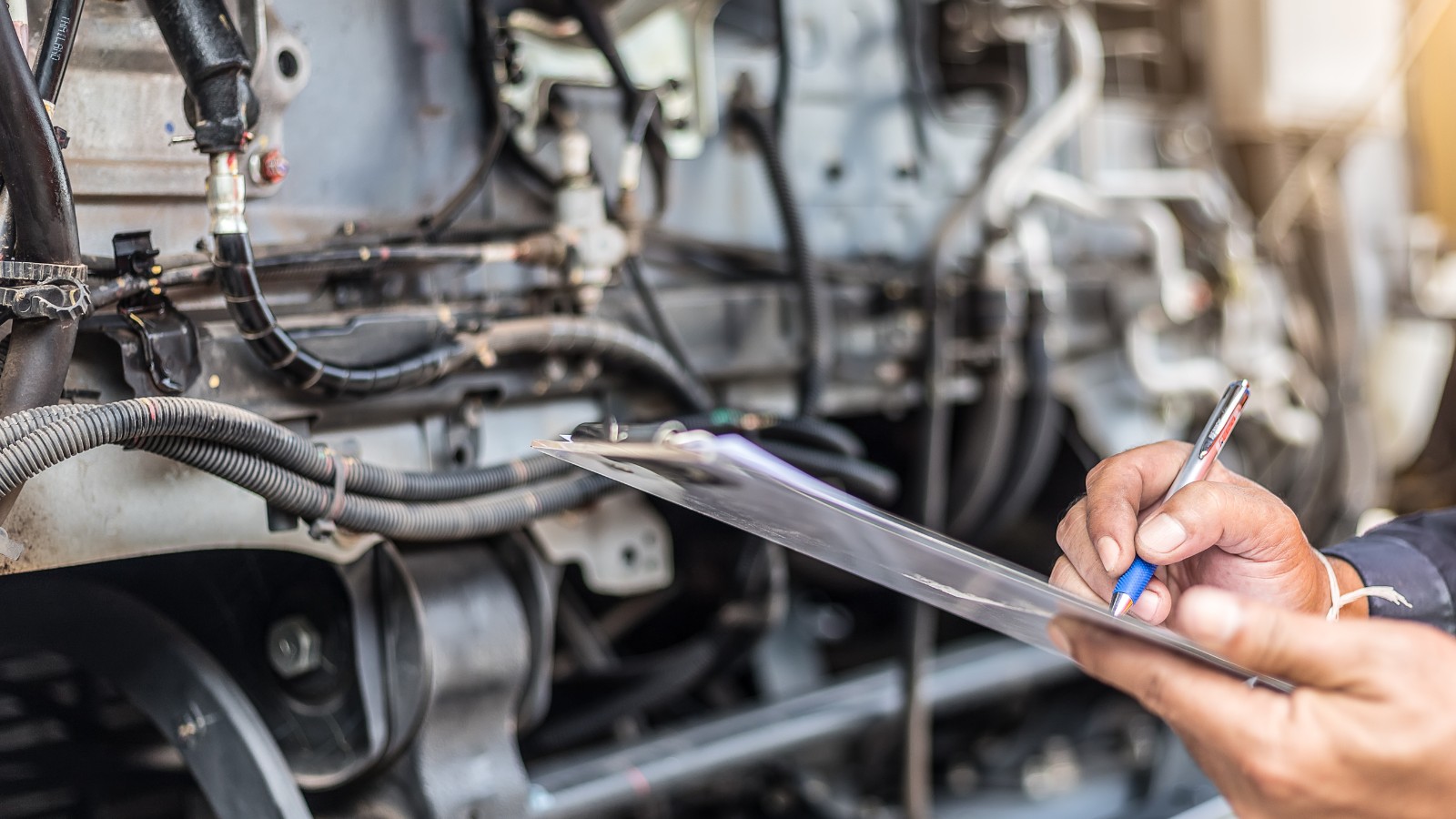
How Autonomous Maintenance Drives Overall Equipment Effectiveness
In the race to meet production targets, it’s easy to focus on speed, volume, and quality, but what happens when the very machines driving your success start to fall behind? Too often, equipment health is overlooked until an unexpected breakdown brings everything to a halt, jeopardising your bottom line. Imagine if your frontline operators could prevent these costly disruptions before they happen. Enter Autonomous Maintenance (AM)—a game-changing pillar of Total Productive Maintenance (TPM) that not only increases machine performance but also helps your workforce take control of the equipment they rely on. Implementing AM could be the key to uncovering hidden efficiencies and creating a culture of ownership on your shop floor, all while driving significant improvements in Overall Equipment Effectiveness (OEE)..
Defining OEE
OEE is a business improvement metric used to evaluate the efficiency of manufacturing processes. While it is widely used across industries—from automotive and aerospace to food production—it serves as a valuable tool for any business reliant on machinery.
OEE is calculated as:
OEE = % Target Speed x % Target Quantity x % Target First Quality
This metric compares actual performance against target performance, including deductions for maintenance and changeover times. It serves as a continuous improvement driver by highlighting areas of inefficiency. For example, a machine running at 95% of target speed, producing 88% of target quantity, with 90% first-pass quality would result in an actual OEE of just 75%. If the target OEE is 86%, this points to an 11% gap that can be addressed.
When speed, quantity, or quality suffers due to equipment issues, Autonomous Maintenance (AM) can be the key to recovering this lost efficiency, especially in industries where profit margins are tight.
What is Autonomous Maintenance (AM)?
Autonomous Maintenance enables frontline operators to take responsibility for the upkeep of their machines. Operators perform routine tasks such as cleaning, inspecting, lubricating, and making minor repairs. AM is often the first pillar of TPM implemented, as it is both low-cost and delivers quick results.
Why is AM important?
Operators work with their machines every day. They become familiar with the equipment’s behaviour and are often the first to notice when something is wrong. With the proper training, operators can identify and fix small issues before they escalate into major breakdowns. By implementing AM, companies reduce the need for emergency maintenance, cut downtime, and improve overall machine reliability.
The Benefits of AM in Driving OEE
Consider the example of a manufacturing plant with an OEE target of 86%. After implementing AM, the plant improves OEE by 6% almost immediately. This improvement is not just a one-time gain but continues over time as operators take proactive steps to keep machines running at their best.
Steps to Implement Autonomous Maintenance
- Set Clear Objectives and Expectations
Explain to your engineering, operations, and maintenance teams why AM is being implemented. This is key to gaining buy-in and ensuring that everyone understands how it will improve business operations and make jobs easier. - Initial Cleaning and Inspection
Teams should conduct an initial deep clean and inspection of all equipment. As they clean, they should inspect components, mark any potential problems with colour-coded tags (e.g., safety, electrical, mechanical issues), and ensure that existing work orders are addressed. This “clean to inspect” method helps teams identify and prioritise maintenance tasks. - Develop Routine Maintenance Checklists
Working together, operators and maintenance teams should create a checklist of routine cleaning, inspection, and lubrication tasks. This checklist should be built from preventive maintenance schedules and enhanced with operator insights. - Provide Operator Training
Operators need to be trained on how to perform basic maintenance tasks properly. Training should cover the correct use of tools (e.g., torque wrenches), selection of lubricants, and how to avoid issues like cross-contamination. This ensures that operators maintain the equipment safely and effectively, without turning them into maintenance technicians. - Implement Visual Management
Visual management boards should be set up to track AM activities. These boards allow teams to monitor tasks, ensuring they are completed on time and to standard. Regular supervisor checks help sustain AM practices and maintain equipment reliability. - Encourage Continuous Improvement
AM is not static. Operators and maintenance teams should meet regularly to review and improve AM processes. Feedback, collaboration, and daily Genba walks help drive continuous improvement and sustain gains.
Wrapping up
Autonomous Maintenance is a low-cost, high-impact approach to improving Overall Equipment Effectiveness (OEE). By training operators to take responsibility for the routine upkeep of their machines, businesses can reduce downtime, increase production efficiency, and improve product quality. AM not only enhances machine reliability but also fosters a culture of ownership and continuous improvement across the shop floor.
If you’re looking to drive OEE and improve your maintenance practices, Project7 Consultancy offers expert training in TPM and Autonomous Maintenance. Contact us to find out more.