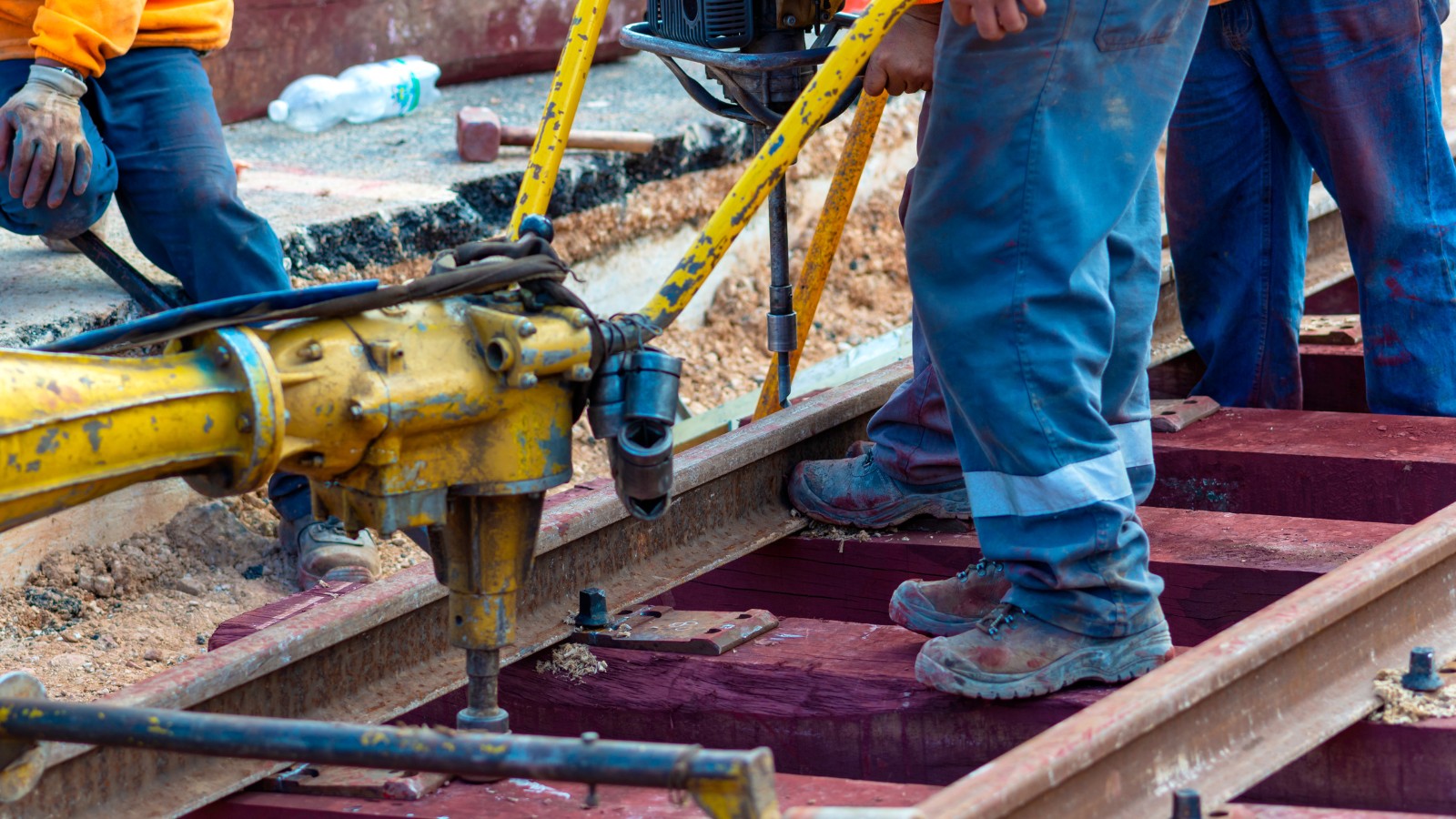
We continuously strive to help organisations achieve operational excellence through targeted performance improvements. One of our significant and most memorable projects was with one of the UK’s largest rail infrastructure providers. In this article we’ll explore the challenges, solutions, and outcomes of this project focused on standardised working within rail maintenance.
Our client manages the infrastructure for most of the rail network across England, Scotland, and Wales, and employs approximately 35,000 individuals across various disciplines.
Operating under the control of the UK government, the organisation is tasked with ensuring the safe and efficient operation of the nation’s railways. However, the maintenance procedures for repairing defective tracks were found to be inconsistent due to variations in standard work practices among maintenance teams. These inconsistencies led to additional defects, rework, and negative impacts on quality and cost metrics.
Recognising these challenges, Project7 implemented a Standardised Work approach to enhance the consistency, efficiency, and quality of track maintenance. The project involved training a pilot team on the proficiency and usefulness of Standardised Work and Waste Analysis. We began by analysing the current performance of the delivery unit and linking key metrics to performance measures such as Safety, Quality, Cost, Delivery, and People (S.Q.C.D.P).
A critical part of the project was trialling the revised processes and documentation with team members. This included visually recording the maintenance activities to identify any waste and opportunities for quick change-overs using Single-Minute Exchange of Dies (SMED) principles. Additionally, we recommended redesigning the Point of Use materials and tooling storage to maximise kitting and process efficiency.
The primary aims of implementing Standardised Work were:
- Reducing process variation by adopting a ‘best practice approach’ for managing defective track repairs.
- Enhancing safety benefits.
- Ensuring the process was Trainable, Measurable, Improvable, Controllable, Repeatable, and Observable.
- Improving competence across maintenance teams.
- Enabling cyclic maintenance planning.
- Promoting compliance with industry standards.
- Facilitating continuous improvement.
The impact of these implementations was profound. Firstly, the cost avoidance achieved by identifying the over-processing of defective track repairs amounted to £540,000. This substantial saving underscores the financial benefits of standardising work practices.
Additionally, our analysis of data records revealed significant gaps in data entry. By recommending tighter governance, we improved data quality and achieved additional cost savings of £180,600. These improvements in data quality are critical for informed decision-making and ongoing performance management.
Perhaps one of the most remarkable outcomes was the 50% increase in productivity due to the elimination of waste. This productivity boost not only enhances the efficiency of maintenance operations but also contributes to overall organisational effectiveness.
Reflecting on this project, several key lessons emerge:
- Consistency is Key: Standardised work practices are essential for reducing variations and ensuring consistent quality and efficiency in operations.
- Training and Engagement: Engaging and training teams on new processes and waste analysis tools is critical for successful implementation and sustainability.
- Data Governance: Improving data quality through stringent governance practices is vital for accurate performance measurement and continuous improvement.
- Continuous Improvement: Adopting a mindset of continuous improvement allows organisations to adapt, refine, and enhance their processes over time.
Our partnership with our client demonstrates the significant impact that well-executed standardisation and process improvements can have on an organisation. By creating a safer, more efficient, and high-performing railway, we not only met but exceeded our client’s expectations.
At Project7 Consultancy, we remain committed to helping our clients achieve operational excellence through tailored solutions and strategic interventions. Please contact us for more information on how we can assist your organisation in achieving similar success. Together, we can drive positive change and deliver lasting benefits.