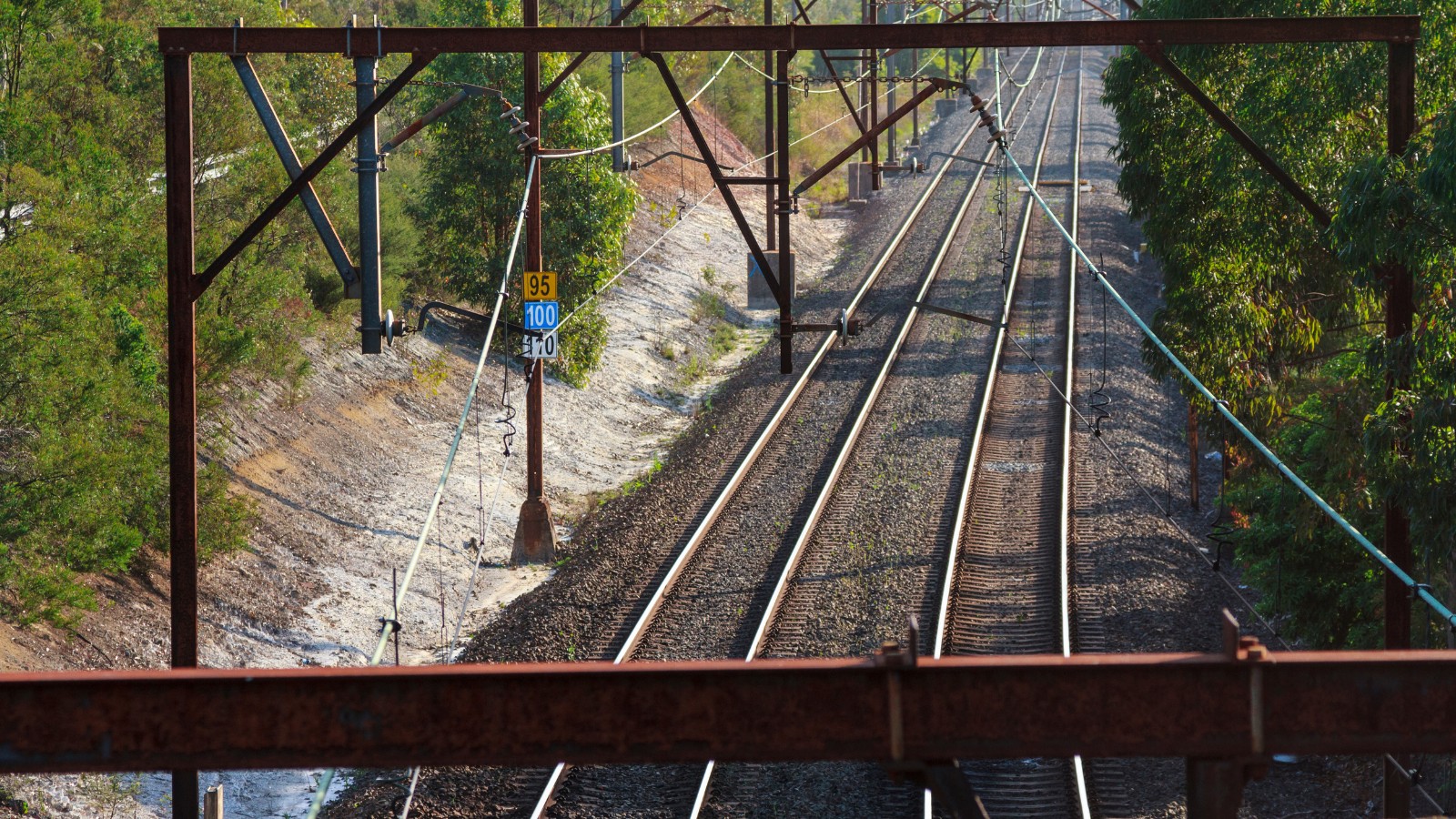
Production Planning Process Improvement Project
Delivering impactful change that enhances operational efficiency and delivers measurable results is critical for any large-scale organisation. In one of our previous projects, we helped transform the production planning processes at a major suburban rail network in New South Wales, Australia. This reflection explores the challenges faced, solutions implemented, and the outcomes achieved throughout the collaboration.
The company operates over 815 km of track and 178 stations, serving millions of passengers annually. The Major Works division, responsible for maintaining and upgrading the rail network, was undergoing a transformational reform to improve the efficiency and performance of its operations. The team engaged Project7 to assist in developing a Production Planning Process that would enhance the delivery of their annual works programme and drive a cultural shift towards better coordination and commercial focus.
Challenges
The company faced several operational challenges that hindered their ability to meet service and maintenance goals. These included:
- Incomplete Work and Rework: Many projects were not completed within the allotted time, leading to repeated site visits, rework, and increased costs.
- Poor Forecasting: A lack of visibility into the work demand forecast from the annual works programme made it difficult to plan effectively, resulting in delays.
- Safety Concerns: Inconsistent pre-work site inspections and safety briefings led to a high Total Recordable Injury Frequency Rate (TRIFR).
- Unstructured Planning: An inconsistent approach to planning across teams led to resource underutilisation and poor communication within and between departments.
- Lack of Accountability: The absence of structured pre- and post-possession reviews meant that lessons were not learned, and planning was not adjusted for future projects.
Solutions
We undertook a comprehensive diagnostic phase to understand the current state of Project Operations. Through collaborative workshops and process mapping exercises with the delivery teams, we developed a robust Production Planning Process focused on improving safety, quality, delivery, cost, and people performance metrics.
Key solutions implemented included:
- Policy Deployment: We aligned corporate goals with actionable targets for staff at all levels, ensuring everyone was working towards common objectives.
- Visual Performance Management: Standardised visual management boards were introduced across different teams (Track, Signals, Electrical), providing a transparent system to track progress and communicate project status.
- Structured Performance Reviews: Weekly reviews led by team managers ensured accountability and provided regular updates on the status of each project, improving ownership and responsibility across the team.
- Safety and Pre-Work Improvements: Safety briefings and pre-works meetings were reintroduced, along with a Short Interval Control system to track plan versus actual performance in real-time.
- Clear Communication Channels: Improved communication within and across teams was achieved by integrating Team Leaders into the production planning process, helping to streamline project execution.
Impact on Performance
The implementation of the Production Planning Process led to substantial improvements in operational efficiency, cost control, and safety:
- 40% Reduction in TRIFR: Consistent safety briefings and improved pre-work site inspections led to a significant reduction in injuries.
- 1% Increase in Delivery: The Annual Works Programme saw a 1% increase in completion, reflecting a more efficient project execution process.
- $2.5 Million in Cost Savings: Continuous improvement initiatives identified significant opportunities for cost reduction, resulting in a 6:1 Return on Investment.
- $13 Million Reduction in Maintenance Costs: Net operating costs came in $13 million under budget, highlighting the financial impact of better planning and execution.
- 10% Improvement in Post-Works Asset-Related Delays: Improved planning and coordination resulted in fewer delays following project completion, enhancing service reliability.
Final Thoughts
This project demonstrated how structured planning, clear communication, and consistent performance management can lead to significant operational improvements. By implementing a clear Production Planning Process and encouraging a culture of accountability, this New South Wales based train operator saw improved efficiency, reduced costs, and enhanced safety, ultimately delivering a better service to its passengers.
At Project7 Consultancy, we remain dedicated to helping organisations achieve their operational goals through tailored solutions and strategic interventions. For more information on how we can help your organisation achieve similar success, contact us directly.