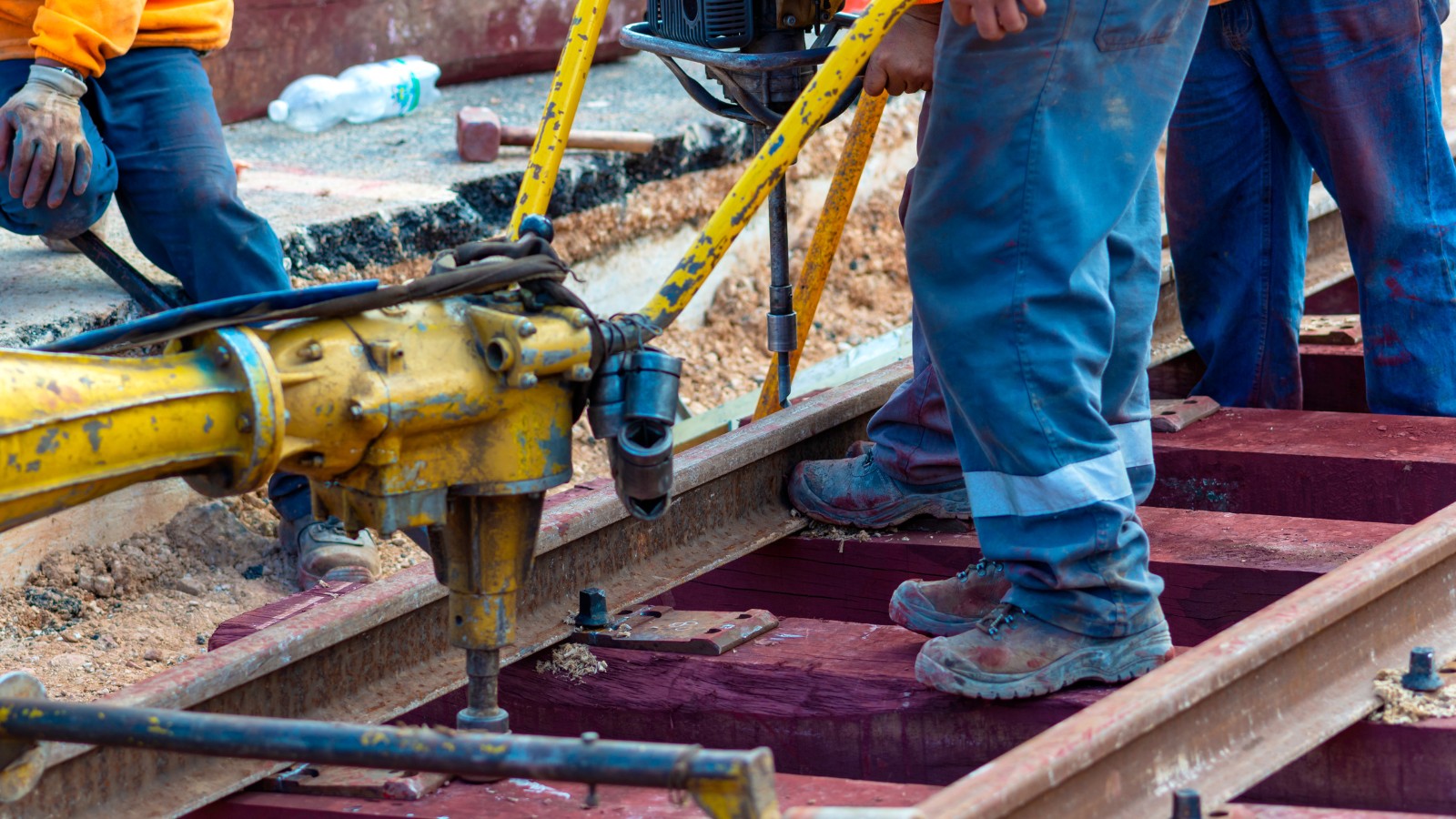
Reflection on Standardised Working in Rail
We continuously strive to help organisations achieve operational excellence through targeted performance improvements. One of our significant and most memorable projects was with one of the UK’s largest rail infrastructure providers. In this article we’ll explore the challenges, solutions, and outcomes of this project focused on standardised working within rail maintenance.
Our client manages the infrastructure for most of the rail network across England, Scotland, and Wales, and employs approximately 35,000 individuals across various disciplines.
Operating under the control of the UK government, the organisation is tasked with ensuring the safe and efficient operation of the nation’s railways. However, the maintenance procedures for repairing defective tracks were found to be inconsistent due to variations in standard work practices among maintenance teams. These inconsistencies led to additional defects, rework, and negative impacts on quality and cost metrics.
Recognising these challenges, Project7 implemented a Standardised Work approach to enhance the consistency, efficiency, and quality of track maintenance. The project involved training a pilot team on the proficiency and usefulness of Standardised Work and Waste Analysis. We began by analysing the current performance of the delivery unit and linking key metrics to performance measures such as Safety, Quality, Cost, Delivery, and People (S.Q.C.D.P).
A critical part of the project was trialling the revised processes and documentation with team members. This included visually recording the maintenance activities to identify any waste and opportunities for quick change-overs using Single-Minute Exchange of Dies (SMED) principles. Additionally, we recommended redesigning the Point of Use materials and tooling storage to maximise kitting and process efficiency.
The primary aims of implementing Standardised Work were:
- Reducing process variation by adopting a ‘best practice approach’ for managing defective track repairs.
- Enhancing safety benefits.
- Ensuring the process was Trainable, Measurable, Improvable, Controllable, Repeatable, and Observable.
- Improving competence across maintenance teams.
- Enabling cyclic maintenance planning.
- Promoting compliance with industry standards.
- Facilitating continuous improvement.
The impact of these implementations was profound. Firstly, the cost avoidance achieved by identifying the over-processing of defective track repairs amounted to £540,000. This substantial saving underscores the financial benefits of standardising work practices.
Additionally, our analysis of data records revealed significant gaps in data entry. By recommending tighter governance, we improved data quality and achieved additional cost savings of £180,600. These improvements in data quality are critical for informed decision-making and ongoing performance management.
Perhaps one of the most remarkable outcomes was the 50% increase in productivity due to the elimination of waste. This productivity boost not only enhances the efficiency of maintenance operations but also contributes to overall organisational effectiveness.
Reflecting on this project, several key lessons emerge:
- Consistency is Key: Standardised work practices are essential for reducing variations and ensuring consistent quality and efficiency in operations.
- Training and Engagement: Engaging and training teams on new processes and waste analysis tools is critical for successful implementation and sustainability.
- Data Governance: Improving data quality through stringent governance practices is vital for accurate performance measurement and continuous improvement.
- Continuous Improvement: Adopting a mindset of continuous improvement allows organisations to adapt, refine, and enhance their processes over time.
Our partnership with our client demonstrates the significant impact that well-executed standardisation and process improvements can have on an organisation. By creating a safer, more efficient, and high-performing railway, we not only met but exceeded our client’s expectations.
At Project7 Consultancy, we remain committed to helping our clients achieve operational excellence through tailored solutions and strategic interventions. Please contact us for more information on how we can assist your organisation in achieving similar success. Together, we can drive positive change and deliver lasting benefits.
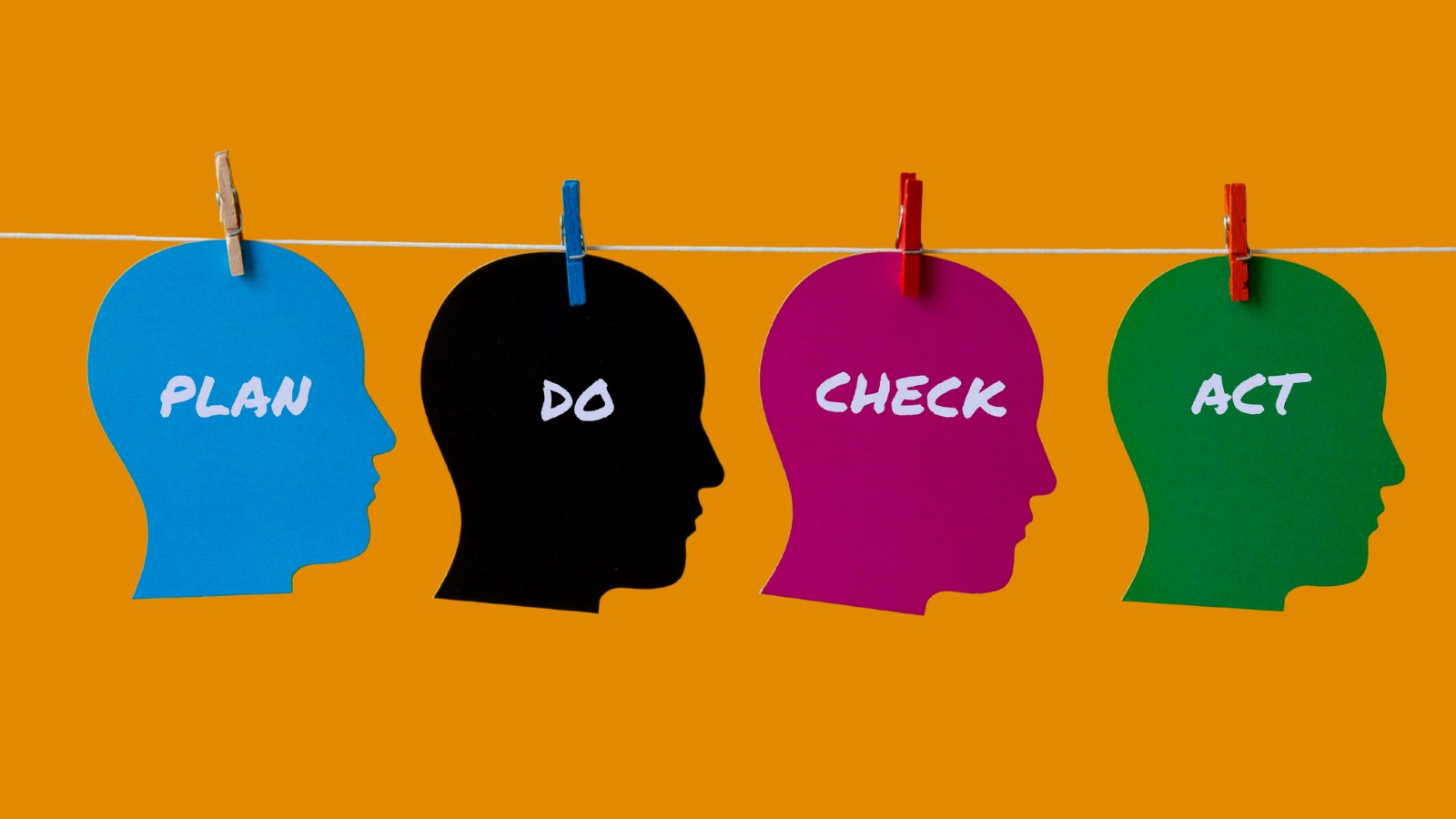
Lean Principles for the Service Industry
When speaking with leaders outside the manufacturing industry, one of the most common questions we encounter is: “How can Lean principles be effectively and sustainably integrated into service-based industries, where processes and outcomes are often more variable and less tangible than Lean’s origins in manufacturing?”
This question is challenging because Lean manufacturing principles, initially developed for the automotive industry and other manufacturing settings, rely heavily on the standardisation of processes, reduction of waste, and continuous improvement.
These principles are straightforward to apply in environments with repetitive, predictable processes and tangible outputs.
However, the variability, customer interaction, and intangible outputs typical of service industries (such as healthcare, finance, and hospitality) present unique challenges in adapting Lean methodologies.
Exploring how to customise and implement Lean principles in such environments while maintaining their effectiveness and sustainability is a critical area of ongoing research and practice. However, don’t let this deter you. We have seen Lean successfully applied in diverse areas, from running the London Underground, transporting human organs across the USA, organising care homes, optimising call centres, and reducing the time for end-of-month closing in a large corporate finance department.
We believe that Lean, when intelligently applied, will reduce waste in any process, develop a culture of continuous improvement, and delight both the customer and the shareholder or business owner.
Implementation Strategies
To address the challenge of integrating Lean principles into service-based industries effectively and sustainably, several strategies can be pursued:
- Customisation of Lean Tools and Techniques
Adaptation of Tools: Modify traditional Lean tools such as Value Stream Mapping (VSM), 5S, and Kaizen to fit service processes. For example, in healthcare, VSM can map patient flow through different departments, or in finance streamline supplier payments, or in hospitality speed up room cleaning and standardise hotel bedroom layouts. Don’t just replicate what manufacturing plants have done; adapt the core principles to be meaningful in your business.
Service-Specific Metrics: Develop metrics that capture service quality and customer satisfaction alongside efficiency and waste reduction. The key is to make the process and the metrics meaningful in driving your business.
2. Training and Education
Lean Education: Provide Lean training tailored to your employees so they understand not only the tools of Lean implementation but also why they are useful in driving your particular business. This way, they will see how the principles can solve their problems and improve their daily operations. In designing this training, engage with those who will own the new process to ensure you are solving real problems.
Cross-Industry Learning: Encourage learning from sectors where Lean has been successfully applied, such as Lean healthcare, to adapt best practices to your particular industry or need.
3. Cultural Change and Leadership
Leadership Commitment: Ensure strong leadership support for Lean initiatives. Leaders should champion Lean principles, become catalysts for change, and demonstrate commitment through actions. Without this commitment, sustaining a Lean programme in any industry is impossible. Find leaders at all levels who are passionate about Lean change as they will need this passion to drive change and transform cultures on what can be a difficult journey.
Employee Involvement: Foster a culture of continuous improvement where employees at all levels are rewarded and encouraged to identify inefficiencies and suggest improvements.
4. Pilot Projects and Iterative Improvement
Small-Scale Pilots: Start with pilot projects to test Lean principles in specific service areas. Use the lessons learned to refine and expand Lean initiatives.
Iterative Approach: Apply Lean iteratively, continuously assessing and refining processes based on feedback and performance data. Practice PDCA (Plan-Do-Check-Act) to constantly reflect on and refine your processes.
5. Customer-Centric Focus
Customer Feedback: Regularly gather and integrate customer feedback into your continuous improvement processes to ensure Lean improvements align with customer needs.
Customer Journey Mapping: Use customer journey mapping to identify pain points and opportunities for Lean improvements from the customer’s perspective. Too many organisations keep the customer ‘on the other side of the wall.’ This is an outdated behaviour based on protectionism and fear. Be transparent and ethical, which Industry 5.0 customers now rightly demand.
6. Technology and Automation
Digital Tools: Leverage digital tools and automation to streamline service processes and reduce variability.
Data Analytics: Use data analytics to gain insights into service performance and identify opportunities for Industry 4.0 integration to optimise areas for Lean improvements.
7. Collaboration and Knowledge Sharing
Industry Collaboration: Encourage collaboration between different service sectors and internal departments to share Lean success stories and challenges. Bring in people from other industries who have successfully engaged with Lean principles so that you do not have to ‘reinvent the wheel.’
Lean Communities: Participate in Lean communities and forums to exchange knowledge and experiences. Attend online and in-person Lean events from other industries to learn from them and adapt their experience to your needs.
If you require support to begin your Lean optimisation journey in the service industry, we invite you to get in touch. We offer a no-cost discussion to explore your opportunities and demonstrate how Project7 can assist in driving Lean implementation for your business.
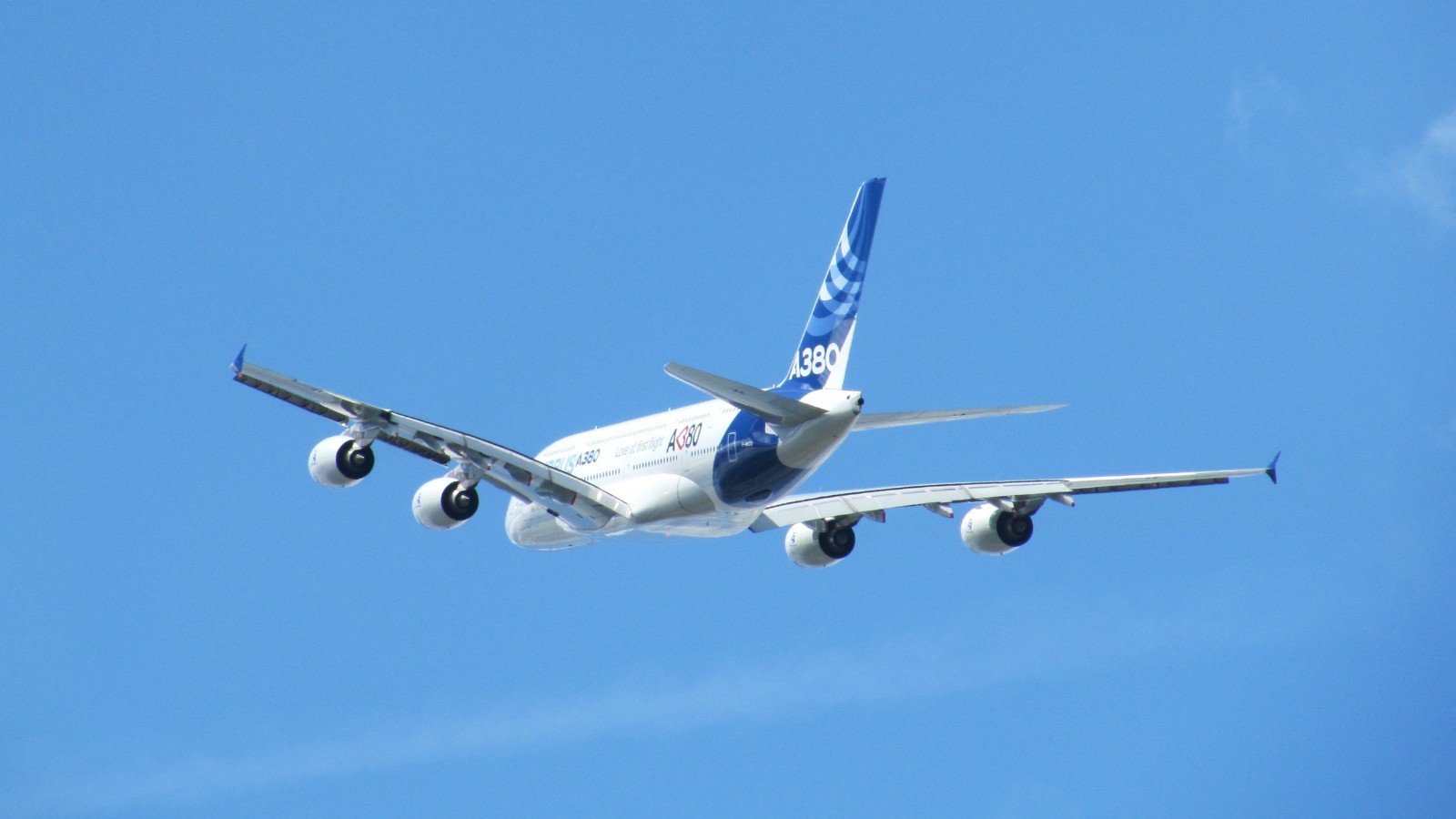
Reflecting on our Work for a Global Leader in Aircraft Manufacturing
At Project7 Consultancy, we have had the privilege of partnering with industry leaders to drive transformative change. One significant project involved a global leader in aircraft manufacturing. This reflection explores our journey with their US Final Assembly Line (FAL) in Alabama, highlighting the challenges faced, the solutions implemented, and the significant outcomes achieved.
At the Alabama facility, a new Final Assembly Line, was undergoing a critical transition from building two aircraft per month during its build phase to producing four aircraft per month as a fully operational assembly line.
This transition was compounded by the withdrawal of experienced European expats and the need to maintain production levels without significantly increasing the workforce.
The newly appointed General Manager recognised the need for a cultural shift towards a high-performance operating system to meet strategic goals of increasing US market growth and production volumes.
The key challenges at the Alabama facility included:
- Transitioning from experienced European employees to a new US workforce.
- Achieving a higher maturity level in their operating system, which was initially assessed at a D level with a target of A.
- Addressing employee engagement issues, as 60% of base-level employees rated leadership as either average or poor.
- Reduce the high levels of “travelled work,” where 40-50% of the planned workload was moved to subsequent workstations instead of being completed at one station.
These challenges highlighted the need for improved leadership, better material and workforce management, and the adoption of a systematic approach to assembly processes.
To address these challenges, Project7 was tasked with designing, implementing, and evaluating a world-class operating system across four levels of the Alabama organisation.
Our solution was based on the seven steps of the P7 Way, adapted to align with the company’s core principles:
- Strategy into Action
- Tiered Visual Performance Management (VPM)
- Short Interval Control & Performance Dialogues
- Performance Confirmation & Go Look See
- Setting Clear & Aligned Targets
- Problem-solving Level 1, Coaching for Success
- Problem-solving Level 2
- Talent Management and Leadership Development.
Additionally, we incorporated RACI Diagrams and ICOR Charts to clarify roles, tasks, and timelines, which facilitated significant breakthroughs in project success. By integrating these steps into the operating system, we aimed to create a high-performing culture that would enhance efficiency, reduce costs, and improve overall performance.
The implementation of the P7 Way and our tailored solutions led to substantial improvements at the US FAL:
- 40% reduction in travelled work, enabling the first-ever clean aircraft build within a workstation
- A significant positive shift in employee leadership survey results, moving from 60% negative ratings to 60% positive ratings
- Doubling production capacity from two to four aircraft per month, resulting in $2.4 billion in annual sales
- Increase in the operating system maturity assessment from D to B, with six categories moving to B and two to A.
These outcomes reflect the effectiveness of our approach in driving cultural and operational transformation. The success of this project not only met but exceeded the organisation’s strategic objectives, establishing a foundation for sustained high performance.
Reflecting on this project, several key lessons stand out:
- Implementing a world-class operating system requires a systematic approach that integrates leadership development, performance management, and continuous improvement.
- Building a high-performance culture involves engaging employees at all levels and fostering a sense of ownership and accountability.
- Adapting solutions to align with the client’s core principles and specific needs is critical for achieving desired outcomes.
- Ensuring thorough knowledge transfer and training for the local workforce is essential for sustaining improvements.
This project highlights the transformative impact that strategic interventions and a commitment to excellence can have on an organisation.
At Project7 Consultancy, we remain dedicated to helping our clients achieve their goals through targeted performance improvements and leadership development.
Please get in touch for more information on how Project7 Consultancy can help your organisation achieve similar results.
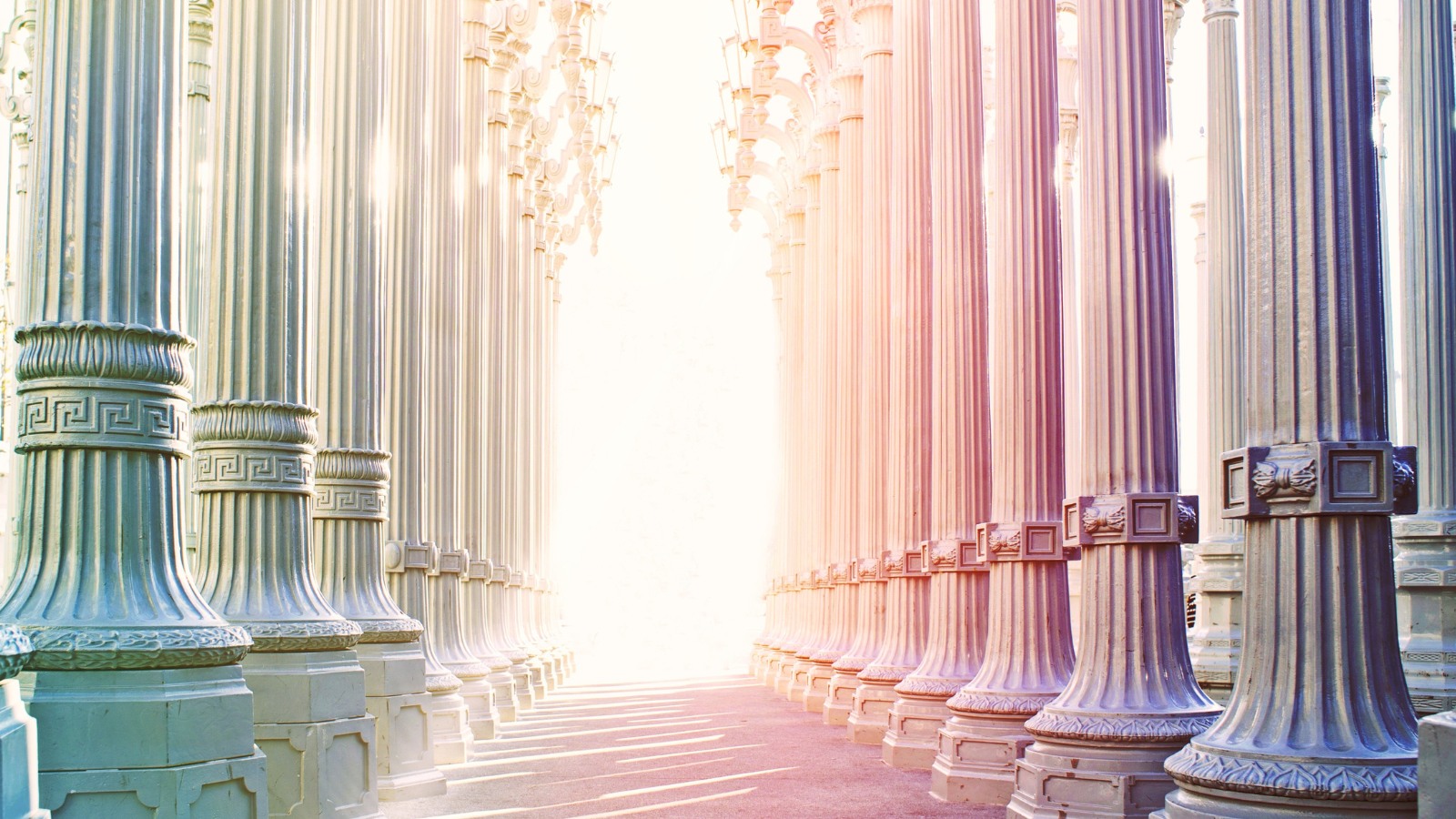
Addressing Common Misunderstandings for Effective Lean Leadership
Despite its widespread application and success across various industries, there are still many misunderstandings of Lean and Lean leadership. Here are eight common misunderstandings of Lean that we have found when working across industry, the service sector, and commerce.
- Focus on Tools Over Philosophy:
- Misunderstanding: Many believe Lean is primarily about implementing specific tools and techniques (like Kanban, 5S, or Kaizen).
- Reality: Lean is fundamentally a philosophy and mindset focused on continuous improvement and the reduction of waste. Tools are secondary to understanding and embodying principles that build a culture of Lean.
- Top-Down Implementation:
- Misunderstanding: Lean initiatives are often thought to be most effective when driven from the top down, with leaders dictating changes.
- Reality: While leadership support is critical, Lean thrives on engaging all employees, fostering a culture of bottom-up ideas and continuous improvement. When all are focused on Lean improvement, the entire business thrives. The role of leadership becomes the removal of obstacles so all can drive capability and capacity.
- Lean Equals Cost Cutting:
- Misunderstanding: Lean is frequently equated with cost reduction measures.
- Reality: This is still the overarching belief in many companies, but it is misguided. Lean aims to enhance value to the customer by eliminating waste, which can lead to cost savings, but the primary focus is on improving quality, efficiency, and employee satisfaction, not on reducing headcount.
- Lean is Only for Manufacturing:
- Misunderstanding: Lean principles are often seen as applicable only to manufacturing environments.
- Reality: Lean principles can be applied across various sectors, including finance, healthcare, software development, and service industries, wherever process improvement could be beneficial. We have seen Lean employed from improving the throughput in operating theatres to debt recovery, to cross-country transport of human organs for transplantation, to management of resources for care in the community.
- Immediate Results Expected:
- Misunderstanding: There is an expectation that Lean implementation will yield immediate and dramatic results.
- Reality: While the application of Lean can result in improvement in as little as one shift, Lean is a long-term commitment to a culture of continuous improvement. Significant results often take several years and demand sustained effort to materialise.
- Lean is a One-Time Project:
- Misunderstanding: Some view Lean as a project, a sort of ‘bolt-on’ with a defined beginning and end.
- Reality: Those who have been successful at Lean implementation know that Lean is an ongoing journey of continuous improvement to create a sustained cultural change. It requires persistent effort, regular assessment, and adaptation.
- Standardisation Stifles Creativity:
- Misunderstanding: Lean’s emphasis on standardisation and process control is thought to stifle creativity and innovation.
- Reality: Standardisation provides a stable foundation from which innovation and creativity can flourish. Standardisation eliminates chaos and frees up resources so each team member can focus on creative problem-solving and improvements.
- Lean Ignores People Development:
- Misunderstanding: Lean is sometimes seen as focusing solely on process improvement, neglecting the development of people.
- Reality: Lean leadership emphasises the essential input of people and invests heavily in training and empowering employees to solve problems and improve processes.
People + Process = Performance
Understanding these aspects will help leaders more effectively implement Lean principles and cultivate a culture of continuous improvement within their organisations.
If you would like to work through these misunderstandings and drive Lean processes in your organisation, then please get in touch.
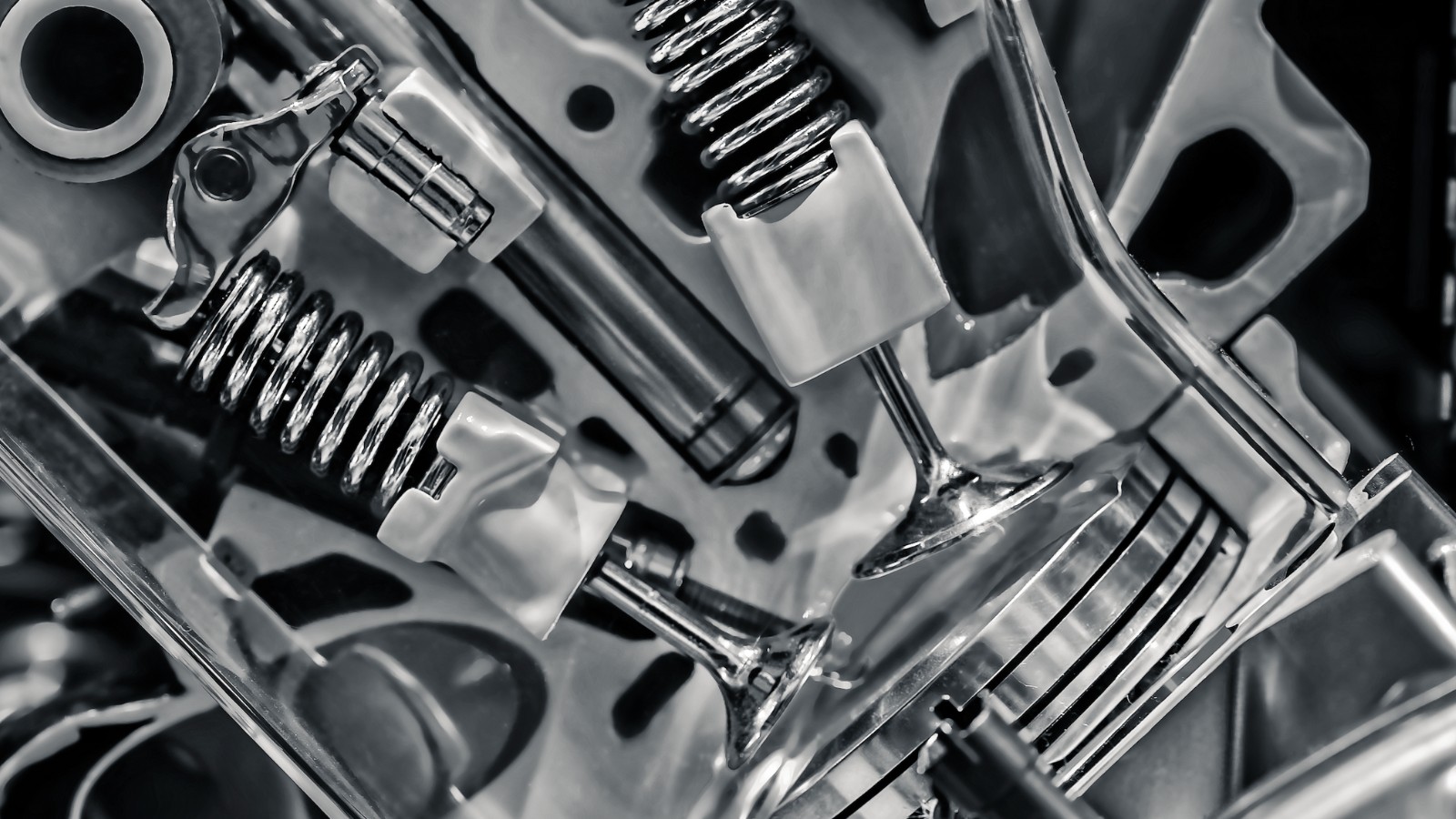
Reflecting on a Lean Plant Leadership Programme
Over the years, we have had the privilege of working with some of the world’s most respected organisations to drive significant performance improvements. One such project was our Lean Plant Leadership Programme (LP2) with a leading engine valve manufacturer in the automotive industry. This reflection explores the challenges faced, the solutions implemented, and the impactful results achieved through our collaboration.
Our client is a major manufacturer in the automotive industry, supplying engine valves to most car manufacturers globally. In recent years, the company faced increasing competition from low-cost manufacturers, coupled with rising scrap rates and high levels of finished product. This competitive pressure necessitated a reevaluation of their processes to boost performance and sustain long-term success.
The company engaged Project7 to help coach and integrate a Lean Leadership Programme to enhance productivity and equipment reliability.
Our approach was designed to create a leaner structure, mentality, and culture within the organisation, ultimately leading to improved performance and a more resilient company culture.
The primary challenge was the need for a clearly defined, standardised operating system across their plants. This inconsistency led to varied processes, systems, product quality, and delivery outputs, negatively impacting customer confidence. The company urgently needed access to lean tools and principles to establish a standard foundation for operational excellence across its engine components division.
Specifically, the intervention required:
- Creation of a standard foundation for operational excellence.
- Integration of effective engineering maintenance processes to improve asset management and equipment availability.
- Identification of the right processes and the right people to achieve sustainable performance output.
These objectives were to be achieved through a Back to Basics approach, focusing on core manufacturing business elements.
After a thorough assessment, Project7, along with our client, decided to create and deploy the Lean Plant Leadership Programme (LP2). This solution aimed to design, implement, and evaluate a world-class operating system that would be standardised and applied across 14 manufacturing sites globally.
The programme encompassed seven steps of the P7 Way:
- Strategy into Action (Policy Deployment)
- Tiered Visual Performance Management (TVPM)
- Short Interval Control & Performance Dialogues
- Process Confirmation & Go Look See
- Setting Clear & Aligned Targets; Problem-solving Level 1
- Coaching for Success; Problem-solving Level 2
- Talent Management and Leadership Development
These steps were adapted and implemented to create an Engine Components Operating System. Project7 worked closely with the executive team to define their needs clearly and focus on developing the organisation through lean techniques and best practices.
Within each site, a master schedule was created with local leadership teams to drive measurable activities against performance targets. Clear directional targets were established, and processes were created to guide the improvements.
Implementing LP2 led to significant improvements in business performance across all operations. Each site underwent a four-month implementation period based on our 3P approach, yielding impressive results:
- 31% Improvement in Overall Equipment Effectiveness
- 33% Improvement in Equipment Cycle Time (Bottleneck)
- 67% Reduction in Premium Freight
- 21% Reduction in Change Overtime, Hit to Hit
- 4% Reduction in Scrap
- 7% Reduction in Temporary Resource
- 11% Reduction in Overtime
- 21% Reduction in Finished Goods Inventory
- $24 Million Cost Avoidance in Capital Investment
The programme’s success extended beyond these metrics, creating a high-performing team culture and standardising operations across all 14 plants. Introducing tiered visual performance management, short interval control, and robust governance structures ensured sustained improvements and continuous knowledge transfer.
Lessons Learned and Future Outlook
Reflecting on this project, several key lessons emerge:
- Standardisation is Key: Establishing a standardised operating system across multiple sites is critical for consistent performance and quality.
- Lean Leadership: Integrating lean principles and leadership development fosters a culture of continuous improvement and accountability.
- Collaborative Approach: Close collaboration with the client’s executive team ensures the solutions are tailored to their specific needs and objectives.
- Sustainable Change: Focusing on both process improvements and cultural shifts ensures that the changes are sustainable in the long term.
The Lean Plant Leadership Programme demonstrated the profound impact that structured, strategic interventions can have on an organisation’s performance. By creating a leaner, more resilient structure and culture, our client not only enhanced its operational efficiency but also strengthened its competitive position in the market.
At Project7 Consultancy, we remain committed to helping organisations achieve their strategic goals through targeted performance improvements.
Please get in touch with us for more information on how Project7 Consultancy can help your organisation achieve similar results.
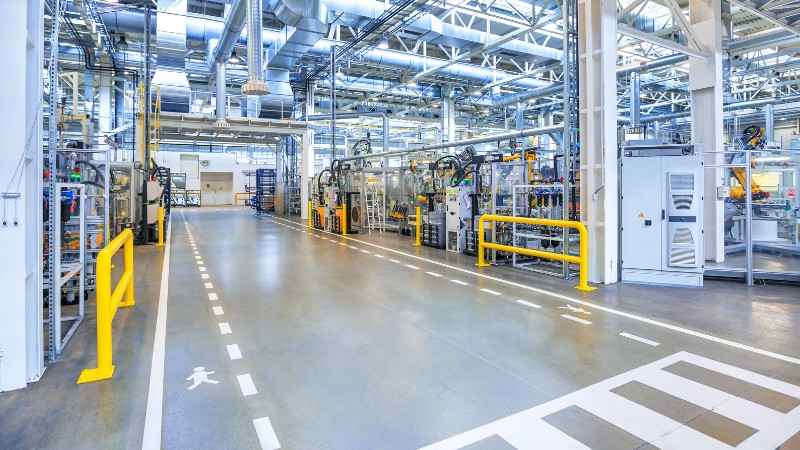
A Fresh Perspective on 5S
5S is a well-known and widely implemented methodology. Its steps—Sort, Set in Order, Shine, Standardise, Sustain—are fundamental to creating an organised and efficient workplace. However, for anyone who feels they have mastered 5S, there are always new layers of value and insight to uncover. This article explores how 5S can be continually leveraged to drive innovation, efficiency, and cultural transformation.
The Deeper Value of 5S
Lean tools, including 5S, have often been the subject of gimmicks or complex graphics to try and make a supposed original point. Many of you, we are sure, will have seen new constructs around 8S, 11S, or even 14S. However, the essence of 5S has proven sufficient for around 50 years to transform from the simplest to the most complex work environments, both inside and outside of manufacturing. This is why we argue that if you learn why the 5 S’s are important and execute them correctly, then nothing else is needed.
Simplicity
The original 5S methodology (Sort, Set in Order, Shine, Standardise, Sustain) is simple and easy to understand. It provides a clear framework for organising workspaces, eliminating waste, and improving efficiency without adding unnecessary complexity. The key to this simplicity is to let all the individuals who work in the area be engaged in the change and particularly understand why the change is needed. In this way, they become their own experts, understanding the process and the need without becoming overcomplicated. As a result of this engagement, they are also far more likely to sustain the change. We often see ‘experts’ parachuted in to run a 5S exercise only to see the area back to its chaotic state, sometimes within hours, as those who will need to own the solution were not integral to building the newly organised 5S area. 5S doesn’t need experts; it needs engagement.
Comprehensive Coverage
The 5S methodology covers a broad range of areas essential for workplace organisation and efficiency. It addresses the key aspects of sorting out unnecessary items, organising necessary items, cleaning, and maintaining workspaces, establishing standardised procedures, and sustaining improvements over time. Don’t get fixated on making things pretty; make them functional, be that in organising a production line or even at home.
In one paper converting plant, a very large spanner was used under a ream cutter. It was the only place that spanner was ever used. In the 5S exercise, the operator said:
I suppose that this spanner will now have to go in the tool store or on a shadow board.”
The operator had always kept the spanner under the machine ‘at the point of use’ where he needed it. As it wasn’t a trip or other hazard, we enabled him to put a shadow right at the place he needed it. He had his tool to hand at the right and most efficient place, and as a bonus, became an advocate for 5S methodology. 5S is about workplace optimisation, not beautification.
Adaptability
The 5S methodology has proven to be highly adaptable and has been applied to various types of commerce and industry, including manufacturing, office settings, healthcare facilities, and even virtual workspaces. You can even 5S your computer desktop! Just using 5 ‘S’s has proven in all these environments to be adaptable, allowing organisations to customise and scale the approach to suit their specific needs and circumstances. So why add unnecessary steps that over-complicate what already works?
Focus on Fundamentals
By focusing on the fundamental 5 steps of workplace organisation and standardisation, the 5S methodology helps build a solid foundation for continuous improvement initiatives. Just 5 ‘S’s used properly will instil discipline, orderliness, and a culture of cleanliness and efficiency within any organisation.
Low Cost and High Impact
Implementing the 5 ‘S’s typically requires minimal financial investment, as it primarily involves changes in behaviour, processes, and workplace layout rather than complex nugatory steps, costly equipment, or new technology. Yet, these simple steps consistently yield significant benefits across businesses in terms of productivity, quality, safety, and employee morale when leadership and teams commit.
Gateway to Further Improvement
While some organisations have chosen to expand beyond the original 5S framework, starting with the proven basics provides a stepping stone for more advanced Lean practices. Once the 5S principles are firmly established and sustained, learning organisations may choose to explore additional Lean tools and techniques to further enhance performance. However, these do not need to include overcomplicating 5S, which has already been proven to work. Expand from 5S into Leader Standard Work, Short Interval Control, Process Confirmation, Visual Management, etc., rather than trying to fix what is not broken.
Focus on Continuous Improvement
The essence of the 5S methodology lies in its emphasis on continuous improvement. By regularly reviewing and refining workplace practices, organisations can continually strive for higher levels of efficiency, quality, and safety without adding more “S’s” to the framework. Continually refine the workplace solution using PDCA, and reinforce what is known to work without adding extra complexity to 5S, which also adds risk.
Summing Up
While some organisations may find value in expanding the 5S methodology to include additional “S’s,” we don’t see the value. With our many years’ of proven experience, we put considerable weight behind the argument that just the original 5 S’s are sufficient, complemented by this methodology’s simplicity, comprehensive nature, adaptability, cost-effectiveness, and focus on continuous improvement.
Implementing the 5S methodology completely and proactively will provide a solid foundation for Lean transformation and drive meaningful improvements in organisational performance. In short, ‘we can put our house in order’ without messing with what already works; keep it simple, commit, sustain, and quickly move on to the next step in your continuous improvement journey.
For more information on how Project7 Consultancy can help you with your Operational Excellence, please contact us.
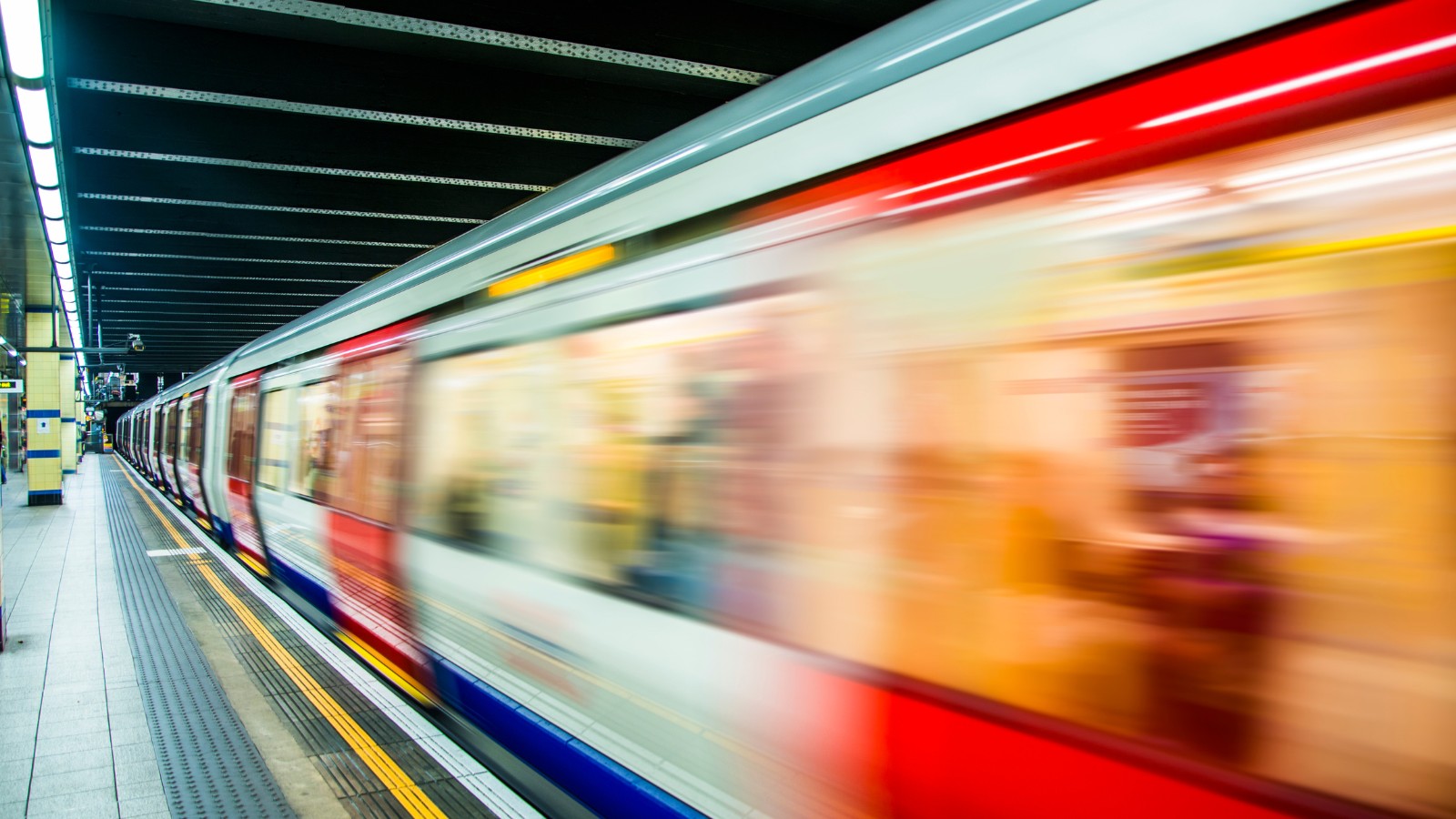
Reflecting on our Journey with London Underground
We previously undertook a significant project with London Underground (LU) to address the issue of staff availability, a critical factor affecting their overall performance and customer satisfaction. Our goal was to help LU enhance their operational efficiency by reducing absenteeism among line operations staff. The impact of this project has been profound, and we are pleased to share our reflections on the journey, the challenges faced, and the outcomes achieved.
Understanding the Challenge
London Underground operates one of the busiest metro systems globally, with over 1.34 billion passengers annually. The performance and reliability of the Tube are vital for the city’s daily functioning. However, LU was experiencing a decline in reliability performance since 2016, primarily due to increasing staff absenteeism.
Absenteeism led to service cancellations, lost customer hours, and significant operational costs, amounting to approximately £48 million per annum.
Our initial assessment identified three main causes of poor staff availability:
- The existing Attendance at Work Policy was not robust enough to address sustained absenteeism effectively.
- The application of the policy by key stakeholders lacked consistency and timeliness.
- There was an inadequate capability among managers to handle absenteeism issues properly.
Implementing Solutions
To tackle these challenges, we began with a comprehensive review of the current absence management processes. This involved deep-diving into individual absence cases, evaluating adherence to procedures, and understanding the mindsets and behaviours of those involved in managing absences.
We piloted a Visual Performance Management (VPM) process in the worst-performing areas, identifying key metrics to monitor and manage performance. Area leaders were coached on conducting regular performance dialogues and using structured problem-solving techniques. This approach led to a significant reduction in absenteeism, from 16% to 9%, within an initial 12-week period.
A Project Management Office (PMO) was established for Line Operations to oversee the improvement programme. We developed and deployed a standardised Tiered Visual Performance Management system across all line operations, ensuring transparency and facilitating regular performance reviews.
Reflecting on the Impact
The impact of our interventions was remarkable. For train operators in Line Operations, the number of employees on restricted duties was reduced from 85 (2.4%) to 35 (1%), a 58% improvement. This reduction resulted in a cost avoidance of £2.4 million in salaries per annum within the first nine months.
Additionally, the overall number of employees off sick across the network decreased by 14.2%, leading to additional cost savings. The reduction in lost customer hours provided a cost avoidance of £5 million, with a projected annual customer benefit of £13 million. In total, the project achieved a cost avoidance of £15.4 million, equating to a 64:1 Return on Investment (ROI).
Lessons Learned and Future Outlook
Reflecting on this project, several key lessons emerged:
- Importance of a Robust Policy: Ensuring that attendance policies are comprehensive and enforceable is critical. A clear policy provides a strong foundation for managing absenteeism effectively.
- Consistency and Timeliness: Applying policies consistently and addressing issues promptly can significantly improve staff availability. Training managers to handle these responsibilities is essential.
- Transparency and Engagement: Implementing visual management tools and fostering regular communication about performance helps create accountability and encourages continuous improvement.
- Holistic Approach: Addressing both the procedural and behavioural aspects of absenteeism management leads to more sustainable improvements.
This project demonstrated that targeted interventions, combined with a commitment to ongoing improvement, can deliver substantial benefits. By enhancing staff availability, LU not only improved their operational efficiency but also boosted customer satisfaction and reduced costs significantly.
Final Thoughts
At Project7 Consultancy, we are committed to helping organisations achieve their strategic goals through performance improvement. Our work with London Underground is an example of the impact that well-executed projects can have on an organisation’s success.
For more information on how Project7 Consultancy can help your organisation achieve similar results, please contact us.
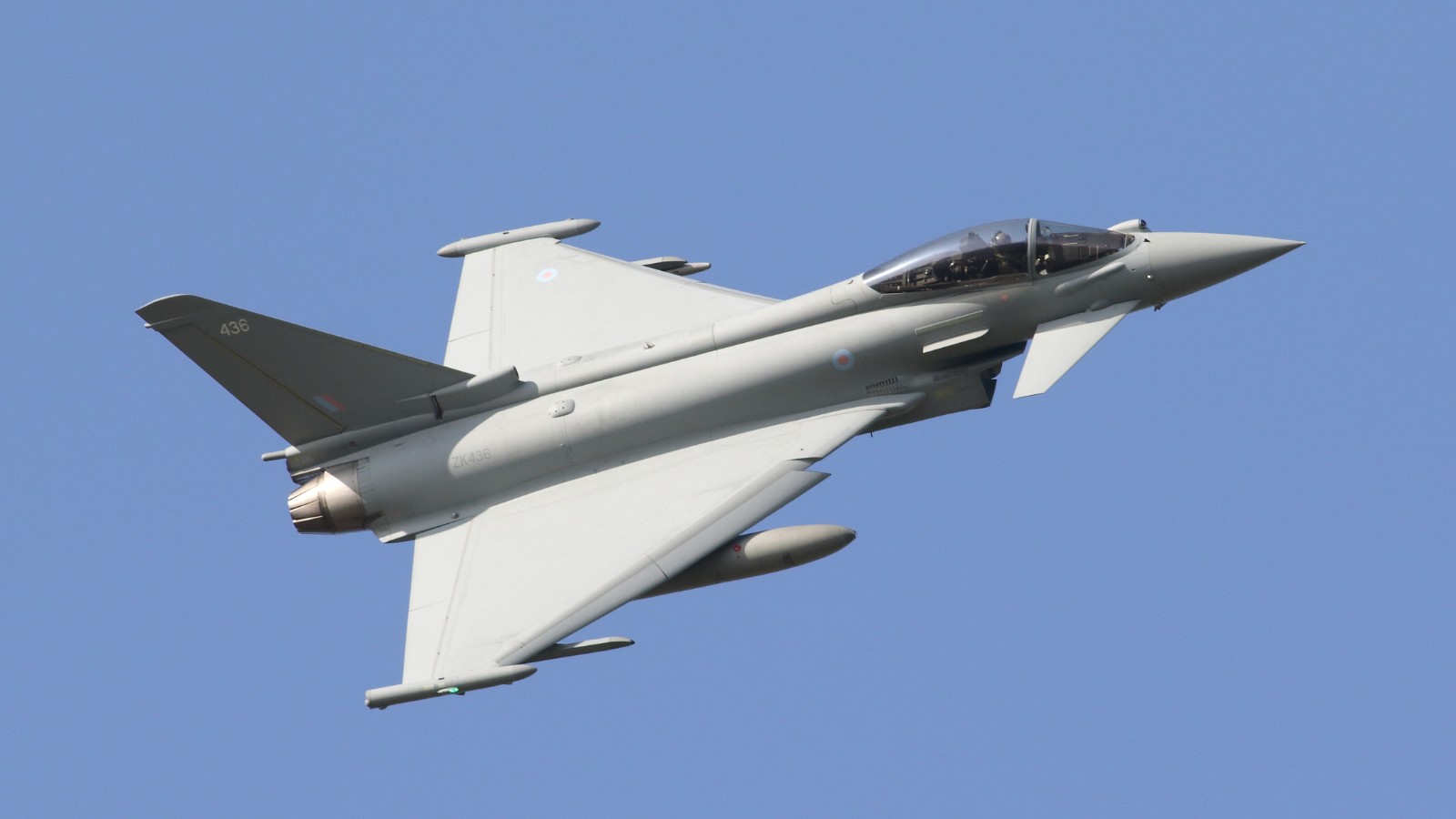
Quality as an Inclusive Culture
At Project7 Consultancy, we understand that quality is not just a department or a checklist; it is a culture that must permeate every level of an organisation. For senior leaders committed to driving excellence, fostering an inclusive quality culture is essential for long-term success and sustainability. Our approach combines industry best practices with insights from Dr Anthony Kenneson-Adams FIoL, a former Engineering Squadron Commander in the Royal Air Force (RAF), who is part of our senior leadership team. Anthony’s military background provides a unique perspective on how quality can be ingrained into the fabric of an organisation.
The Essence of Quality Culture
A quality culture is one where every individual, from top management to the frontline worker, is dedicated to maintaining the highest standards. It’s about creating an environment where quality is everyone’s responsibility and continuous improvement is a fundamental part of the organisational ethos. When we ask Anthony about what he feels are the three core elements to build and sustain quality as an inclusive culture, Anthony cites Training, Communication, and Commitment.
Training: The Backbone of Quality
In the RAF, even simple tasks like servicing anti-collision lights were critical to flight safety, demonstrating that quality starts with the basics,” says Anthony.
Effective training is the cornerstone of a robust quality culture. It equips employees with the knowledge and skills necessary to perform their tasks to the highest standards. Reflecting on Anthony’s military background, where training is rigorous and comprehensive, we emphasise the importance of precision and responsibility from the start.
- Customised Training Programs: Tailor training to meet the specific needs of your workforce.
- Continuous Learning: Encourage a culture of continuous learning. Regularly update training materials to reflect the latest industry standards and technological advancements.
- Practical Application: Ensure training includes practical applications. Hands-on experience reinforces theoretical knowledge and helps employees understand the real-world implications of their work.
Communication: The Key to Engagement
Open and effective communication is vital in fostering a quality culture. It ensures that everyone is on the same page and that potential issues are addressed proactively. In the RAF, Anthony learned the importance of open communication channels and the confidence to voice concerns without fear of retribution, which were critical in maintaining engineering quality standards.
- Transparent Channels: Establish transparent communication channels where employees feel safe to voice concerns and provide feedback without fear of retribution.
- Regular Updates: Keep the team informed about quality goals, progress, and any changes in procedures. Regular updates help maintain focus and alignment.
- Inclusive Dialogue: Promote an inclusive dialogue where ideas and suggestions are welcomed. Encourage employees at all levels to participate in discussions about quality improvements.
Commitment: The Foundation of Excellence
Commitment to quality must start at the top and cascade throughout the organisation. Leaders play a critical role in setting the tone and demonstrating their dedication to quality. In the RAF, there is no dedicated quality manager or department; instead, a culture of individual and collective commitment to quality permeated every rank and role. Anthony’s experience underscores the importance of this collective responsibility.
- Lead by Example: Senior leaders should exemplify quality in their actions and decisions. This sets a powerful precedent for the rest of the organisation.
- Integrated Quality Goals: Integrate quality goals into the overall business strategy. Ensure that quality is a key performance indicator for all departments.
- Empower Employees: Empower employees by providing the necessary resources and autonomy to make decisions that enhance quality. Trust and support from leadership foster a sense of ownership and responsibility.
Implementing Quality Culture in Your Organisation
Implementing a quality culture requires a strategic approach and consistent effort. Here are some steps senior leaders can take to embed quality into their organisation’s fabric:
- Assessment and Benchmarking: Start with a thorough assessment of your current quality practices. Benchmark against industry standards to identify areas for improvement.
- Strategic Planning: Develop a strategic plan that outlines clear quality objectives and the steps needed to achieve them. Ensure alignment with the overall business strategy.
- Engagement and Buy-In: Engage employees at all levels in the quality journey. Secure buy-in by highlighting the benefits of a quality culture, such as improved performance, customer satisfaction, and competitive advantage.
- Monitoring and Evaluation: Implement robust monitoring and evaluation systems to track progress. Regularly review and adjust strategies to ensure continuous improvement.
At Project7 Consultancy, we believe that an inclusive quality culture is the foundation of operational excellence. By focusing on training, communication, and commitment, senior leaders can transform their organisations and achieve sustainable success. Quality should not be seen as an isolated function but as an integral part of every process and decision.
By embedding these principles into your organisation, and drawing on insights from leaders like Dr Anthony Kenneson-Adams with a rich military background, you can drive performance, enhance customer satisfaction, and secure a competitive advantage in the marketplace.